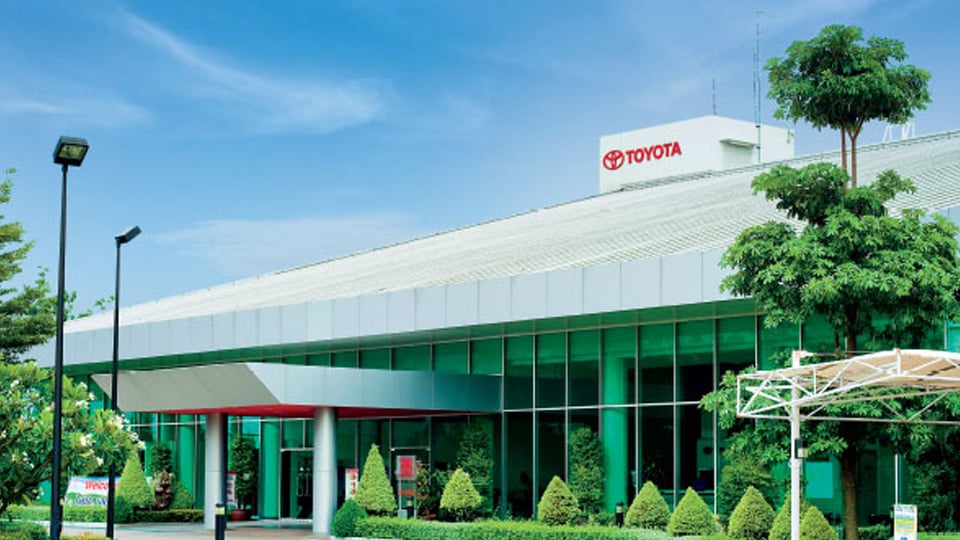
การเพิ่ม Productivity ในแบบฉบับของ ‘โตโยต้า โรงงานเกตเวย์’ (ตอน 2)
โตโยต้า มอเตอร์ ประเทศไทย (โรงงานเกตเวย์) หนึ่งในภาคเอกชนชั้นนำ ผู้ได้รับรางวัลคุณภาพแห่งชาติ ปี 2564 (Thailand Quality Award: TQA) เผยผลลัพธ์ความสำเร็จจากรางวัลอุตสาหกรรมดีเด่น ประเภทการเพิ่มผลผลิต ประจำปี 2564
ผ่านงานสัมมนา “Thailand Quality Award 2021 Winner Conference :The Excellence of the Future Readiness” จัดโดยสถาบันเพิ่มผลผลิตแห่งชาติ สถาบันเครือข่ายของกระทรวงอุตสาหกรรม ในหัวข้อบรรยาย Think Productivity Act Productivity : จัดกระบวนทัพ ยกระดับผลิตภาพองค์กรยั่งยืน
ในบทความก่อน M Report ได้พาผู้อ่านทุกท่านทำความรู้จัก โรงงานโตโยต้า เกตเวย์ ทั้ง 2 แห่ง เข้าใจนิยามและหลักในการวางแผนกลยุทธ์เพื่อเพิ่มผลิตภาพ (Productivity) ความสำคัญของหลักการผลิตแบบ Most Flexible รวมถึงได้เรียนรู้บทบาทของผู้บริหารระดับสูง การสื่อสารภายในองค์กร และปรัชญา Customer First ที่ทาง Toyota ยึดถือเป็นหลักปฏิบัติ ในการตอบสนองความพึงพอใจของลูกค้าไปบ้างพอสมควรแล้ว
- การเพิ่ม Productivity ในแบบฉบับของ ‘โตโยต้า โรงงานเกตเวย์’ (ตอน 1)
- โตโยต้า ผนึก สถาบันเพิ่มฯ เปิดหลักสูตรอบรม-ให้คำปรึกษา “การพัฒนาศักยภาพและยกระดับผลิตภาพผู้ประกอบการไทยสู่อุตสาหกรรม 4.0”
- ญี่ปุ่นค่ายแรก! 'โตโยต้า' ลงนาม 'กรมสรรพสามิต' ดันไทยสู่ยุคยานยนต์ไฟฟ้า
ในงานสัมมนานี้ เรายังได้ฝ่ายบริหารจากทางโตโยต้าอีกท่านหนึ่ง คือ คุณวัชระ ชื่นสมบูรณ์ ผู้ช่วยผู้จัดการฝ่ายบริหาร บริษัท โตโยต้า มอเตอร์ ประเทศไทย จำกัด (โรงงานเกตเวย์) มาช่วยให้ความรู้ในส่วนของการบริหารทรัพยากรบุคคล ต้นทุน และสายการผลิตในโรงงาน เพื่อความครอบคลุมทุกด้านมากขึ้น
คุณวัชระ เล่าว่า ในการดำเนินกิจกรรมต่าง ๆ ให้ประสบผลสำเร็จ การบริหารทรัพยากรบุคคลถือเป็นส่วนสำคัญอย่างมาก ซึ่งโตโยต้าใช้ Production EFFiciency (PEFF) เป็น KPI ในการชี้วัดประสิทธิภาพของคน โดยกำหนดเป็นเวลามาตรฐานในทุก ๆ กระบวนการผลิต มีทั้งการฝึกอบรมพนักงานผ่านศูนย์ฝึกอบรมของเราเอง (Toyota Way) หรืออาจมีการจัดบุคคลภายนอกเข้ามาช่วยฝึกอบรมในตำแหน่งของหัวหน้างานเพิ่มเติม นอกจากนี้ ยังมีการส่งพนักงานไปยังบริษัทแม่ โตโยต้า มอเตอร์ คอร์ปอเรชั่น ประเทศญี่ปุ่นอีกด้วย
