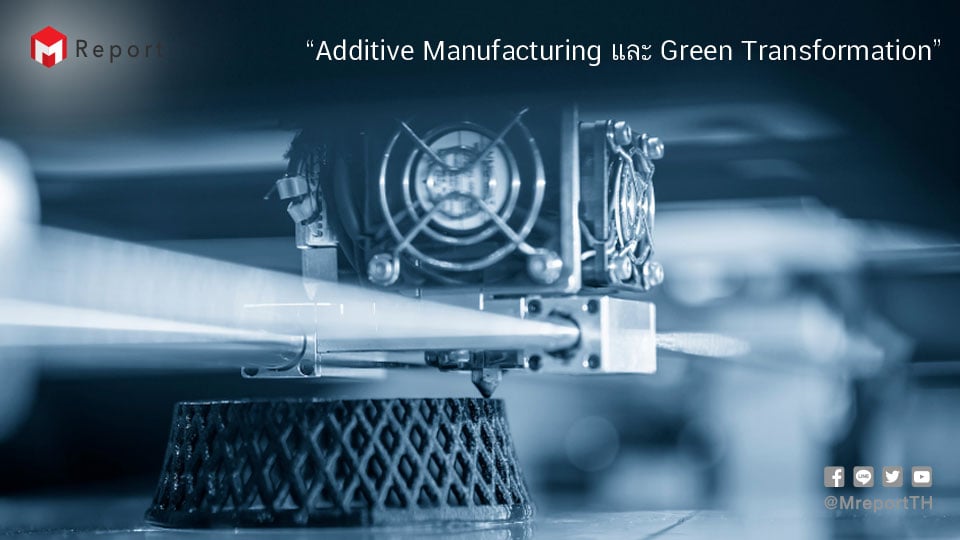
‘Additive Manufacturing’ ตัวเร่งการเปลี่ยนผ่านสู่ ‘อุตสาหกรรมสีเขียว’ จริงหรือ?
เทคโนโลยี Additive Manufacturing กำลังจะมีบทบาทมากขึ้นในยุคเปลี่ยนผ่านสู่อุตสาหกรรมสีเขียว จริงหรือ? ในเมื่อกระบวนการผลิตผงโลหะและการพิมพ์ชิ้นงาน 3D ยังต้องใช้พลังงานสูง
เว็บไซต์ EMO Hannover หนึ่งในงานจัดแสดงเครื่องจักรกลและเทคโนโลยีโลหะการที่ใหญ่ที่สุดของโลก เผยแพร่บทความในหัวข้อ “Additive Manufacturing เร่งเครื่องอุตสาหกรรมสู่ Green Transformation” มีใจความสำคัญ ดังนี้
- 3D Printing: เทคโนโลยีการพิมพ์ 3 มิติ สำหรับอุตสาหกรรมเครื่องจักรกล
- Machine Tools ญี่ปุ่น จับเทรนด์ Green Transformation อย่างไร
Advertisement | |
เมื่อปี 2020 อียู (EU) ได้เปิดตัวแผนปฏิบัติการด้านเศรษฐกิจหมุนเวียน (Action Reduction Plan for the Circular Economy) ริเริ่มนโยบายที่มีเป้าหมายเพิ่มระดับความยั่งยืนในภาคอุตสาหกรรม ใช้เทคโนโลยีใหม่ ๆ เพื่อลดผลกระทบต่อสิ่งแวดล้อม ประหยัดพลังงานและทรัพยากรธรรมชาติ เพื่อให้ได้ผลิตภัณฑ์ที่ยั่งยืนยิ่งขึ้น
การผลิตชิ้นงานแบบเพิ่มเนื้อวัสดุ หรือ Additive Manufacturing (AM) หนึ่งในเทคโนโลยีหลักที่ถูกพิจารณา ด้วยคุณสมบัติของเทคโนโลยีการพิมพ์ 3 มิติช่วยให้ผู้ใช้สามารถออกแบบผลิตภัณฑ์และบริการรูปแบบใหม่ ๆ อีกทั้งยังให้ผลดีในด้านความคุ้มค่าและประหยัดทรัพยากร
- Additive Manufacturing ปัจจุบัน ตอบโจทย์ "การออกแบบแม่พิมพ์" แค่ไหน
- 4 ทศวรรษ ‘ไทยสากล กรุ๊ป’ ก้าวสู่ Manufacturing Transformation
แม้เทคโนโลยี Additive Manufacturing จะต้องใช้พลังงานสูงในกระบวนการผลิตวัสดุผงพิมพ์ และการพิมพ์ชิ้นงาน แต่สามารถชดเชยได้ด้วยผลิตภัณฑ์ขั้นสุดท้ายที่ประหยัดยิ่งขึ้น ซึ่งเป็นการช่วยลดคาร์บอนฟุตพริ้นท์ ทำให้การพิมพ์ 3 มิติเชิงอุตสาหกรรมมีข้อดีในแง่ของความยั่งยืน
สมาคมเครื่องจักรกลแห่งยุโรป หรือ CECIMO จึงได้รวบรวมกรณีศึกษาจากผู้ผลิตทั่วยุโรป เพื่อย้ำถึงศักยภาพของการผลิตด้วยเทคโนโลยีดังกล่าว ซึ่งนาย Stewart Lane ประธานคณะกรรมการเทคโนโลยี AM จากสมาคมฯ กล่าวแสดงความเห็นว่า Additive Manufacturing สามารถช่วยให้การเปลี่ยนผ่านสู่ยุคสีเขียวในภาคอุตสาหกรรมรวดเร็วยิ่งขึ้น ซึ่งสมาคมและอียูจะร่วมสนับสนุนการประยุกต์ใช้เทคโนโลยีนี้ให้มีบทบาทในแผนนโยบายกรีนดีล (European Green Deal) ต่อไป
โลหะจากเศษวัสดุ และของเสียจากการผลิตแบบ Additive Manufacturing
