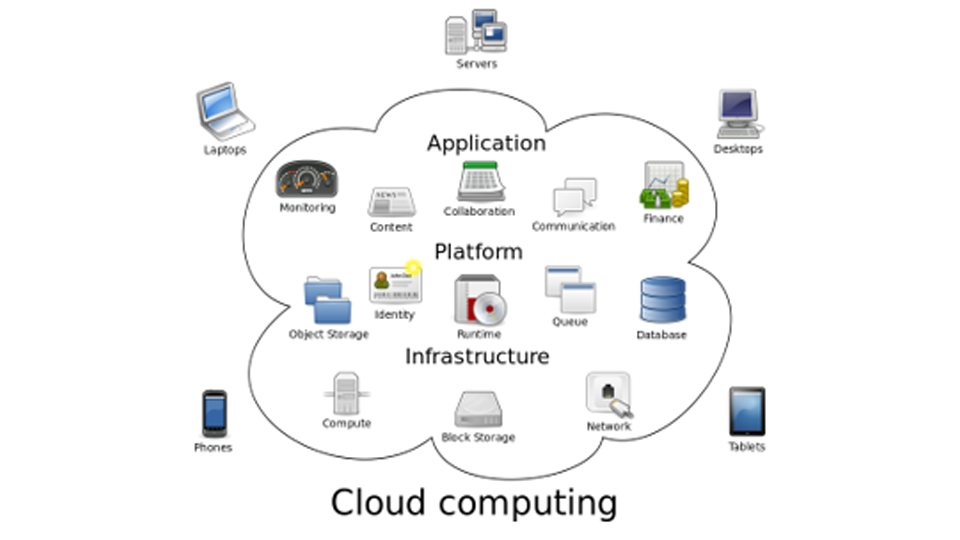
ระบบ Smart Maintenance ในยุค Industry 4.0
การเข้าสู่ยุคอุตสาหกรรม 4.0 (Industry 4.0) เป็นยุคโลกแห่งความเป็นจริง (Physical world) ถูกเชื่อมโยงเข้ากับโลกดิจิทัล (Cyber world) หรือที่เรียกว่า Cyber Physical Systems โดยเครื่องจักร อุปกรณ์ในระบบการผลิตและบริการโดยอาศัยอุปกรณ์ตรวจจับ (Sensor) และตัวควบคุม (Controller) ชนิดต่าง ๆ และยังมีการนำระบบสมองกลฝังตัว (Embedded system) มาใช้กับเครื่องจักร เครื่องมือ หรืออุปกรณ์ ทำให้มีความสามารถคำนวณ ประมวลผลข้อมูล และจำแนกและแก้ปัญหาได้ด้วยตัวเอง โดยอุปกรณ์เหล่านี้สามารถเชื่อมต่อถึงอุปกรณ์อื่นโดยตรง หรือเชื่อมต่อเข้ากับโครงข่ายสื่อสารต่าง ๆ ได้ทุกที่ ทุกเวลา ผ่านเครือข่ายออนไลน์และอินเทอร์เน็ตไร้สายและมีสาย โดยเราจะเริ่มได้ยินอุปกรณ์เหล่านี้กันมากขึ้นในชื่อ Internet of Things (IoT) นั่นเอง
เมื่อข้อมูลที่ติดต่อสื่อสารกันที่จากอุปกรณ์เหล่านี้มีปริมาณมาก รวมถึงความสามารถในการประมวลผลและจัดเก็บข้อมูลที่จำกัด และเมื่ออุปกรณ์เหล่านี้บางตัวอาศัยพลังงานจากแบตเตอรี่ จึงจำเป็นต้องลดการใช้พลังงานที่เกิดขึ้นจากประมวลผลที่ซับซ้อนเหล่านี้ลง ทำให้ต้องอาศัยระบบ Cloud computing เป็นตัวกลางในการประมวลผล วิเคราะห์ ตัดสินใจ จัดเก็บข้อมูล และส่งข้อมูลหรือสื่อสารกับกับอุปกรณ์ (IoT) ตัวอื่น ๆ ต่อไป โดยเฉพาะในระบบที่การสื่อสารข้อมูลมีอุปสรรค หลุดจากการเชื่อมต่อ หรืออัตราความเร็วในการส่งข้อมูลต่ำ ทำให้เกิดความล่าช้า (Latency) ในการส่งข้อมูลระหว่างอุปกรณ์ ระบบคอมพิวเตอร์แม่ข่าย (Server) ในระบบ Cloud computing จะมีบทบาทในการส่งต่อข้อมูลเหล่านี้ให้กับอุปกรณ์ที่ขาดการเชื่อมต่อนี้ในภายหลัง
ดังนั้นระบบอุตสาหกรรม 4.0 จึงเป็นยุคที่ประกอบด้วยส่วนสำคัญ สามส่วน คือ
1. Cyber Physical Systems ที่เชื่อมต่อผลลัพธ์จากกระบวนการทำงาน การผลิตสินค้าและการให้บริการ เข้ากับโลกดิจิทัลในลักษณะข้อมูลที่สามารถบันทึก ประมวลผลและแสดงผลในภายหลังได้ โดยผ่านอุปกรณ์ตรวจจับ (Sensor) และตัวควบคุม (Controller) ต่าง ๆ
2. ระบบสมองกลฝังตัว ที่มีความสามารถในการประมวล วิเคราะห์ ตัดสินใจ ที่สามารถเชื่อมต่อเข้ากับโครงข่ายสื่อสารต่าง ๆ ได้ทุกที่ ทุกเวลา รวมถึงสามารถสื่อสารกันระหว่างอุปกรณ์ได้โดยตรง