“เมื่อเราได้พัฒนาบุคลากรให้พร้อมรองรับการเพิ่มผลผลิตให้มากขึ้น อย่างที่ทราบกันว่าเรามีระบบการผลิตแบบโตโยต้า Toyota Production System (TPS) เป็นหลักในด้านการจัดการกระบวนการอยู่แล้ว ซึ่งเรายังได้เพิ่ม Most Flexible Operation เพื่อการปรับเปลี่ยนตามสถานการณ์ต่าง ๆ ในภาวะที่อยู่ในช่วงของการแข่งขัน แม้สถานการณ์เปลี่ยนเราก็สามารถรับมือได้เร็ว คงความเสียหายไว้ให้น้อยที่สุด และยังทำกำไรได้ดี รวมถึงการออกแบบ Process การทำงาน, การฝึกอบรมพนักงานให้พร้อม, เครื่องจักรต่าง ๆ พยายามทำให้ง่ายขึ้น สามารถซ่อมบำรุงได้อย่างเหมาะสม”
Advertisement | |
![]() |
การออกแบบกระบวนการทำงานในสายการผลิตของโตโยต้า
โรงงาน โตโยต้า เกตเวย์ เป็นโรงงานเดียวที่ผลิตรถยนต์นั่งส่วนบุคคล (Passenger Car) ซึ่งการผลิตรถยนต์ในแต่ละรุ่นใช้เวลาไม่เท่ากัน นอกจากเวลามาตรฐานในการผลิตแล้ว (Standard Process) จึงได้กำหนดส่วนของเวลาที่อาจเพิ่มขึ้น (Option Process) และเตรียมจำนวนคนให้พร้อมรองรับกระบวนการดังกล่าว เพื่อปรับแผนการผลิตได้อย่างรวดเร็ว
โดยโตโยต้าได้กำหนดให้พนักงานสามารถทำงานได้หลากหลาย (Multi-Skill) อย่างน้อย 3 Process คือ Process ที่ทำอยู่เป็นประจำ, Process ที่อยู่ก่อนหน้า และ Process ที่เราจะต้องส่งงานให้ในส่วนถัดไป ทำให้สามารถลดการฝึกอบรม เมื่อมีการปรับกระบวนการทำงาน (เปลี่ยน Takt Time)
คุณวัชระ ชื่นสมบูรณ์ ผู้ช่วยผู้จัดการฝ่ายบริหาร โตโยต้า มอเตอร์ ประเทศไทย (โรงงานเกตเวย์)
ถัดมา คือ การกำหนดหรือออกแบบกระบวนการต่าง ๆ เราปลูกฝังให้พนักงานตระหนักและพยายามกำจัด 'ความสูญเปล่า' (MUDA) ผ่านการควบคุมการสูญเสีย 7 ประการ (7 Wastes) และใช้หลัก Just in Time (J.I.T.) และ จิโดกะ (Jidoka) ป้องกันความผิดพลาดในการทำงาน มีการปรับปรุงเครื่องจักรเพื่อรองรับ รวมถึงการใช้ Karakuri Dojo เพื่อปรับปรุงสายการผลิตโดยใช้แรงโน้มถ่วงให้เหมาะสมในแต่ละสถานการณ์ เช่น Karakuri Kaizen ระบบสายพานลำเลียงที่ใช้แรงเฉี่อยทำให้ให้เกิดพลังงานจลน์แทนการใช้พลังงานไฟฟ้า ซึ่งเป็นกลไกอย่างง่าย ๆ ที่ขับเคลื่อนได้โดยไม่ใช้พลังงานภายนอก ช่วยในการเพิ่มผลผลิต จัดส่งสินค้าได้รวดเร็วขึ้น ลดพลังงานไฟฟ้า-น้ำมันจากรถโฟล์คลิฟท์ที่ใช้ขนส่ง ทำให้การเกิดอุบัติเหตุในโรงงานลดลงตามด้วย
