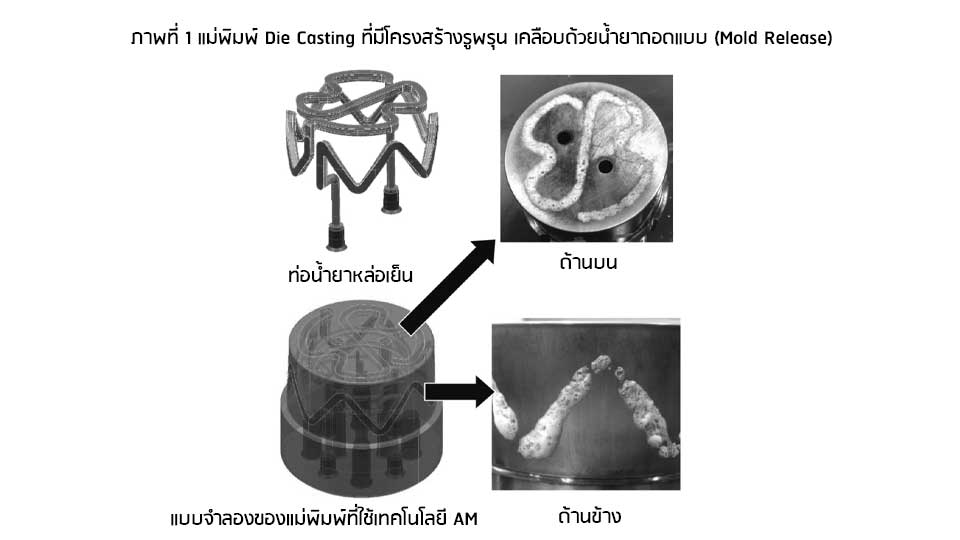
Additive Manufacturing ปัจจุบัน ตอบโจทย์ "การออกแบบแม่พิมพ์" แค่ไหน
ความก้าวหน้าของเทคโนโลยี Additive Manufacturing (AM) ไม่จำกัดเพียงแค่การผลิตชิ้นงานจากพลาสติกเรซิ่น แต่รวมไปถึงชิ้นงานโลหะ รวมถึงการผลิตแม่พิมพ์ ซึ่ง Metal 3D Printer สามารถพิมพ์ชิ้นงานที่มีความซับซ้อนออกมาได้ดี และเริ่มถูกนำมาใช้ในหลายอุตสาหกรรม
เทคโนโลยี Additive Manufacturing (AM) คือ เทคโนโลยีการผลิตแบบเพิ่มเนื้อวัสดุลงไปเป็นชั้น ๆ เพื่อขึ้นรูปชิ้นงาน โดยไม่ต้องอาศัยแม่พิมพ์ จึงเป็นที่รู้จักกันในชื่อว่า เทคโนโลยีการพิมพ์ แบบ 3 มิติ (3D Printing) หากเปรียบเทียบกับกระบวนการผลิตแบบดั้งเดิมแล้ว AM มีความใกล้เคียงกับงานเชื่อม แต่ตรงข้ามกับการตัดเฉือนโลหะซึ่งมีการสูญเสียเนื้อวัสดุที่ไม่ต้องการทิ้งไป
อย่างไรก็ตาม แม้จะมีความพยายามนำมาใช้ แต่หากมองในภาพรวมจะพบว่าเทคโนโลยีนี้ยังห่างไกลความแพร่หลาย และแม่พิมพ์จะยังคงเป็นเครื่องมือที่ถูกใช้ในการผลิตชิ้นงานโลหะอยู่ แม้จะมีคำกล่าวว่าแม่พิมพ์กำลังมาถึงทางตัน แต่ในความเป็นจริงแม่พิมพ์ยังพัฒนาต่อได้อีกมาก ไม่ว่าจะเป็นความคืบหน้าของเทคโนโลยี CAD ที่ช่วยให้สามารถออกแบบแม่พิมพ์ที่มีประสิทธิภาพสูงขึ้น การทำแบบจำลองเพื่อค้นหารูปแบบของแม่พิมพ์ที่เหมาะกับชิ้นงานที่สุด แม่พิมพ์ที่ช่วยให้การผลิตชิ้นงานเร็วขึ้น และอื่น ๆ
Advertisement | |
![]() |
ผู้บุกเบิกแม่พิมพ์จาก Additive Manufacturing
