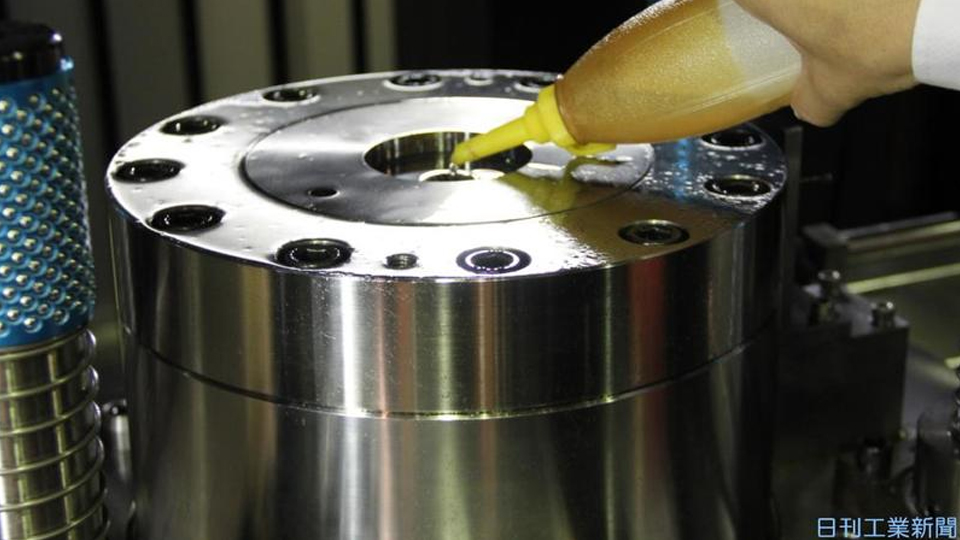
เทคโนโลยีทางรอด อุตสาหกรรมขึ้นรูปโลหะ และโลหะแผ่น
ปัจจุบันอุตสาหกรรมขึ้นรูปโลหะ และอุตสาหกรรมโลหะแผ่น เผชิญอยู่กับสถานการณ์คลื่นแห่งการเปลี่ยนแปลงครั้งใหญ่ ทั้งปัญหาขาดแคลนแรงงาน และสังคมผู้สูงอายุ ซึ่งส่งผลกระทบโดยตรงต่อทุกอุตสาหกรรมการผลิต นำมาซึ่งปัญหาแรงงานมีทักษะไม่เพียงพอ หรือไม่สามารถทำงานได้อย่างมีประสิทธิภาพ ส่งผลให้กำลังการผลิต และความแม่นยำของผลิตภัณฑ์ รวมถึงความปลอดภัยในการผลิตลดลง อีกทั้งสงครามการค้าที่นำมาซึ่งการชะลอตัวในอุตสาหกรรม จึงเป็นเหตุผลว่า ในช่วงเวลาเช่นนี้เอง ที่ผู้ผลิตและผู้ใช้ควรศึกษาเทคโนโลนีให้ถี่ถ้วน เพื่อที่จะแข่งขันในตลาดได้ต่อไป
หรือเครื่องเพรสจะมาแรง
กระบวนการผลิตของ Amada Orii ที่ใช้น้ำมันแทนแม่พิมพ์
หาก Machine Tools มีจุดเด่นในด้านความเที่ยงตรงของเครื่องมือ เครื่องเพรสก็มีจุดเด่นที่กำลังผลิตสูง ซึ่งในช่วงไม่กี่ปีที่ผ่านมา เครื่องเพรสที่ใช้เซอร์โวมอเตอร์ หรือที่เรียกว่า Servo Press ก็กลายเป็นเทคโนโลยีที่ทำให้ประสิทธิภาพด้านนี้สูงขึ้น ซึ่งหากใช้ร่วมกับแม่พิมพ์ที่มีความแม่นยำ ในอนาคตเครื่องเพรสก็อาจจะแทนที่ Machine Tools ในการผลิตชิ้นงานหลายชนิดก็เป็นได้
AMADA ORII ประสบความสำเร็จในการลดเวลาผลิต และต้นทุนในการผลิตเฟืองเกลียวของ SUBARU ได้ 75% และ 30% ตามลำดับ ด้วยกระบวนการที่เรียกว่า “Fluid Pulse Forging” ซึ่งบรรจุวัตถุดิบลงในแม่พิมพ์ทรงกระบอก เติมน้ำมันลงไป ซึ่งน้ำมันจะทำหน้าที่แทนแม่พิมพ์
AIDA ENGINEERING เป็นอีกรายที่พัฒนาเครื่องเพรสให้มีความแม่นยำมากขึ้น โดยล่าสุด พัฒนาให้เครื่องเพรสมีความแม่นยำในระดับ 10 ไมโครเมตร ทำให้ชิ้นงานที่ได้สามารถนำไปใช้งานได้เลย โดยไม่ต้องผ่าน machine Tools อีกรอบหนึ่ง ซึ่งเป็นผลจากการร่วมพัฒนาระหว่างผู้ผลิต และลูกค้าผู้ใช้งานจริง จนสามารถช่วยลดเศษโลหะที่เกิดจากการผลิตได้เป็นอย่างมาก
ความคืบหน้าของระบบอัตโนมัติในอุตสาหกรรมโลหะแผ่น
โดยทั่วไปแล้ว ในอุตสาหกรรมโลหะแผ่น พนักงานจำเป็นต้องเข้ามาทำงานร่วมกับเครื่องจักร โดยเฉพาะอย่างยิ่งในขั้นตอนการดัด พับ และตกแต่งผิวงาน ส่งผลให้ผู้ผลิตหลายรายเล็งพัฒนาระบบอัตโนมัติที่สามารถทดแทนกระบวนการเหล่านี้ได้
เมื่อปี 2018 Mitsubishi Electric ได้ซื้อกิจการผู้ผลิตระบบอัตโนมัติค่ายสวิตเซอร์แลนด์เข้ามาเป็นส่วนหนึ่งของบริษัท และวางจำหน่ายผลิตภัณฑ์ของบริษัทนี้ภายใต้แบรนด์ของตน โดยสามารถทำงานกับโลหะแผ่นที่มีความหนาสูงถึง 25 มม. และมีน้ำหนักมากถึง 2 ตันได้ และใช้แม่เหล็กในการติดตั้งเครื่องมือให้เหมาะสมกับขนาดของแผ่นโลหะ