โดยได้ส่งเสริมให้พนักงานพยายามคิดและปรับปรุงกระบวนการนี้ให้ดียิ่งขึ้น ผ่านกิจกรรม เช่น 1 Day 1 Process (ระดับผู้จัดการ) ในส่วนของระดับพนักงานได้ผลักดันให้ให้เกิดความคิดในเรื่องของการลดเวลาในแต่ละกระบวนการ ในรูปแบบของการแข่งขันภายใน เป็นต้น
Karakuri Kaizen กระบวนการสนับสนุนสำคัญสำหรับระบบโลจิสติกส์ในโรงงาน
ทั้งนี้ ด้วยความที่โตโยต้ามีผลิตภัณฑ์ใหม่เกิดขึ้นอยู่เสมอ ดังนั้นจึงมีช่วงของการทดลองหรือดีไซน์ผลิตภัณฑ์ให้ได้อย่างรวดเร็ว จึงมีการนำเทคโนโลยี VR (Virtual Reality) เข้ามาช่วย เพื่อลด Lead time หรือ ระยะเวลาในการรอสินค้าของลูกค้าให้ลดลง เป็นผลให้มีการปรับ “การผลิตในแต่ละช่วงเวลา” (Takt Time) อยู่บ่อยครั้ง ทั้งในส่วนของงานที่ง่าย และงานที่ยาก โดยเฉพาะที่โรงงานเกตเวย์ เนื่องจากเป็นการผลิต Passenger Car ที่มีโมเดลค่อนข้างหลากหลาย
‘เทรนเท่าที่จำเป็น’ คือ การเพิ่มประสิทธิภาพในการเทรนนิ่งอีกทาง
ในแต่ละกระบวนการ เราใช้คนเฉพาะทักษะที่จำเป็น กับอีกส่วนที่เพิ่มขึ้นมา คือ Visual Manual ที่ใช้ Video ในการสอนงานในแต่ละขั้นตอน ซึ่งจะช่วยให้พนักงานได้เห็นสภาพการทำงานจริง โดยไม่จำเป็นต้องอยู่ในไลน์ผลิต ซึ่งมี Video ให้กับทุก Process การทำงาน
ซึ่งช่วยเราลด Lead Time ในการเทรนงานจาก 4 สัปดาห์ ลดลงอย่างน้อย 1 สัปดาห์ เพื่อรองรับการผลิตที่อาจเพิ่มขึ้น ณ เวลานั้น นอกจากนี้ เราใช้หลัก Machine & Facility - Quick Modify ช่วยลดเวลาในการติดตั้งเครื่องจักร ผ่านกิจกรรมที่พนักงานเป็นผู้คิดขึ้น
‘ตัวกันโง่’ หรือ ระบบป้องกันความผิดพลาด (Pokayoke) ของโตโยต้า
ในสายการผลิตของโตโยต้า เรามีระบบ ‘ตัวกันโง่’ (Pokayoke) ที่พนักงานเป็นผู้คิดค้นขึ้น เพื่อแสดงความผิดพลาดที่เกิดขึ้นจากการทำงานในกระบวนการต่อสายไฟ เมื่อมีการปรับเปลี่ยนกระบวนการ ก็จะต้องมีการขยับ เปลี่ยนแปลง เมื่อใช้ Pokayoke ทำให้เชื่อมต่อได้ง่ายขึ้น จากเดิมที่ใช้เวลาถึง 7 นาทีต่อหนึ่งจุด ลดเหลือเพียง 30 วินาที เมื่อรวมการลดระยะเวลาของพนักงานทุกส่วน ถือเป็นอีกส่วนสำคัญที่ช่วยเพิ่มประสิทธิภาพการผลิตให้ดีขึ้น