และในไม่กี่ปีมานี้เอง ที่การพิมพ์ด้วยผงโลหะ (Metal 3D Printing) มีความก้าวหน้ามากขึ้น และถูกนำไปใช้ในหลายอุตสาหกรรม เช่น อวกาศ, เครื่องมือแพทย์, และอื่น ๆ ซึ่งคาดว่าในปี 2030 ทั้งอุตสาหกรรมอวกาศและอุตสาหกรรมเครื่องมือแพทย์ จะเป็นกลุ่มแรก ๆ ที่นำ Metal 3D Printer มาใช้ในการผลิตแม่พิมพ์ เนื่องจากเป็นอุตสาหกรรมที่ต้องการชิ้นงานที่มีความซับซ้อน และความคงทนสูง ซึ่งเป็นคุณสมบัติที่ต้องการจุดเด่นของแม่พิมพ์โลหะร่วมกับเครื่องพิมพ์ 3 มิติ
- จาก 0 ถึง 1200 ก้าวสำคัญในประวัติศาสตร์การพิมพ์ 3 มิติกับ Porsche 911 GT2 RS ผสานโซลูชันจาก ZEISS
- ศูนย์วิจัย 3D Printing ของ Lamborghini ผลิตเครื่องจำลองการหายใจช่วยคัดกรองผู้ป่วยโควิด-19
- Oxford Performance Materials เทคโนโลยี 3D Printing สำหรับพิมพ์กะโหลกเทียม
อย่างไรก็ตาม ปฏิเสธไม่ได้ว่าการนำเทคโนโลยี Additive Manufacturing มาใช้ในการผลิตแม่พิมพ์ไม่ใช่เรื่องง่าย เนื่องจากมีตัวแปรมากมายที่ต้องคำนึงถึง ด้วยเหตุนี้เอง ในภาคอุตสาหกรรมจึงจำเป็นต้องศึกษาว่าการใช้แม่พิมพ์จาก 3D Printing นั้นมีคุณภาพตรงตามความต้องการหรือไม่ หรือมีกระบวนการผลิตใดที่เหมาะสมมากกว่า
ลดเวลาผลิตแม่พิมพ์ เมื่อใช้ AM ร่วมกับเทคโนโลยีตัดเฉือนโลหะ
เทคโนโลยี Additive Manufacturing ที่ได้รับความสนใจจากอุตสาหกรรมโลหะการ คือ Powder Bed Fusion (PBF) ซึ่งใช้ความร้อนในการหลอมผงโลหะโดยยิงพลังงานความร้อนลงบนชิ้นงาน และ Directed Energy Deposition (DED) ซึ่งใช้การพ่นผงโลหะเข้าไปในลำแสงเลเซอร์กำลังสูง ทั้งสองเทคโนโลยีนี้ได้รับความสนใจจากผู้ผลิตเครื่องจักรกลนำมาผนวกเข้ากับเครื่อง Multi-tasking Machine
