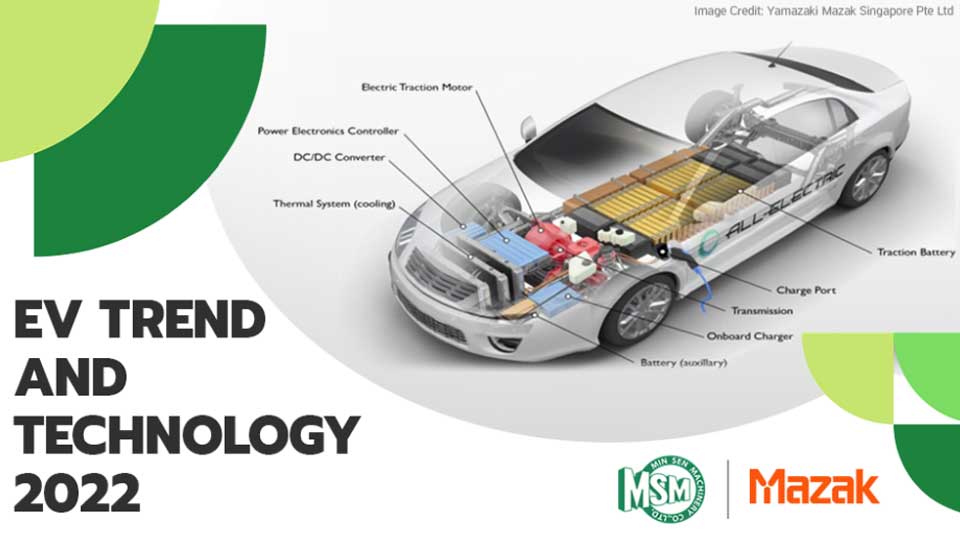
Min Sen ร่วม Mazak เปิด “EV Trend and Technology 2022”
เป็นที่กังวลว่า การมาถึงของยุคอีวีจะเป็นขาลงของผู้ผลิตชิ้นส่วนยานยนต์ ข้อเท็จจริงในประเด็นนี้จะเป็นเช่นไร มาร่วมไขประเด็นในบทความนี้ที่รวบรวมจากงานสัมมนาเชิงเทคโนโลยีที่ร่วมจัดโดย Min Sen Machinery และ Mazak (Thailand) สองบริษัทชั้นนำด้านเครื่องจักรกล
ปัจจุบัน ประเทศไทยยังคงอยู่ในตำแหน่งผู้ผลิตยานยนต์และจักรยานยนต์รายใหญ่ที่สุดในอาเซียน แต่หากเอ่ยถึงรถยนต์ไฟฟ้าแล้ว ข้อมูลจากกระทรวงอุตสาหกรรมเปิดเผยว่า ในช่วงจนถึงปี 2020 ยอดผลิตรถยนต์ไฟฟ้าในไทยยังไม่สูงมากนัก มีเพียงราว 186,000 คัน แต่จะมีการเติบโตอย่างต่อเนื่อง
โดยคาดการณ์ว่า ในปี 2025 จะมียอดผลิตรถยนต์ไฟฟ้าในไทย 1.05 ล้านคัน ก่อนเพิ่มเป็น 6.22 ล้านคันในปี 2030 และ 18.41 ล้านคันในปี 2035 แสดงให้เห็นถึงการเพิ่มขึ้นของรถยนต์ไฟฟ้าในไทยอย่างเด่นชัด
อย่างไรก็ตาม คำกล่าวที่ว่า “รถยนต์ไฟฟ้ามีชิ้นส่วนเพียง 1 ใน 3 ของรถยนต์สันดาป” ทำให้เกิดความกังวลในหมู่ผู้ผลิตชิ้นส่วนรายหลายถึงเรื่องในอนาคตว่าจะเป็นอย่างไรต่อไป
โดยเมื่อวันที่ 5 สิงหาคม 2022 บริษัท มินเซนแมชีนเนอรี่ จำกัด ร่วมกับ บริษัท มาซัค (ประเทศไทย) จำกัด และพันธมิตร จัดงานสัมมนาเชิงเทคโนโลยี ชูหัวข้อ “EV trend and technology 2022” เป็นธีมงานครั้งนี้ เพื่อให้ข้อมูลเชิงลึกแก่นักอุตสาหกรรม 50 รายที่มาร่วมไขข้องใจ และเปิดรับโอกาสใหม่ที่มาพร้อมกับยุคอีวี
นายก่อเกียรติ ทรัพย์สมพล ผู้ช่วยกรรมการผู้จัดการ ฝ่ายเครื่องมือกล บริษัท มินเซนแมชีนเนอรี่ จำกัด เปิดเผยว่า ในช่วงสามสิบปีมาที่ผ่านมา วงการเครื่องจักรมักพูดถึง High Speed Machining และตามด้วยเรื่อง 3D Printer และเมื่อยี่สิบปีก่อน เราพูดกันเรื่อง Industry 4.0 จนมาถึงไม่กี่ปีมานี้ เทรนด์ที่เราพูดกันเป็นเรื่องของเทคโนโลยีใหม่ในการผลิตชิ้นส่วนรถยนต์ไฟฟ้า
นี่จึงเป็นการจุดประเด็นสู่หัวข้อไฮไลต์ของงาน “EV trend and technology 2022” ซึ่งบรรยายโดย Mr. K.S.Chong ผู้อำนวยการอาวุโส บริษัท Yamazaki Mazak Singapore
การแมชชีนนิ่ง “ชิ้นส่วนรถยนต์ไฟฟ้า” ต่างจาก “ชิ้นส่วนรถยนต์สันดาปภายใน” อย่างไร?