เรียกได้ว่าการผลิตของโตโยต้า มี Kaizen points เกิดขึ้นในทุกกระบวนการ รวมถึงมีการตรวจสอบและควบคุมคุณภาพการผลิต เมื่อเกิดปัญหาจะไม่ถูกปล่อยผ่านไปยัง Process ถัดไป ตั้งแต่เริ่มต้นจนถึงกระบวนการสุดท้าย (QC: Quality Control) ผ่าน KPI Control และยังมีหน่วยงานกลางควบคุมดูแลคุณภาพ (QA: Quality Assurance) ทำหน้าที่เสมือนลูกค้า โดยการ Sampling รถในแต่ละกลุ่ม เพื่อ Feedback ปัญหาที่เกิดขึ้นกลับไปยัง Process ต้นทาง
ซึ่งทั้งหมดทั้งมวลเรื่องของคุณภาพในการที่เราจะเป็น Best of The Best ในการเพิ่มผลผลิตให้ได้นั้น เครื่องมือและอุปกรณ์ต่าง ๆ ถือเป็นปัจจัยสำคัญ แต่ในอีกด้านหนึ่ง จะเห็นได้ว่าโตโยต้าพยายามผลักดันในเรื่องของจิตใจของพนักงานเป็นหลัก ทั้ง Kaizen Mind, Quality Mind และ Pokayoke Mind เพื่อสร้างทรัพยากรบุคคล ให้สามารถสนับสนุนการเพิ่มผลผลิตได้อย่างจริงจังและยั่งยืน
Competitiveness: การเพิ่มผลิตภาพและการปรับปรุงอย่างต่อเนื่อง ในช่วงแรกของการผลิตรถยนต์โมเดลใหม่ ตั้งแต่การเปิดตัว อาทิ CHR, Camry หรือ Corolla อาจเกิดปัญหาติดขัดในไลน์ผลิต เรามีการตั้ง Target เพื่อปรับปรุงงานในส่วนนี้ ผ่าน Challenge 1 Day Recovery แก้ไขปัญหาให้สำเร็จภายในวันถัดไป โดยให้ผู้บริหารระดับ GM ลงหน้างานเพื่อตัดสินใจปรับเปลี่ยนแก้ไขได้อย่างทันท่วงที
การใช้เทคโนโลยีในสายการผลิตของโตโยต้า
โตโยต้าใช้เทคโนโลยี Semi-Automate & IT, IoT รวมถึง Full Automate Big data เข้าช่วยในสายการผลิตรถยนต์ การควบคุมคุณภาพ และการดูแลสินค้า
เมื่อเราดำเนินกิจกรรมต่าง ๆ ที่ได้วางไว้อย่างครบถ้วนแล้ว จะถูกวัดผลโดยเน้นในเรื่องของลูกค้าเป็นหลัก ผ่านรางวัลต่าง ๆ โดยน้อมรับและนำมาปรับปรุงผลิตภัณฑ์ในส่วนที่ยังบกพร่อง รวมถึงในด้านของทรัพยากรบุคคลที่มีการวัดผลระบบความปลอดภัย ตัวเลขสะสมการไม่เกิดอุบัติเหตุ (นับเป็นชั่วโมง) และมีการสำรวจความผูกพันของพนักงาน (EE Score) อย่างต่อเนื่องในทุก ๆ ปี รวมถึงมีการส่งพนักงานบางส่วน