ส่วนทาง Amada Holdings ได้เลือกแก้ไขปัญหานี้ ด้วยการพัฒนาระบบอัตโนมัติเพื่อใช้ในขั้นตอนการดัด และพับแผ่นโลหะ ด้วยการใช้หุ่นยนต์แบบ 7 แกน แทนที่ระบบเปลี่ยนแม่พิมพ์ เพื่อลดขั้นตอนให้น้อยลง และใช้พนักงานในส่วนของงานขนาดเล็กที่ต้องการความแม่นยำสูงแทน โดยออกแบบระบบให้มีความสูงต่ำ เพื่อให้พนักงานสามารถนั่งทำงานได้โดยสะดวก
ซึ่งการออกแบบระบบการผลิตให้นั่งทำงานได้นั้น เดิมทีมีผู้ผลิตรายใหญ่ค่ายยุโรปเป็นผู้ริเริ่ม และมีผู้ผลิตรายอื่นที่ผลิตออกจำหน่ายไปก่อนหน้านี้ไม่นานนักอย่าง Murata Machinery ซึ่งตัวเครื่องมีความกว้างลดลงจากทั่วไปถึง 35% ทำให้พนักงานสามารถนั่งทำงานด้วยได้อย่างสะดวกสบาย
เทคโนโลยีควบคุม สิ่งสำคัญของไฟเบอร์เลเซอร์
Yamazaki Mazak พัฒนาเครื่องไฟเบอร์เลเซอร์สำหรับงานผลิตท่อขนาดเล็กขึ้นมาโดยเฉพาะ ซึ่งตัวเครื่องจะทำหน้าที่ลำเลียงวัสดุสำหรับผลิตท่อเข้าไปในเครื่องทีละชิ้น จึงสามารถเปลี่ยนขั้นตอนงานที่ใช้เวลานาน ให้กลายเป็นระบบอัตโนมัติได้สำเร็จ
โดยไฟเบอร์เลเซอร์ เป็นที่ยอมรับในอุตสาหกรรมการผลิต เนื่องจากความประหยัดพลังงานของเทคโนโลยีนี้ และเป็นเทคโนโลยีที่สำคัญต่ออุตสาหกรรมโลหการเป็นอย่างมาก และเหมาะสำหรับงานตัดโลหะแผ่นแบบบางเป็นอย่างยิ่ง ซึ่งเมื่อไม่กี่ปีก่อน ไฟเบอร์เลเซอร์ทั่วไปมีพลังงานอยู่ที่ไม่กี่กิโลวัตต์ ในขณะที่ปัจจุบัน ผู้ผลิตหลายรายตั้งเป้าพัฒนาให้มีพลังงานมากกว่า 10 กิโลวัตต์ขึ้นไป ส่วนในประเทศจีน ล่าสุดได้ประสบความสำเร็จในการผลิตไฟเบอร์เลเซอร์ 25 กิโลวัตต์เป็นที่เรียบร้อยแล้ว
อย่างไรก็ตาม ในภาคอุตสาหกรรมนั้น ผู้ผลิตมีความเห็นต่อไฟเบอร์เลเซอร์กระจายออกเป็นหลายฝ่าย เช่น Mitsubishi Electric ที่มีความเห็นว่า “ควรผลิตเครื่องให้มีกำลังเพิ่มขึ้นหรือไม่ก็ขึ้นกับกระแสตลาด” ในขณะที่ Yamazaki Mazak มีความเห็นว่า “เทคโนโลยีนี้น่าจะสิ้นสุดที่ 10 กิโลวัตต์เท่านั้น”
Amada Holding แสดงความเห็นว่า “สิ่งสำคัญในการพัฒนาไฟเบอร์เลเซอร์ ไม่ใช่ Oscillator ที่หลายบริษัทต่างผลิตได้ แต่ควรมุ่งไปที่เทคโนโลยีควบคุมเลเซอร์มากกว่า” ซึ่ง Yamazaki Mazak มีความเห็นใกล้เคียงกันว่า “สิ่งที่ควรพัฒนาคือการควบคุมรูปทรงของเลเซอร์ ซึ่งจะนำไปสู่การผลิตชิ้นงานที่มีคุณภาพสูงขึ้นได้”