จากการศึกษาพบว่า Multi-tasking Machine ที่ใช้เทคโนโลยี Additive Manufacturing แบบ Powder Bed Fusion (PBF) สามารถนำมาใช้ในการผลิตแม่พิมพ์ได้ ซึ่งในการทดลองพบว่า การผลิตแม่พิมพ์วิธีนี้ทำให้สามารถใช้ทูลส์ที่มีความยาวน้อยลง ไม่จำเป็นต้องแยกส่วนแม่พิมพ์มากนัก และทำแนวเสริมความแข็งแรงของชิ้นงาน (Rib) ที่มีความลึกได้ ทำให้ใช้เวลาในการผลิตแม่พิมพ์น้อยลง นำไปสู่การลดต้นทุน ซึ่งจากการทดลองโดย สถาบันเทคโนโลยีการผลิตขั้นสูง มหาวิทยาลัยคานะซะวะ ประเทศญี่ปุ่น พบว่ากระบวนการนี้สามารถลดเวลาที่ใช้ผลิตแม่พิมพ์ได้ถึง 60%
Additive Manufacturing กับการออกแบบแม่พิมพ์
ในความเป็นจริงแล้ว จุดเด่นของ Additive Manufacturing สามารถนำมาประยุกต์ใช้เพื่อให้แม่พิมพ์ในปัจจุบันมีประสิทธิภาพสูงขึ้นได้ ยกตัวอย่างเช่น การออกแบบท่อหล่อเย็นของแม่พิมพ์ที่มีประสิทธิภาพ แต่ไม่สามารถผลิตได้จริงเนื่องจากความซับซ้อน ซึ่งเครื่องพิมพ์ 3 มิติสามารถนำมาช่วยในส่วนนี้
ดังนั้น การออกแบบแม่พิมพ์ในอนาคตจะมีอิสระมากขึ้นก็ไม่ใช่เรื่องที่เกินจริง ซึ่งจากกรณีตัวอย่างข้างต้นนี้ ทำให้มีหลายบริษัทอยู่ระหว่างการทดลองออกแบบแม่พิมพ์ที่มีการปรับเปลี่ยนวิธีจัดวางท่อน้ำใหม่เพื่อให้สามารถควบคุมอุณหภูมิแม่พิมพ์ได้ดียิ่งขึ้น
นอกจากนี้ หากใช้วิธีการขึ้นรูปผงโลหะแบบ PBF ซึ่งมีจุดเด่นคือสามารถควบคุมโครงสร้างของรูพรุนได้ ก็จะช่วยให้แม่พิมพ์ระบายก๊าซออกมาได้ดียิ่งขึ้น นำไปสู่การลดฟองอากาศ อีกทั้งโครงสร้างที่มีรูพรุนยังสามารถขึ้นรูปได้เร็วกว่าโครงสร้างทั่วไป ซึ่งหากนำมาใช้ในการผลิตแม่พิมพ์ เช่น เปลี่ยนโครงสร้างภายในแม่พิมพ์บางส่วนให้มีรูพรุน ก็จะสามารถผลิตแม่พิมพ์ออกมาได้เร็วยิ่งขึ้น
ปัจจุบัน ทางทีมวิจัยจากมหาวิทยาลัยคะนะซะว่า และผู้ผลิตแม่พิมพ์รายต่าง ๆ ได้อยู่ระหว่างพิจารณาทดลองผลิตแม่พิมพ์ Die Casting ที่มีโครงสร้างรูพรุนประสิทธิภาพสูง (ภาพที่ 1)