3. ระบบ Cloud computing ที่ใช้ในการประมวล วิเคราะห์ จัดเก็บ และพักข้อมูลที่เชื่อมต่อเข้ากับระบบสมองกลฝังตัวผ่านโครงข่ายสื่อสาร
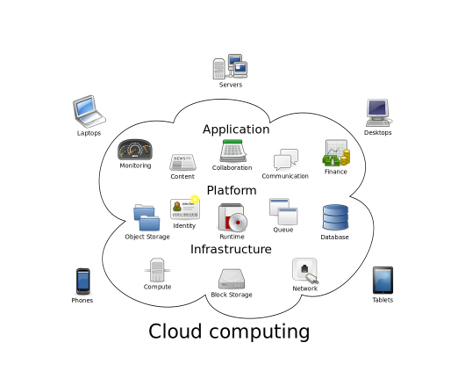
ภาพจาก Wikipedia ภายใต้ GNU Free Documentation License
ระบบ Smart Maintenance
เมื่อเครื่องจักรและอุปกรณ์ต่าง ๆ ในอุตสากรรมการผลิต มุ่งหน้าสู่อุตสากรรม 4.0 การบำรุงรักษาเครื่องจักรและอุปกรณ์ในกระบวนการผลิตในยุคนี้จึงต้องมีการปรับตัวตาม เพื่อให้สอดคล้องกับระบบการผลิต ซึ่งเป็นที่มาของคำว่า Smart Maintenance
ในระบบการบำรุงรักษาแบบดั้งเดิม ที่ข้อมูลจากสภาพการทำงานของเครื่องจักร ถูกนำมาใช้ในการวางแผนการซ่อม การบำรุงรักษา การผลิต และระยะเวลาในการเข้าตรวจสอบ หรือที่รู้จักกันในชื่อ Predictive Maintenance (PdM) หรือ Condition Based Maintenance (CbM)
ข้อมูลที่ได้มาจากการตรวจวัด แรงดันไฟฟ้า กระแสไฟฟ้า การสั่นสะเทือน ความร้อน เสียง ความดัน (Pressure) อัตราการไหล (Flow rate) อัตราการรั่วไหล (Leakage) และความชื้น เป็นต้น จะถูกตรวจสอบในแบบต่อเนื่อง (Online or Continuous Monitoring) โดยระบบหรือเครื่องมือตรวจสอบที่ติดตั้งถาวรที่มักมีราคาแพง และแบบตามช่วงเวลาที่กำหนด (Periodic or Routine Monitoring) โดยอาศัยคนในการเข้าไปตรวจสอบโดยใช้เครื่องมือแบบพกพา หรืออ่านค่าและจดบันทึกจากมิเตอร์ หรือเกจวัด เพื่อนำมาวิเคราะห์ ประสิทธิภาพ (Efficiency) สมรรถนะ (Performance) และการเสื่อมสภาพ (Condition) ของเครื่องจักร เพื่อการวางแผนปละจัดการในการผลิตและบำรุงรักษา
ระบบการตรวจสอบหรือเฝ้าระวัง (Condition Monitoring or Surveillance system) ที่กล่าวมาที่เป็นระบบปิด รวมถึงการเข้ากันได้ของฐานข้อมูลจากผู้ผลิตเครื่องมือตรวจสอบแต่ละราย ความแตกต่างของข้อกำหนดในการสื่อสาร (Protocol) รูปแบบข้อมูล ทำให้การบูรณาการ (Integration) ในการนำข้อมูลเหล่านี้มาวิเคราะห์และวางแผนงานร่วมกันในปัจจุบัน มีความยุ่งยากและขาดความคล่องตัว การมาของระบบอุตสาหกรรม 4.0 ซึ่งเป็นระบบเปิด ที่อาศัยอุปกรณ์ตรวจจับ (Sensor) ตัวควบคุม (Controller) อุปกรณ์ IoT ระบบคอมพิวเตอร์แม่ข่าย (Server) และ Cloud computing ช่วยให้การบูรณาการข้อมูลหรือสัญญาณต่าง ๆ จากการตรวจสอบ จากระบบควบคุม เป็นไปได้อย่างง่ายดาย
