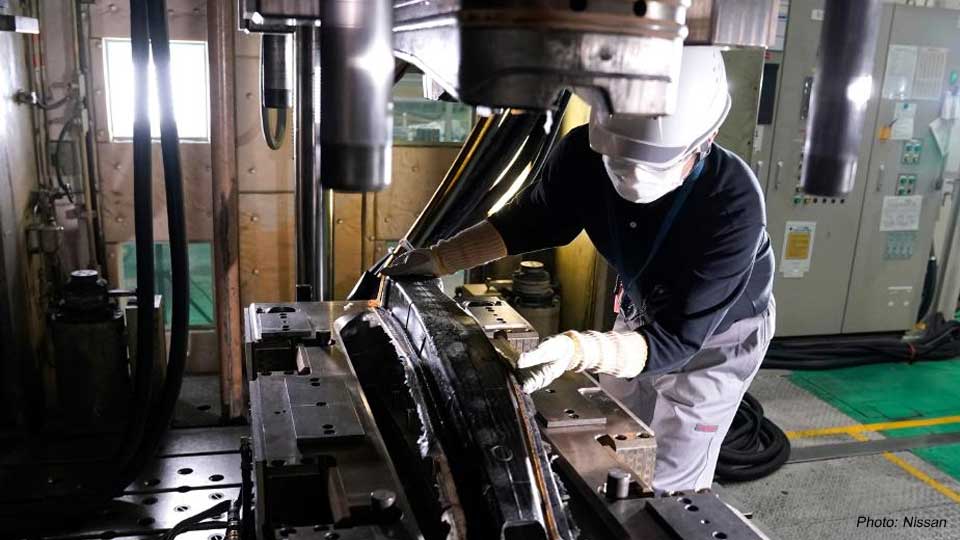
นิสสันรุดหน้า ลุยชิ้นส่วน CFRP ผลิตแบบ Mass Production
เมื่อวันที่ 3 กันยายน 2020 นิสสัน มอเตอร์ (Nissan Motor) ประกาศความสำเร็จอีกขั้นในการผลิตชิ้นส่วนยานยนต์จากวัสดุ Carbon Fiber Reinforced Polymer (CFRP) ซึ่งเป็นวัสดุที่ถูกใช้ในการผลิตชิ้นส่วนอากาศยาน, จรวด, และรถสปอร์ต ซึ่งถูกคาดหวังว่าจะกลายเป็นวัสดุสำคัญในการลดน้ำหนักยานยนต์ โดยเฉพาะรถยนต์ไฟฟ้า (Electric Vehicles: EV)
วิธีการในการผลิตชิ้นส่วนยานยนต์จาก CFRP ที่นิสสันใช้ คือ Compression Resin Transfer Molding ซึ่งเป็นวิธีการทำแม่พิมพ์อัดเรซิ่นที่มีอยู่แต่ดั้งเดิม โดยเริ่มจากขึ้นรูปวัสดุคาร์บอนไฟเบอร์ให้ได้รูปทรงตามต้องการ โดยเว้นช่องว่างระหว่างชิ้นส่วนกับแม่พิมพ์ไว้ จากนั้นจึงฉีดวัสดุเรซิ่นตามเข้าไปและปล่อยให้แข็งตัว
ทีมวิศวกรของนิสสันได้พัฒนากระบวนการนี้เพิ่มเติมด้วยการติดตั้งเซนเซอร์ไว้ภายในแม่พิมพ์ และใช้แม่พิมพ์ที่โปร่งใส ทำให้สามารถมองเห็น และตรวจวัดการไหลของเรซิ่นในแม่พิมพ์ได้โดยละเอียด ช่วยให้การจำลองการซึมผ่าน (Permeability) ของเรซิ่นในคาร์บอนไฟเบอร์มีความแม่นยำมากยิ่งขึ้น และลดระยะเวลาที่ใช้ในการพัฒนาชิ้นงานลงได้เป็นอย่างมาก จึงทำให้สามารถทำการผลิตแบบจำนวนมาก (Mass production) ได้
แม่พิมพ์โปร่งใส (Photo: Nissan)
นิสสันรายงานว่ากระบวนการผลิต CFRP แบบจำนวนมากที่พัฒนาขึ้นนี้ สามารถลด Lead Time ในการผลิตลงได้เกือบครึ่ง และลด Cycle Time ในการขึ้นรูปได้ราว 80% เมื่อเทียบกับวิธีการทั่วไป โดยตั้งเป้านำกระบวนการนี้มาใช้ในการผลิตชิ้นส่วนสำหรับยานยนต์รุ่นทั่วไปที่เป็นการผลิตแบบจำนวนมาก ซึ่งจะช่วยให้ CFRP กลายเป็นวัสดุที่ผู้บริโภคเข้าถึงได้มากขึ้น
ที่แล้วมา ด้วยวัสดุ CFRP เป็นมีข้อดีหลายประการ แต่เนื่องจากมีราคาแพงและขึ้นรูปได้ยาก ทำให้การนำมาใช้กับยานยนต์ตามท้องตลาดเป็นเรื่องยาก ความสำเร็จในการพัฒนากระบวนการผลิตของนิสสันครั้งนี้จะนำมาซึ่งการพัฒนาชิ้นส่วนยานยนต์ให้มีน้ำหนักเบา แต่ทนทาน ช่วยในการประหยัดเชื้อเพลิง และเพิ่มความปลอดภัยให้กับผู้โดยสารมากยิ่งขึ้น นอกจากนี้ หากนำวัสดุ CFRP ที่มีน้ำหนักเบามาใช้ในการผลิตชิ้นส่วนตัวถังช่วงบน จะทำให้จุดศูนย์ถ่วงของยานยนต์ต่ำลง ทำให้ยานยนต์มีความคล่องตัวมากขึ้นอีกด้วย
อ่านต่อ
- CFRP และแกนมอเตอร์ คือ 2 โอกาสทางธุรกิจในยุคใหม่ของอุตสาหกรรมยานยนต์
- เมื่อ ”พลาสติก” แข็งแรงเทียบเท่า High Tensile Steel
- เทคโนโลยีใหม่ Thermoplastic CFRP Rapid Heater