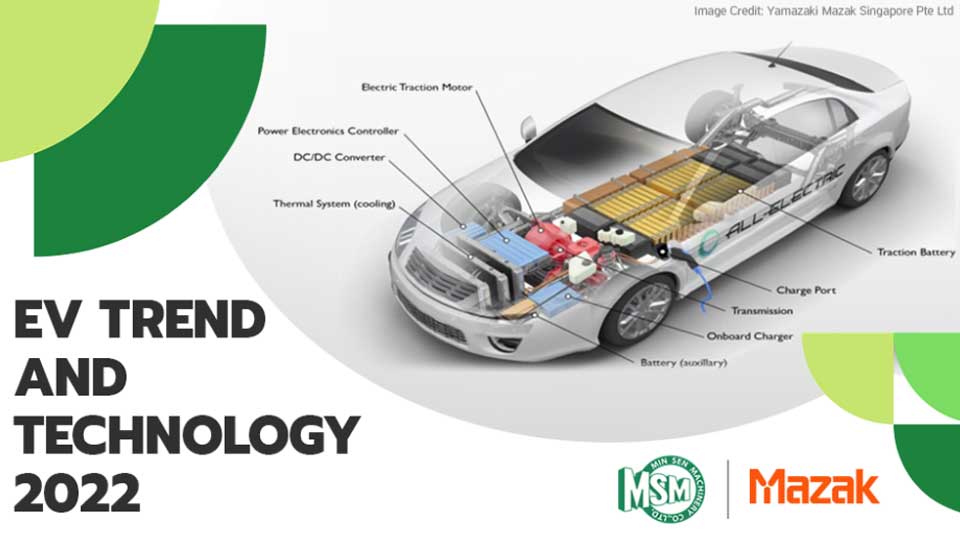
Min Sen joins Mazak to launch “EV Trend and Technology 2022”
As it is concerning that the introduction of the EV age would result in a decline for manufacturers of automotive components, what will the facts be on this matter? Let's examine the issues in this article compiled from a technology seminar that two major machinery businesses, Min Sen Machinery and Mazak (Thailand), jointly hosted.
Currently, Thailand continues to be ASEAN's top manufacturer of cars and motorcycles. But when it comes to electric vehicles, according to data from the Ministry of Industry, only roughly 186,000 electric cars were produced in Thailand up to 2020, which is a rather low number. However, this number will continue to rise.
The manufacturing of electric vehicles is predicted to develop significantly in Thailand, reaching 1.05 million vehicles by 2025, 6.22 million by 2030, and 18.41 million by 2035.
However, since "electric vehicles are made up of barely one-third of the parts of combustion ones," manufacturers of auto parts are worried about the future.
To give the insights and allay their concerns to be open to new prospects brought on by the EV era, Min Sen Machinery Co., Ltd., Mazak (Thailand) Co., Ltd., and partners hosted an "EV trend and technology 2022" technology seminar for 50 industrialists on August 5, 2022.
Mr. Korkiat Subsompon, Vice President, Machine Tool Department, Min Sen Machinery Co., Ltd., claims that over the past 30 years, high speed machining and 3D printers have been topics of discussion in the machinery business. Then, for the past 20 years, the topic has become Industry 4.0. It is only in the last few years that we have started to talk about new technologies for manufacturing electric car components.
This is how the highlight topic of “EV trend and technology 2022” was sparked, which was led by Mr. K.S. Chong, Senior Director of Yamazaki Mazak Singapore.
What distinguishes the machining of "electric vehicle parts" from "internal combustion vehicle parts"?
Despite the fact that EV cars lose the internal combustion engines (ICEs), which are primarily machined components, and replace them with an electric motor, the machined components of the powertrain system will continue to exist.
Electric vehicle parts are moving to lightweight materials like plastics and other contemporary engineering materials to satisfy the demand to lower the weight of EV vehicles so they can use electric power to go longer distances. More molds are being produced for plastic parts as a result of this demand, which is also influencing how new materials are machined.
