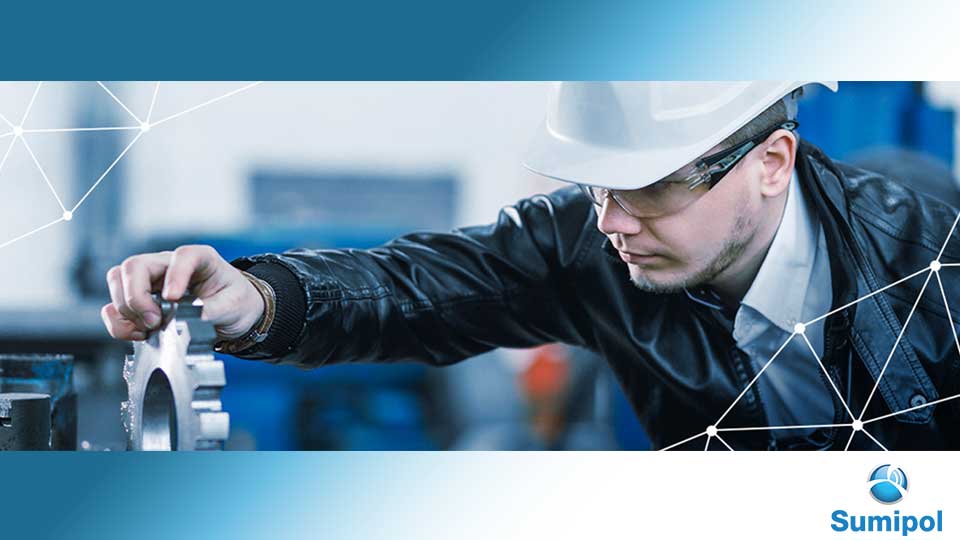
ลดของเสียให้เป็นศูนย์ แนวคิด Zero Defect ในระบบควบคุมคุณภาพ เกิดขึ้นจริงได้อย่างไร
สุมิพล คอร์ปอเรชั่น (Sumipol Corporation) รุกคืบ ชูแนวคิด Zero Defect ลดของเสียให้เป็นศูนย์ ดันโรงงานให้มีระบบการผลิตที่ดี พร้อมกับการควบคุมคุณภาพได้ในตัวเองตลอดกระบวนการ
Zero Defect หรือ แนวคิดการลดของเสียให้เป็นศูนย์ นั้นไม่ใช่เรื่องใหม่ แต่เราอาจต้องยอมรับว่าด้วยเทคโนโลยีและความเข้าใจในการจัดการสมัยก่อนนั้นไม่อาจส่งผลให้แนวคิดนี้เติบโตได้เต็มที่ แต่ด้วยการเข้ามาของระบบ Automation และนวัตกรรมอื่น ๆ ที่ช่วยควบคุมคุณภาพสินค้าและการทำงานในโรงงาน ทำให้ทุกอย่างเปลี่ยนไปโดยสิ้นเชิง
บทความนี้จะพาคุณเข้าไปทำความรู้จักกับแนวคิด Zero Defect ให้ลึกขึ้น และขยายความว่าทำไมการควบคุมคุณภาพและ Zero Defect จึงเป็นเรื่องสำคัญที่ขาดไม่ได้ในโรงงานปัจจุบัน
ทำความรู้จักกับแนวคิด Zero Defect
Zero Defect หรือการจัดการการผลิตโดยลดของเสียให้เป็นศูนย์ มีแนวคิดตั้งอยู่ในพื้นฐานที่ว่า ‘ทุกภาคส่วนทำงานถูกต้อง เกิดความผิดพลาดน้อยที่สุดจนจบกระบวนการ นั่นคือการจัดการที่สมบูรณ์’ และการจัดการที่สมบูรณ์นั้นจะช่วยให้ค่าใช้จ่ายโดยรวมลดลง หากแนวคิดนี้เป็นจริงจะส่งผลให้โรงงานของเราสามารถพัฒนาคุณภาพได้โดยเสียเงินน้อยที่สุด หรือไม่เสียเลย
Zero Defect กับระบบควบคุมคุณภาพ
แนวคิด Zero Defect ถูกขยายความให้ชัดเจนขึ้นอย่างมากด้วยฝีมือของ Philip B. Crosby นักธุรกิจชาวอเมริกันที่มีผลงานด้านงานเขียนมากมาย โดยหนึ่งในการอธิบายของเขาได้ระบุเกี่ยวกับการจัดการคุณภาพ (Quality Management) เชื่อมกับเรื่อง Zero Defect ไว้อย่างน่าสนใจ
สิ่งนั้นถูกเรียกว่า หลักการจัดการคุณภาพอย่างสมบูรณ์ 5 ประการ (5 absolutes of quality management) โดยมีรายละเอียดดังนี้
- คุณภาพหมายถึงการทำมาตรฐาน ไม่ใช่ทำเรื่องสง่างาม
- ไม่มีปัญหาใดสำคัญเทียบเท่าปัญหาด้านคุณภาพ
- เราสามารถลดต้นทุนได้หากทำทุกสิ่งให้ถูกต้องเสียแต่แรก
- ต้นทุนของคุณภาพเป็นตัวชี้วัดประสิทธิภาพ
- มาตรฐานของคุณภาพคือของเสียที่เป็นศูนย์ (Zero Defect)