แม้ว่ารถยนต์ไฟฟ้า (EV) จะทำให้ชิ้นส่วนที่อยู่ในเครื่องยนต์สันดาปภายใน (ICE) ซึ่งส่วนใหญ่แล้วเป็นงานแมชชีนนิ่งหายไป เนื่องจากถูกทดแทนด้วยมอเตอร์ไฟฟ้า แต่ชิ้นส่วนแมชชีนนิ่งที่อยู่ในระบบส่งกำลัง (Powertrain System) จะยังคงอยู่
และเพื่อตอบโจทย์การลดน้ำหนักยานยนต์ให้รถอีวีสามารถใช้พลังงานไฟฟ้าขับเคลื่อนในระยะทางที่ไกลขึ้น ทำให้ชิ้นส่วนของรถยนต์ไฟฟ้าเปลี่ยนไปใช้วัสดุที่มีน้ำหนักเบา เช่น พลาสติก วัสดุวิศวกรรมสมัยใหม่อื่น ๆ ความต้องการนี้จะทำให้มีการผลิตแม่พิมพ์สำหรับชิ้นส่วนพลาสติกเพิ่มขึ้น รวมไปถึงการปรับเปลี่ยนเทคโนโลยีในการแมชชินนิ่งวัสดุชนิดใหม่
อีกความเปลี่ยนแปลงที่จะเกิดขึ้น คือ ตัวถังยานยนต์ที่มีความซับซ้อนมากกว่าที่ผ่านมาและมีขนาดใหญ่ขึ้น อย่างรถเทสล่าก็เป็นตัวอย่างที่บ่งชี้ได้ เนื่องจากผู้ผลิตยานยนต์ต้องการลดจำนวนชิ้นส่วนให้เหลือน้อยที่สุดเพื่อใช้เวลาในการประกอบยานยนต์ให้เร็วยิ่งขึ้นและมีต้นทุนต่ำลง ชิ้นส่วนที่ใหญ่และซับซ้อนขึ้นทำให้การผลิตแม่พิมพ์มีความยากกว่าเดิม จนเครื่อง 3 แกนไม่อาจตอบโจทย์การผลิตแม่พิมพ์อีกต่อไป อีกทั้งในงานประกอบชิ้นส่วนจะมีความต้องการใช้อุปกรณ์จับยึด Jig & Fixture เพิ่มขึ้นอย่างมาก
ทั้งหมดนี้เป็นแค่ตัวอย่างส่วนหนึ่งเท่านั้น ชิ้นส่วนที่ต้องผลิตด้วยการแมชชีนนิ่งยังไม่หายไปไหน ชิ้นส่วนที่ต้องผลิตด้วยแม่พิมพ์ก็ยังคงอยู่ ซึ่งนั่นหมายความว่า ไม่ใช่เพียงแค่การผลิตชิ้นส่วนอีวีเท่านั้น แต่ผู้ผลิตยังต้องผลิตแม่พิมพ์เพิ่มขึ้นอีกด้วย โดยชิ้นส่วนและแม่พิมพ์เหล่านี้ต้องใช้เครื่อง CNC, เครื่องมิลลิ่ง, และเครื่องแมชชีนนิ่งเซ็นเตอร์ 3 - 5 แกนในการผลิต
นอกจากนี้ รถอีวียังมีระบบแบตเตอรี่ซึ่งเป็นส่วนสำคัญที่เพิ่มเข้ามา ชิ้นส่วนเหล่านี้ยังจำเป็นต้องผลิตด้วยวิธีการแมชชีนนิ่งอยู่ ยกตัวอย่างเช่น กล่องแบตเตอรี่ (Battery casing) ซึ่งใช้วัสดุเป็นอะลูมิเนียม ทำให้เกิดความต้องการแม่พิมพ์ไดคาสติ้ง โดยเฉพาะกระบวนการผลิตแบบ High-pressure Die Casting
High-pressure Die Casting จะมีความต้องการมากขึ้นในอนาคต