The bigger and more complicated vehicle body is another modification that will take place. An example is the Tesla car. This is because automakers aim to employ the fewest possible parts in order to reduce costs and speed up assembly. Mold manufacturing becomes more challenging due to larger and more intricate pieces, and 3-axis machines are no longer sufficient. Jigs and fixtures will also be in extremely high demand for the assembling process.
These are only a few examples. There are still parts that require machining to create them. There are still parts that need to be made using molds. It implies that manufacturers must both produce more molds and more EV parts. These parts and molds must be made using a 3-5 axis machining center, CNC, and milling.
Also, the EV cars have the battery system as an essential additional component. The parts of the system require machining. For instance, the manufacturing of metal battery housings needs die casting molds, particularly the high-pressure die casting.
High-pressure die casting will be in higher demand
“High-pressure die casting (HPDC) is the manufacturing process of a part where molten metal is injected into a mold that is sealed by high pressure until the molten metal hardens.”
Any part that is manufactured by the process of high-pressure die casting requires a mold, and these molds are made through machining. With the appearance of thinner, lighter, more complex parts, this makes the mold manufacturing process much more challenging than the previous combustion engine parts dies.
The battery box, for instance, is a sizable, intricately shaped piece of thin aluminum with numerous details that need to be assembled with other parts. Therefore, larger machinery and molds are needed to make these parts.
Other parts such as gear boxes, inverter boxes, and automotive chargers will increase the demand for medium and large die-casting machines. This means the need for larger machines as well.
In the case of Tesla, the parts are put together into a single piece. This makes the manufacturing process of parts more complicated and needs a large 5-axis machine for high-pressure die casting mold production.
Another example of manufacturing EV parts addressed in this seminar is the manufacturing of electric car motors, which have a stator and a rotor as key components.
The challenge in manufacturing these components is positioning them at the proper distance. This can be made possible by utilizing a robot to hold the workpiece, measuring the distance precisely with the probe, and machining the workpiece using Mazak lathes on both ends.
Another example is the manufacture of motor housings, where the walls are extremely thin and vary based on model. The winning choice is a flexible automated manufacturing system with a 6-axis robot to load the workpiece and a sensor to determine if the two sides of the workpiece are tightly coupled with each other by blowing air onto the workpiece.
Friction stir welding is the future of welding electric vehicle parts
"Friction stir welding (FSW) is a welding technique that uses friction rather than heat or additional metal to fuse the workpieces together."
Friction stir welding is an important process required for welding electric vehicle parts. Since FSW welds metal only at a temperature of 300 °C, as opposed to that of conventional welding at 1,000 °C, FSW will not deform the parts and can also be used to weld workpieces of different materials. It is also highly safe because it does not use gas, plasma, etc.
Parts that can be produced by this process are chassis that require durability, cooling system parts, etc.
An example of FSW mentioned in the seminar is the radiator cover welded to the radiator body to create one unit with a cooling hole and an integrated coolant pipe. There are no nuts in it to lighten the weight. It has a long service life and no easily degradable insulation, therefore there is no need to replace the insulation.
Aside from automotive parts like aluminum bodywork, which can help make a car lighter and more fuel-efficient, FSW can also be utilized for workpieces in other industries like aircraft structures, semiconductor components, railway components, and aluminum construction structures.
In addition, Mazak has developed and integrated the stationary shoulder concept FSW (SSFSW) into the machining center, where the shoulder and probe in the FJV-60/80 FSW and VTC-530/20 FSW models are separate. As a result, during welding, the force is applied to the shoulder rather than the spindle, which reduces the load on the spindle and extends the spindle’s service life. This load-bearing technology also enables welds to be made more consistently.
These are just a handful of the examples we choose to give to auto parts manufacturers so they can see the potential of EV parts. Those who want to move forward with this can contact Min Sen Machinery for technology consultation.