ตัวอย่างแรก คือ กรณีศึกษาจาก F3nice บริษัทสัญชาตินอร์เวย์ ผู้ผลิตผงโลหะสำหรับ AM ด้วยวัสดุรีไซเคิล 100% โดยรวบรวมขยะโลหะ เช่น เศษโลหะจากอุตสาหกรรมน้ำมันและก๊าซ ไปจนถึงผงโลหะใช้แล้วและชิ้นงานที่เสียหรือไม่ได้มาตรฐานมาแปรรูปเป็นผงโลหะใหม่ ซึ่งได้ผ่านการทดสอบโดยผู้เชี่ยวชาญอิสระเพื่อให้มั่นใจในคุณภาพของผลิตภัณฑ์ขั้นสุดท้าย
ลดของเสีย 95%
ถัดมา คือ 3D4MEC จากอิตาลี ซึ่งอยู่ระหว่างการพัฒนาระบบข้อต่อที่มีจำนวนชิ้นส่วนน้อยและพิมพ์ด้วย 3D Printer จากการทดลองพบว่า การพิมพ์ 44 ชั่วโมงจะได้ชิ้นงานที่มีปริมาตรรวม 180 ลูกบาศก์เซนติเมตร (1.8 กิโลกรัม) โดยมีของเสียจากการพิมพ์ราว 110 กรัม คิดเป็นสัดส่วนไม่ถึง 8% ของปริมาตรวัสดุทั้งหมดที่ใช้ในการพิมพ์ ซึ่งในทางกลับกัน หากผลิตชิ้นงานนี้ด้วยกระบวนการกัดชิ้นงานจะมีของเสียมากถึงประมาณ 35 กิโลกรัม ดังนั้น Additive Manufacturing สามารถลดของเสียจากการผลิตชิ้นงานได้ถึง 95% และยังสามารถผลิตชิ้นงานที่มีรูปทรงซับซ้อนได้อีกด้วย
ใช้วัตถุดิบน้อยลง 30 เท่า
ตัวอย่างสุดท้าย คือ ทีมจากสหราชอาณาจักร ซึ่งประกอบด้วย Thales Alenia Space, WAAM3D, Glenalmond Technologies และ Cranfield University ประสบความสำเร็จในการผลิตต้นแบบภาชนะรับความดัน (Pressure Vessel) จากไทเทเนียมสำหรับการสำรวจอวกาศ โดยมีความสูง 1 เมตร หนัก 8.5 กิโลกรัม ผลิตจากไททาเนียมอัลลอยด์ Ti-6AI-4V ผ่านกระบวนการ Wire Arc Additive Manufacturing (WAAM) ซึ่งมีจุดเด่นด้านความเร็ว ทำให้ผลิตชิ้นงานได้เร็วขึ้น ใช้วัสดุน้อยลง 30 เท่าเมื่อเทียบกับกระบวนการผลิตทั่วไป ซึ่งในกรณีนี้ หมายถึงการประหยัดไททาเนียมอัลลอยด์ Ti-6AI-4V มากกว่า 200 กิโลกรัม
#AdditiveManufacturing #greentransformation #3Dprinting #Mreport #mreportth #ข่าวอุตสาหกรรม
บทความยอดนิยม 10 อันดับ
- สรุปยอดขายรถยนต์ในไทย ปี 2565
- ครม. อนุมัติงบอุดหนุนรถ BEV 18,000 - 150,000 บาท/คัน
- ภาพรวมอุตสาหกรรมโซลาร์เซลล์ของไทย
- 17 อุตสาหกรรมแนวโน้มเติบโตในปี 2566
- 10 ตัวอย่างที่นำ 5G มาใช้งานได้อย่างน่าสนใจและประสบผลสำเร็จ
- เทคโนโลยีแห่ง G สู่ 5G เครือข่ายไร้สาย
- แบตเตอรี่ลิเธียมไอออนคืออะไร ตลาดจะก้าวไปในทางไหนในปี 2030?
- เทคโนโลยีสำหรับโลจิสติกส์ ทางเลือกสู่ทางรอด ปรับก่อนโดนเบียด
- นิยามใหม่ SME ใช้ “รายได้” เป็นตัวกำหนด
- FTA ไทย มีกี่ประเทศ พอหรือไม่ ทำไมต้องคิดเรื่อง CPTPP
อัปเดตข่าวทุกวันที่นี่ www.mreport.co.th
Line / Facebook / Twitter / YouTube @MreportTH