โดยข้อมูลจากอุปกรณ์ตรวจจับ (Sensor) และอุปกรณ์ IoT ราคาถูก สามารถส่งต่อไปยังระบบสื่อสารได้ทุกที่ ทุกเวลา ทำให้สามารถติดตาม วิเคราะห์ข้อมูล แจ้งเตือน วางแผน เข้าถึงรายงาน และการสั่งการได้สะดวกและรวดเร็วผ่านอุปกรณ์ต่าง ๆ เช่น สมาร์ทโฟน แท็บเล็ต และคอมพิวเตอร์โน๊ตบุค จากที่ใดก็ได้
บุคลากรในสถานประกอบการที่ต้องการนำระบบ Smart Maintenance มาใช้ จะต้องทำความเข้าใจในหลักการ และกระบวนการทำงาน และต้องศึกษาวิธีการในการนำเทคโนโลยี รวมถึงอุปกรณ์ IoT มาใช้กับระบบงานบำรุงรักษาที่เป็นอยู่ของตน รวมถึงสามารถพัฒนาระบบ Smart Maintenance ขึ้นเองในหน่วยงานของตนเอง เพื่อให้เหมาะกับสภาพการผลิตและการทำงานของเครื่องจักรที่แตกต่างกันในแต่ละสถานประกอบการ
ระบบ Smart Maintenance จึงประกอบไปด้วยส่วนสำคัญ คือ 1) อุปกรณ์ (Sensor อุปกรณ์ IoT และ Infrastructure ต่าง ๆ เช่นระบบโครงข่ายสื่อสาร และคอมพิวเตอร์แม่ข่าย) 2) แอพลิเคชั่น แพลตฟอร์ม หรือซอฟต์แวร์ในการรวบรวม จำแนกวิเคราะห์ และรายงาน 3) คนที่ทำหน้าที่วิเคราะห์ สรุปและวางแผน
นอกจากนี้ ผู้ที่วางระบบ และผู้ปฏิบัติงานในระบบ Smart Maintenance จะต้องเกี่ยวข้อง ศึกษาและทำความเข้าใจในเรื่องต่าง ๆ ดังต่อไปนี้
1. แนวคิด หลักปฏิบัติ รวมถึงกิจกรรมด้าน Condition Monitoring ของการบำรุงรักษาตามสภาพ (Predictive or Condition Based Maintenance)
2. การทำงานของอุปกรณ์ที่ใช้ในระบบ Smart Maintenance ได้แก่ การทำงานของอุปกรณ์ตรวจจับ (Sensor) อุปกรณ์ IoT ระบบการส่งข้อมูลระหว่างอุปกรณ์ หรือจากอุปกรณ์ไปยังคอมพิวเตอร์แม่ข่าย (Server)
3. การทำงานของซอฟต์แวร์ในระบบ Smart Maintenance ที่ใช้สำหรับ คำนวณ วิเคราะห์ จัดการ แสดงผล ควบคุม แจ้งเตือน และรายงาน
5. วิธีการตีความและแปรผลข้อมูลที่เก็บรวบรวมมาได้ เช่น กระแสและแรงดันไฟฟ้า การสั่นสะเทือน และความร้อน เป็นต้น