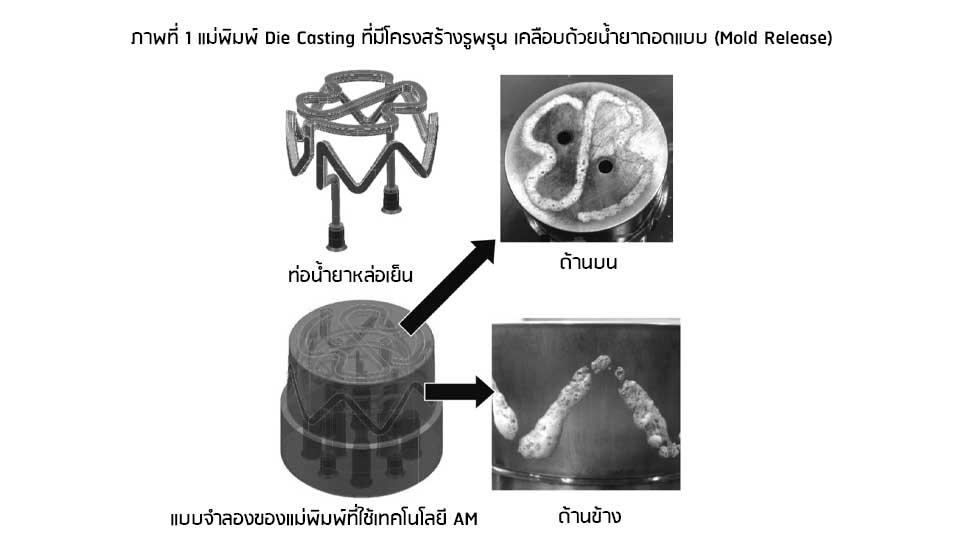
ภาพที่ 1 แม่พิมพ์ Die Casting ที่มีโครงสร้างรูพรุน เคลือบด้วยน้ำยาถอดแบบ (Mold Release)
จะเห็นได้ว่า เทคโนโลยี Additive Manufacturing เข้ามาเปลี่ยนวิธีการออกแบบแม่พิมพ์ขึ้นรูปโลหะให้ก้าวหน้ายิ่งขึ้น อย่างไรก็ตาม อุปสรรคสำคัญก็คือความแม่นยำ เนื่องจาก “แม่พิมพ์ขึ้นรูปโลหะ” เป็นอุปกรณ์ที่ต้องการความแม่นยำสูงมาก แต่โครงสร้างที่มีความซับซ้อนจากเครื่องพิมพ์ 3 มิติขัดแต่งได้ยาก หรือกระทั่งไม่อาจขัดแต่งได้ด้วยเครื่องจักรและกระบวนการทั่วไป ด้วยเหตุนี้ จึงมีการทดลองปรับปรุงพื้นผิวด้านในของแม่พิมพ์ โดยการฉีดผงขัด (Abrasive Grain) เข้าไปในทางไหลของแม่พิมพ์โดยตรง (ภาพที่ 2)
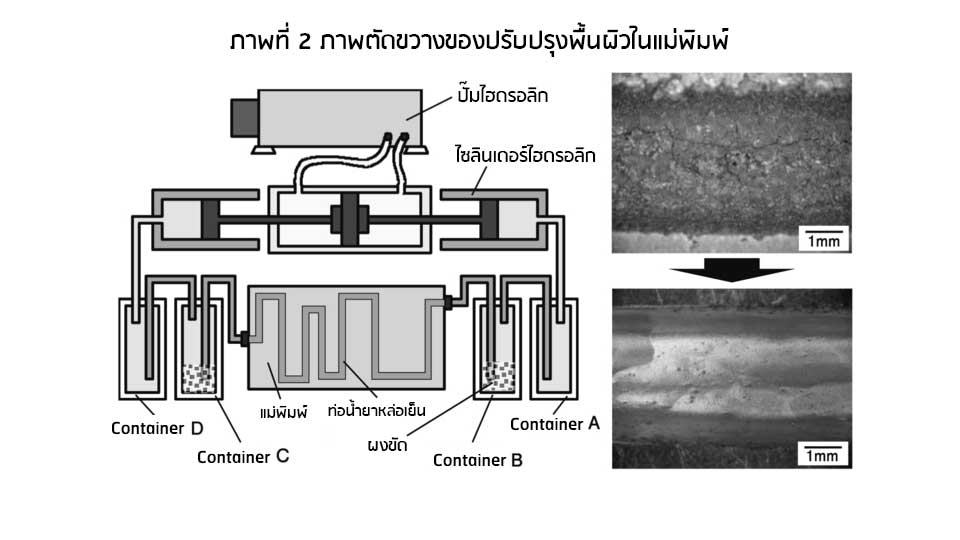
ภาพที่ 2 ภาพตัดขวางของปรับปรุงพื้นผิวในแม่พิมพ์
โดยในการทดลองนี้ได้ใช้ปั๊มไฮดรอลิกแรงดันสูงฉีดผงขัดเข้าไปในแม่พิมพ์ ซึ่งช่วยให้การปรับปรุงพื้นผิวด้านในแม่พิมพ์ทำได้จริง อย่างไรก็ตาม พบว่าสามารถควบคุมคุณภาพผิวแม่พิมพ์ได้ยาก ซึ่งหากเป็นในส่วนท่อหล่อเย็นคงไม่ใช่ปัญหาใหญ่นัก แต่หากเป็นส่วนที่ต้องการความแม่นยำแล้วยังคงต้องศึกษาหาวิธีปรับปรุงพื้นผิวที่ดีกว่านี้
นอกจากความแม่นยำของการผลิตแม่พิมพ์แล้ว ปัญหาด้านโครงสร้างเองก็เช่นเดียวกัน เนื่องจากโครงสร้างของชิ้นงานจาก 3D Printer จะถูกเรียงกันเป็นชั้น ๆ ซึ่งอาจทำให้เกิดปัญหาจากภาระความเค้นในแม่พิมพ์ ซึ่งหากยังแก้ปัญหาเหล่านี้ไม่ได้ การผลิตแม่พิมพ์ด้วยวิธีการ 3D Printing ให้ตอบรับยุคที่ชิ้นงานต้องการความแม่นยำสูงขึ้นเรื่อย ๆ ก็จะยังคงเป็นเรื่องที่ห่างไกล นอกจากนี้ ไม่ใช่ว่าปัญหาทุกอย่างของแม่พิมพ์ขึ้นรูปโลหะในปัจจุบันจะสามารถแก้ไขได้ด้วยวิธีอื่น ๆ อีกด้วย