แม้ว่ารายละเอียดจะมี 5 ข้อ แต่ชัดเจนมากกว่าในข้อ 5 ซึ่งเปรียบเสมือนปลายทางของการจัดการและควบคุมคุณภาพ ไม่ว่าจะโรงงานใดๆ ก็ตาม
ซึ่งการทำงานทั้งหมดจะเกิดขึ้นได้ก็เกิดจากการวางแผนการที่ดี วางระบบที่ถูกต้อง รวมไปถึงมีระบบควบคุมคุณภาพของแผนการและการผลิตต่างๆ เพื่อตรวจสอบและป้องกันไม่ให้เกิดข้อผิดพลาดขึ้น ดังคำกล่าวที่ระบุข้างต้นว่า “คุณภาพคือการทำมาตรฐาน”
ลดของเสียให้เป็นศูนย์ในการทำงานจริงด้วย QUALITY CONTROL
ระบบควบคุมคุณภาพ (Quality Control) มีบทบาทสำคัญอย่างมากในการทำของเสียให้เป็นศูนย์ หากเรามองจากกราฟหรือรูปแล้ว เรามักเห็นการตรวจสอบคุณภาพนั้นอยู่ท้ายสุดเสมอ แต่รู้หรือไม่ว่าจริงๆ แล้ว การ QC ที่ดีต้องมีการตรวจสอบควบคุมทั้งระบบ
โดยเฉพาะในการทำออโตเมชั่นในโรงงานปัจจุบัน ที่เราสามารถรับรู้ข้อมูลของเครื่องจักรทุกตัวได้ด้วยปลายนิ้วสัมผัส สามารถควบคุมคุณภาพของทุกอย่างได้ในทันที สอดคล้องกับแนวคิดของ Zero Defect ที่ส่งเสริมให้การทำงานมีการควบคุมคุณภาพตั้งแต่ต้นทาง เริ่มจัดซื้อวัตถุดิบ จัดจ้างคน ไปจนถึงปลายทาง ที่ส่งถึงมือลูกค้า
ทุกอย่างล้วนมีปัจจัยของ Quality Control แฝงอยู่แทบทั้งสิ้น
แล้วเราจะทำอย่างนั้นได้อย่างไร ? ในเมื่อการจัดการโรงงานปัจจุบัน หลาย ๆ โรงงานยังมีการยก QC ให้เป็นส่วนท้ายสุดเสมอ โดยไม่ได้ใส่ใจเรื่องนี้แต่แรก
คำตอบคือการทำ Automation Design & System Integration หรือการดีไซน์ระบบอัตโนมัติและการวางระบบการผลิตแบบองค์รวม จำลองรูปแบบการทำงานของโรงงานของคุณใหม่ด้วยทรัพยากรที่มี เสริมด้วยการพัฒนาอุปกรณ์เท่าที่โรงงานต้องการ ซึ่งหากเป็นผู้วางระบบที่มีประสบการณ์รวมถึงมีอุปกรณ์ครบครัน จะสามารถช่วยให้โรงงานของคุณนั้นมีระบบการผลิตที่ดี พร้อมกับการควบคุมคุณภาพได้ในตัวเอง
เมื่อระบบทุกอย่างถูกวางไว้แบบพร้อมสรรพ มีการดำเนินการในระบบอย่างมีประสิทธิภาพ เรื่องของ Zero Defect หรือการทำงานในรูปแบบลดของเสียให้เป็นศูนย์ ก็จะกลายเป็นเรื่องปกติธรรมดา ไม่ใช่อุดมคติอีกต่อไป เพิ่มทั้งประสิทธิภาพ ความเร็ว ผลกำไร และยังลดค่าเสียโอกาสจากสิ่งที่ผลิตเกินหรือเสียได้อีกด้วย