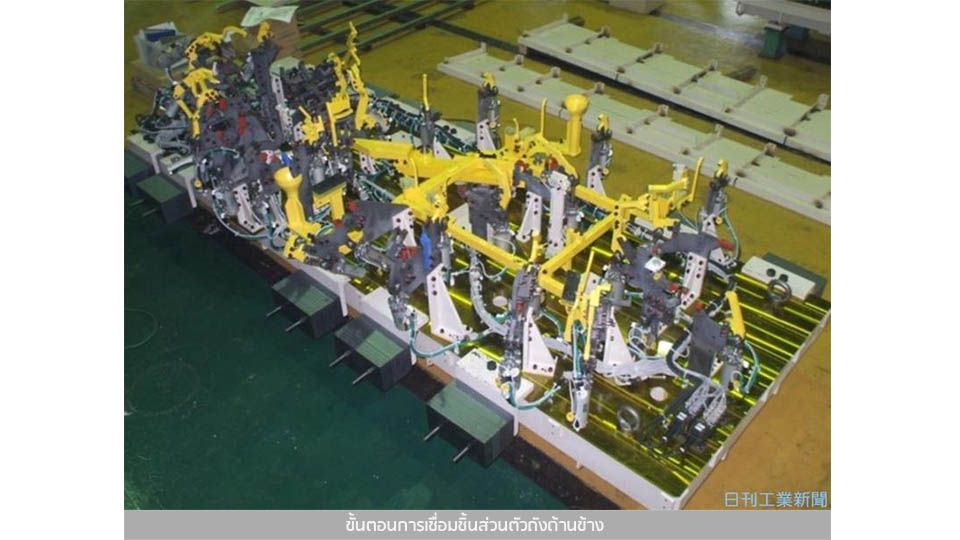
Modular Design ลด Process งานเชื่อมตัวถังยานยนต์
Imanishi Manufacturing ทดลองใช้ “การออกแบบโมดูล (Modular design)” ในงานเชื่อมโลหะ และเริ่มจากการใช้กับชิ้นส่วนยานยนต์ขนาดใหญ่ โดยอาศัยข้อมูลชิ้นส่วนยานยนต์ที่รวบรวมมาในการออกแบบอุปกรณ์ที่เป็นมาตรฐานซึ่งเมื่อเทียบกับการออกแบบใหม่ที่เป็นวิธีที่ใช้โดยทั่วไปแล้วพบว่าสามารถลด Process ลงได้เป็นอย่างมาก และสามารถลดต้นทุนได้มากถึง 60%
ในส่วนของการออกแบบโมดูลนั้น Imanishi Manufacturing ได้ใช้ข้อมูล CAD จากการออกแบบชิ้นส่วนเป็นข้อมูลตั้งต้นก่อนที่จะแบ่งข้อมูลนี้ออกเป็นประเภทต่าง ๆ เช่น ชิ้นส่วนนี้ ต้องใช้ Jig แบบใด รูปทรงและขนาดของชิ้นส่วนแบบไหนที่สามารถออกแบบ Jig เพื่อให้ใช้ร่วมกันได้ และอื่น ๆ เพื่อพัฒนาอุปกรณ์จับยึด หรือ Jig ที่สามารถสับเปลี่ยนได้ตามการใช้งาน และสามารถใช้งานซ้ำได้
ที่ผ่านมา ในการเชื่อมชิ้นส่วนตัวถังด้านข้างของยานยนต์นั้น ทางบริษัทจำเป็นต้องใช้ Welding Jig มากถึง 500 ตัว และในยานยนต์บางโมเดลจำเป็นต้องใช้มากถึง 800 ตัว ซึ่งเมื่อนำการออกแบบโมดูลมาใช้แล้ว จะได้เป็นชิ้นส่วนพื้นฐาน ที่สามารถใช้แทน Welding Jig และอุปกรณ์นิวเมติกส์ได้มากถึง 49%
รูปแบบการผลิตเช่นนี้ จะถูกใช้ในการผลิต “ยานยนต์โมเดลใหม่” ของ Mazda ซึ่งจะออกสู่ตลาดในช่วงต้นปี 2019 นอกจากนี้ Imanishi Manufacturing ยังได้ตั้งเป้าพัฒนาการออกแบบโมดูลต่อ เพื่อให้มีจำนวนชิ้นส่วนพื้นฐานขึ้นไปอยู่ที่ 60%
เดิมที การเชื่อมชิ้นส่วนยานยนต์นั้น ต้องออกแบบ Jigs ใหม่ทุกครั้งให้รองรับกับลักษณะของชิ้นส่วนนั้น ๆ อย่างไรก็ตามยานยนต์รุ่นที่ใช้ชิ้นส่วนร่วมกัน มีชิ้นส่วนที่ใช้ลักษณะบางส่วนร่วมกัน หรือที่เรียกว่า “Common Design” นั้น ได้มีจำนวนมากขึ้นในช่วงระยะหลังมานี้ ซึ่งเป็นสาเหตุหลักที่ทำให้การออกแบบโมดูลสามารถเข้ามาในงานเชื่อมโลหะได้
นอกจากนี้ การออกแบบโมดูล ยังช่วยลดปริมาณการประมวลผลในส่วนของข้อมูล CAM ได้อีกด้วย ซึ่งช่วยให้การทำงานใช้เวลาลดน้อยลง เชื่อมโยงไปสู่ประโยชน์อื่น ๆ ที่ผู้ผลิตจะได้รับ เช่น การผลิตชิ้นส่วนแบบมาตรฐาน ในช่วงที่มียอดออเดอร์เข้ามาต่ำ หรือมีกำลังผลิตที่ว่างอยู่อีกด้วย