เช่น Shop Floor, หรือ ระดับ Engineer และ Management ไปฝึกอบรมเพิ่มเติม ณ บริษัทแม่ ประเทศญี่ปุ่น เพื่อยกระดับการผลิตโรงงานในไทย โดยทั้งนี้ โตโยต้า มอเตอร์ ประเทศไทย ได้รับรางวัล สุดยอดนายจ้างดีเด่น จากเวที Thailand Best Empolyer Award จัดโดย บริษัท เอออน ฮิววิท ประเทศไทย (AON) และ สถาบันบัณฑิตบริหารธุรกิจศศินทร์แห่งจุฬาลงกรณ์มหาวิทยาลัย 3 ปีซ้อน (2016 - 2018)
สรุปหลักการเพิ่ม Productivity ในแบบฉบับของโตโยต้า ผ่าน 6 ด้านสำคัญ
การที่โตโยต้าได้นำอีกหลาย KPI มาชี้วัดในทุก ๆ ด้าน รวมถึงด้านสิ่งแวดล้อม หรือ การดูแลซัพพลายเออร์ ด้วยการจัดส่งผู้เชี่ยวชาญเข้าไปช่วยปรับปรุงเพิ่มผลผลิตและคุณภาพให้ดียิ่งขึ้น เป็นผลให้การประเมินคุณภาพทั้งตัวโรงงาน ประสิทธิภาพในการผลิตรถยนต์ เมื่อเปรียบเทียบในกลุ่มโตโยต้าประเทศอื่น ๆ ด้วยกันอย่าง มาเลเซีย อินโดนีเซีย หรือเวียดนามแล้ว พูดได้เต็มปากเลยว่า “โรงงานเกตเวย์” นับเป็นหนึ่งในโรงงานโตโยต้าที่เปี่ยมด้วยคุณภาพเบอร์ต้น ๆ ของโลก
- การเพิ่ม Productivity ในแบบฉบับของ ‘โตโยต้า โรงงานเกตเวย์’ (ตอน 1)
- ‘ชิ้นส่วนจากพืช’ ความท้าทายใหม่ของซัพพลายเออร์โตโยต้า
- ทุบทุกสถิติ TOYOTA ทำกำไรสูงสุดเป็นประวัติการณ์
#Toyota #โตโยต้าเกตเวย์ #รางวัลคุณภาพแห่งชาติ ปี 2564 #TQA2021 #Thailand #Quality #Award #Mreport #mreportth #ข่าวอุตสาหกรรม #onlinecontent
บทความยอดนิยม 10 อันดับ
- 10 ตัวอย่างที่นำ 5G มาใช้งานได้อย่างน่าสนใจและประสบผลสำเร็จ
- เทคโนโลยีแห่ง G สู่ 5G เครือข่ายไร้สาย
- แบตเตอรี่ลิเธียมไอออนคืออะไร ตลาดจะก้าวไปในทางไหนในปี 2030?
- เทคโนโลยีสำหรับโลจิสติกส์ ทางเลือกสู่ทางรอด ปรับก่อนโดนเบียด
- นิยามใหม่ SME ใช้ “รายได้” เป็นตัวกำหนด
- ธุรกิจที่ได้รับผลกระทบจาก COVID-19 ปี 2564
- กลยุทธ์การ PR และ Communication ในยุคดิจิทัล
- ปัญหาตู้คอนเทนเนอร์ขาดแคลน เจาะลึกตู้สินค้าหายไปไหน?
- เทรนด์การทำงานในอนาคต หลังไทยติดโควิด นานเกือบสองปี!
- FTA ไทย มีกี่ประเทศ พอหรือไม่ ทำไมต้องคิดเรื่อง CPTPP
อัปเดตข่าวทุกวันที่นี่ www.mreport.co.th
Line / Facebook / Twitter / YouTube @MreportTH