สรุปบทความ
Additive Manufacturing สามารถช่วยให้แม่พิมพ์มีประสิทธิภาพสูงกว่าที่ผ่านมาได้จริง และจะเห็นได้ว่าเครื่องพิมพ์ 3 มิติในปัจจุบันมีความแม่นยำสูงขึ้นอย่างต่อเนื่อง ทำให้หลายฝ่ายเชื่อมั่นว่าในอนาคตเทคโนโลยีนี้จะเข้ามามีบทบาทในการผลิตแม่พิมพ์อย่างแน่นอน
#Additive Manufacturing #AM #เทคโนโลยี Additive Manufacturing คือ #เทคโนโลยี3มิติ คืออะไร #เทคโนโลยีการพิมพ์ แบบ 3มิติ คืออะไร #3D Printer #3D Printing #3D Printing Technology #Metal 3D Printer #แม่พิมพ์ขึ้นรูปโลหะ #การออกแบบแม่พิมพ์ขึ้นรูปโลหะ #แม่พิมพ์ Die #เครื่องพิมพ์ 3 มิติ #M Report #mreportth #วงในอุตสาหกรรม #ข่าวอุตสาหกรรม
บทความยอดนิยม 10 อันดับ
- นิยามใหม่ SME ปี 63 ใช้ “รายได้” เป็นตัวกำหนด
- กลยุทธ์การ PR และ Communication ในยุคดิจิทัล
- เทคโนโลยีแห่ง G สู่ 5G เครือข่ายไร้สาย
- เทคโนโลยีสำหรับโลจิสติกส์ ทางเลือกสู่ทางรอด ปรับก่อนโดนเบียด
- 8 แนวโน้มการดำเนินธุรกิจในอนาคต (8 Industry’s Mega Trend)
- 10 รับเหมาฝ่าวิกฤตโกยรายได้ปี”62 ITD ยืนหนึ่ง “ซิโน-ไทยฯ” แซงหน้า “ช.การช่าง”
- บอร์กวอร์เนอร์ (BorgWarner) ฉลองเปิดโรงงานแห่งใหม่ที่นิคมฯ อีสเทิร์นซีบอร์ด (ระยอง)
- เซ็นแล้ว! 'อู่ตะเภา-เมืองการบินภาคตะวันออก' เฟสแรกเสร็จปี 67
- ยอดขายรถยนต์เมษายน 2564
- แบตเตอรี่ลิเธียมไอออนคืออะไร ตลาดจะก้าวไปในทางไหนในปี 2030?
อัปเดตข่าวทุกวันที่นี่ www.mreport.co.th
Line / Facebook / Twitter / YouTube @MreportTH