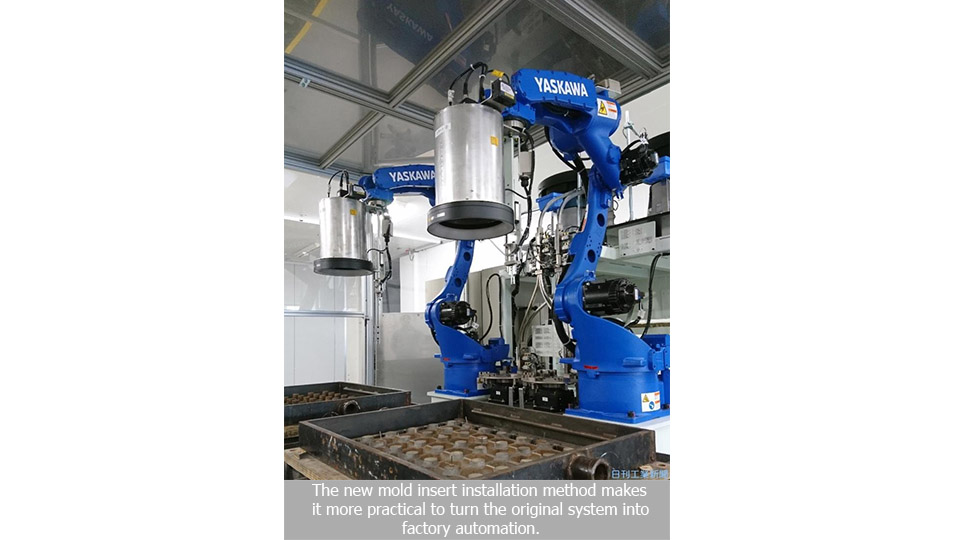
NIKKO KINZOKU and Factory Automation for Small Batch Production
NIKKO KINZOKU, the manufacturer of heat-resistant cast steel for automotive industry in Japan, has made some adjustments to the manufacturing process. Two handling robots were assembled and an image processing system was installed onto the heat treatment tray, which was later used as the mold insert installation aid, leading to a solution to labor shortage in small batch production of various types. In the past, it was difficult to implement the automation technology in the original manufacturing process. These adjustments cost 50 million yen and the installation is expected to complete in 2018.
NIKKO KINZOKU has decided to install a plastic “holder” to prevent mistakes and to reduce labor workload. The original holder was replaced by a new automated holder; the robots were manufactured by Yaskawa and the image processing system was used to measure the position of the holder before using the handling robot to install the mold inserts. Consequently, there will be no need to measure the position of mold inserts every time the mold is replaced, making it possible to implement the factory automation.
Initially, at least 2 robots will be used with wooden molds, 980 mm long by 980 mm wide, with upper and lower plates. In addition, with 2 additional robots, they can be used with bigger molds. For small batch production, the manufacturing process can be adjusted to allow workers to work manually for faster workflow. This is the reason why this system can be implemented to work with the existing manufacturing system smoothly, where workers can install the mold inserts themselves.
In the casting process, as high-temperature liquid metal flow through a sand casting mold, the thick parts are managed to transfer the same amount of heat as the other parts by installing the mold inserts. NIKKO KINZOKU has installed the mold inserts on wooden flasks. The Chairman Shotarou Satou said, “Sometimes, this process requires up to 200 mold inserts.” In the past, workers had to work on this task manually and it took a lot of time and labor. Moreover, it was the most difficult process to be replaced by the factory automation for small batch production.