ในปัจจุบันที่มีความก้าวหน้าทางด้านปัญญาประดิษฐ์ (Artificial intelligence) ซึ่งมีส่วนช่วยในการจำแนกแยกแยะปัญหาการขัดข้อง (Failure) ในเครื่องจักรได้สะดวกและรวดเร็วขึ้น แต่ด้วยความซับซ้อนในการทำงานของเครื่องจักร ลักษณะการเสียหาย (Failure Mode) และการขัดข้อง คุณลักษณะทางการเคลื่อนที่ (Dynamic properties) ของระบบ ตัวแปรต่าง ๆ ในกระบวนการผลิต และลักษณะการทำงาน ทำให้ยังไม่มีระบบตรวจสอบอัตโนมัติใดที่สามารถตัดสิน บอกสภาพของเครื่องจักรได้อย่างแม่นยำและน่าเชื่อถือ
ทำให้ผู้ที่ทำหน้าที่วิเคราะห์และแปรผลข้อมูลนี้ จะต้องมีความรู้และความเข้าใจหลักการทำงาน ส่วนประกอบของเครื่องจักร สามารถเชื่อมโยง สมรรถนะ ประสิทธิภาพ และการเสื่อมสภาพจากการทำงานของเครื่องจักร กับพารามิเตอร์ต่าง ๆ ที่ตรวจวัดมา นำมาบูรณาการเพื่อวินิจฉัย ประเมิณความรุนแรง หรือการเสื่อมสภาพของเครื่องจักรได้อย่างแม่นยำและถูกต้องมากขึ้น
ดังนั้นระบบการบำรุงรักษา Smart Maintenance จึงเป็นระบบที่เกี่ยวข้องกับการตรวจสอบสภาพ สมรรถนะของเครื่องจักร โดยอาศัยเทคโนโลยีของอุปกรณ์ IoT การสื่อสาร สัญญาณและการวิเคราะห์ เพื่อนำมาวางแผนในการผลิตและบำรุงรักษา ซึ่งเป็นส่วนที่มาช่วยปรับปรุงระบบงาน Predictive Maintenance หรือ Condition Based Maintenance ให้มีประสิทธิภาพมากขึ้น โดยอาศัยอุปกรณ์ IoT ซอฟต์แวร์และระบบการสื่อสาร เข้ามาช่วย ด้วยค่าใช้จ่ายในกระบวนการตรวจสอบที่มีค่าใช้จ่ายถูกลง และการมาของยุค Industrial 4.0 ทำให้หลายฝ่ายเห็นข้อดีและโอกาสในการนำเทคโนโลยีมาใช้ในกระบวนการบำรุงรักษาได้ง่ายขึ้น และมีประสิทธิภาพสูงขึ้น แต่ด้วยเครื่องจักรที่นำระบบอัตโนมัติมาใช้กันมากขึ้น มีความสามารถมากขึ้น มีความซับซ้อน มีความเร็วในการผลิตที่สูงขึ้น รูปแบบการขัดข้องและเสื่อมสภาพจึงมีความซับซ้อนมากขึ้นตาม ทำให้ทักษะ ฝีมือในการแก้ไขหรือซ่อมบำรุง ประสบการณ์และความรู้ในการวิเคราะห์ปัญหา ยังเป็นสิ่งที่มีความสำคัญสูงสุดในงานบำรุงรักษาอยู่ต่อไป
แต่อย่างไรก็ตาม บุคลากรในสถานประกอบการไม่ว่าระดับใด ที่เกี่ยวข้องกับการใช้งาน การบำรุงรักษาเครื่องจักรในยุค Industry 4.0 นี้ ซึ่งเป็นแนวโน้มที่เกิดขึ้นทั่วโลก จำเป็นต้องเตรียมตัว หาความรู้ในเทคโนโลยีสมัยใหม่ด้านอื่น ๆ เพิ่มขึ้นอยู่เสมอ เพื่อให้สามารถรับมือกับการเปลี่ยนแปลงที่เกิดขึ้นอย่างรวดเร็วในยุด Industry 4.0 นี้