“High-pressure Die Casting (HPDC) คือ กระบวนการผลิตชิ้นงานที่โลหะหลอมเหลวถูกฉีดเข้าไปยังแม่พิมพ์ซึ่งถูกปิดไว้ด้วยแรงดันสูงจนกว่าโลหะหลอมเหลวจะแข็งตัว”
ชิ้นส่วนใด ๆ ก็ตามที่ผลิตด้วยกระบวนการ High-pressure Die Casting ล้วนต้องการแม่พิมพ์ และแม่พิมพ์เหล่านี้ก็ผลิตด้วยการแมชชีนนิ่ง และด้วยลักษณะของชิ้นส่วนที่บางลง เบาลง ซับซ้อนยิ่งขึ้น ทำให้กระบวนการผลิตแม่พิมพ์มีความท้าทายกว่าการผลิตแม่พิมพ์ชิ้นส่วนเครื่องยนต์สันดาปที่ผ่านมาเป็นอย่างมาก
ยกตัวอย่างเช่นกล่องแบตเตอรี่ ซึ่งเป็นชิ้นส่วนที่มีขนาดใหญ่ มีรูปทรงซับซ้อน ผลิตจากอะลูมิเนียมที่มีความบาง อีกทั้งยังมีรายละเอียดในหลายตำแหน่งที่ต้องมีชิ้นส่วนอื่นมาประกอบเพิ่มเติม ทำให้เครื่องจักรที่ใช้ในการผลิตชิ้นส่วนเหล่านี้มีขนาดใหญ่ขึ้น เกิดความต้องการแม่พิมพ์ขนาดใหญ่สำหรับผลิตชิ้นส่วนเหล่านี้
และในชิ้นส่วนอื่น ๆ อย่างกล่องเฟือง กล่องอินเวอร์เตอร์ และอุปกรณ์ชาร์จไฟยานยนต์ จะนำไปสู่ความต้องการ Die-casting Machine ขนาดกลางและขนาดใหญ่ ซึ่งหมายถึงความต้องการเครื่องจักรขนาดใหญ่มากขึ้นตามไปด้วย
ในกรณีของเทสล่าที่รวมชิ้นส่วนต่าง ๆ เข้าด้วยกันเป็นชิ้นเดียว ทำให้กระบวนการผลิตชิ้นส่วนมีความซับซ้อนยิ่งขึ้น และต้องการเครื่อง 5 แกนขนาดใหญ่สำหรับผลิตแม่พิมพ์ High-pressure Die Casting
อีกหนึ่งตัวอย่างในการผลิตชิ้นส่วนรถอีวีที่ถูกหยิบยกขึ้นมาในงานสัมมนาครั้งนี้ คือการผลิตมอเตอร์รถยนต์ไฟฟ้า ซึ่งมี Stator และ Rotor เป็นชิ้นส่วนสำคัญ
ความยากในการผลิตชิ้นส่วนเหล่านี้คือการเซ็ตให้ได้ระยะที่เหมาะสม ทำให้มีการใช้หุ่นยนต์ในการจับยึดชิ้นงาน ใช้หัวโพรบวัดระยะอย่างแม่นยำ และใช้เครื่องกลึงของ Mazak ในการแมชชีนส่วนหัวและส่วนท้ายของชิ้นงาน
อีกตัวอย่างหนึ่งคือการผลิต Motor Housing ซึ่งผนังชิ้นส่วนมีความบางเป็นอย่างมาก อีกทั้งชิ้นส่วนยังมีความหลากหลายไปตามรถแต่ละรุ่น จึงได้เลือกใช้ระบบการผลิตแบบออโตเมชันที่ยืดหยุ่น ด้วยการใช้หุ่นยนต์ 6 แกนในการโหลดชิ้นงาน และใช้เซนเซอร์ตรวจวัดว่าชิ้นงานสองด้านประกบกันได้สนิทแน่นหรือไม่ผ่านการเป่าลมลงบนชิ้นงาน
Friction Stir Welding อนาคตของการเชื่อมชิ้นส่วนรถยนต์ไฟฟ้า
“Friction Stir Welding (FSW) คือ กระบวนการเชื่อมชิ้นงานที่ใช้แรงเสียดทานเพื่อเชื่อมชิ้นงานเข้าด้วยกันโดยไม่ใช้ความร้อนและไม่เติมเนื้อโลหะ”
กระบวนการเชื่อมแบบ Friction Stir Welding เป็นกระบวนการสำคัญที่ต้องใช้ในการเชื่อมชิ้นส่วนรถยนต์ไฟฟ้า เนื่องจากโลหะที่เชื่อมแบบ FSW จะใช้อุณหภูมิเพียง 300°C ในขณะที่การเชื่อมแบบทั่วไปใช้อุณหภูมิที่ 1,000°C ดังนั้น ชิ้นงานที่เชื่อมแบบ FSW จะไม่เสียรูปทรง และยังสามารถเชื่อมชิ้นงานจากวัสดุต่างชนิดเขาหากันได้อีกด้วย นอกจากนี้ ยังมีความปลอดภัยสูงเพราะไม่มีการใช้ก๊าซ พลาสม่า และอื่น ๆ
สำหรับชิ้นส่วนที่สามารถผลิตด้วยกระบวนการนี้ เช่น โครงรถที่ต้องการความคงทน ชิ้นส่วนระบบหล่อเย็น และอื่น ๆ
ตัวอย่างการเชื่อมชิ้นส่วนด้วยวิธี FSW ที่หยิบยกมาคือการเชื่อมฝาครอบหม้อน้ำเข้ากับตัวหม้อน้ำ เพื่อให้เป็นชิ้นส่วนชิ้นเดียวกัน มีรูระบายความร้อนและท่อคูลแลนต์ในตัว ไม่มีน็อตเพื่อลดน้ำหนัก ไม่มีฉนวนซึ่งเสื่อมสภาพได้ง่ายจึงไม่จำเป็นต้องเปลี่ยนฉนวนอีกต่อไป และมีอายุการใช้งานยาวนาน
การเชื่อมแบบ FSW ยังสามารถนำไปใช้ในการเชื่อมชิ้นงานในอุตสาหกรรมอื่น ๆ ได้อีกด้วย เช่น การเชื่อมโครงสร้างอากาศยาน การเชื่อมชิ้นส่วนเซมิคอนดักเตอร์ การเชื่อมชิ้นส่วนรถไฟ ไปจนถึงการเชื่อมโครงสร้างอะลูมิเนียมในงานก่อสร้าง รวมไปถึงชิ้นส่วนยานยนต์อื่น ๆ เช่น ตัวถังอะลูมิเนียมเพื่อช่วยลดน้ำหนักยานยนต์ให้ประหยัดเชื้อเพลิงได้มากขึ้นอีกด้วย
นอกจากนี้ Mazak ยังได้พัฒนาแนวคิด Stationary Shoulder Concept FSW (SSFSW) เข้าเป็นส่วนหนึ่งของเครื่อง Machining Center เช่น ในรุ่น FJV-60/80 FSW และ VTC-530/20 FSW ซึ่งได้แยกส่วนของ Shoulder และ Probe ออกจากกัน ทำให้ระหว่างทำการเชื่อม แรงจะถูกส่งไปยัง Shoulder แทนสปินเดิล เพื่อให้สปินเดิลรับภาระน้อยลงและมีอายุการใช้งานยาวนานยิ่งขึ้น อีกทั้งระบบรับแรงนี้ยังช่วยให้รอยเชื่อมมีความสม่ำเสมอมากขึ้นอีกด้วย
นี่เป็นเพียงบางส่วนที่คัดมาแบ่งปันให้ผู้ผลิตชิ้นส่วนยานยนต์ได้มองเห็นโอกาสในชิ้นส่วนรถยนต์ไฟฟ้า หากท่านใดที่จะเดินหน้าเรื่องนี้สามารถขอรับคำปรึกษาด้านเทคโนโลยีกับทางบริษัทมินเซนแมชีนเนอรี่ได้