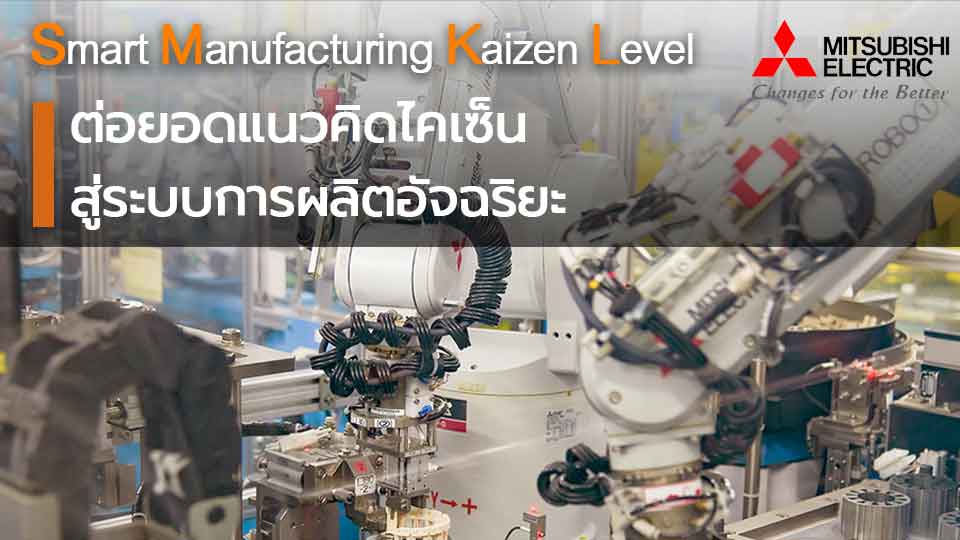
SMKL ต่อยอดแนวคิดไคเซ็น สู่ระบบการผลิตอัจฉริยะ
มิตซูบิชิ อีเล็คทริค แฟคทอรี่ ออโตเมชั่น เติมเต็มคอนเซปต์ e-F@ctory ด้วยการต่อยอดแนวคิดไคเซ็น (Kaizen) สู่ระบบการผลิตอัจฉริยะภายใต้ชื่อ SMKL ที่ทำได้จริง วัดผลความคุ้มค่าได้
เราต่างยอมรับข้อเท็จจริงที่ว่า การมองเห็นเท่ากับได้เปรียบ ทำให้ความสำเร็จของระบบการผลิตในยุคดิจิทัลเช่นนี้ไม่อาจละเลยการใช้เทคโนโลยี IoT เพื่อพัฒนาสู่ โรงงานอัจฉริยะ(Smart Factory) ซึ่งทางบริษัท มิตซูบิชิ อีเล็คทริค แฟคทอรี่ ออโตเมชั่น (ประเทศไทย) จำกัด ได้เติมเต็มคอนเซปต์ e-F@ctory โซลูชั่นสร้างโรงงานอัจฉริยะที่ได้ใช้กันอย่างแพร่หลายในอุตสาหกรรมการผลิต สู่ SMKL หรือ Smart Manufacturing Kaizen Level
SMKL คืออะไร?
SMKL คือ ดัชนีการประเมินระดับการใช้ข้อมูลในโรงงาน ที่สามารถช่วยผู้บริหารในการตัดสินใจลงทุน ด้วยการแสดงวัตถุประสงค์ ผลที่จะได้รับ และความสัมพันธ์ของแต่ละขั้นในการลงทุน เพื่อมุ่งสู่การเป็นโรงงานที่มีประสิทธิภาพยิ่งขึ้นกว่าเดิม
การใช้ SMKL ในระบบการผลิตจะนำไปสู่การเพิ่มผลผลิตและรายได้ด้วยการเน้นผลลัพธ์ ROI ที่ชัดเจนและยั่งยืน โดย SMKL ประเมินระดับการผลิตได้เป็นสองมิติ คือ Maturity Level และ Management level
Maturity Level
Maturity Level คือ การใช้งานข้อมูลระดับสภาวะการผลิต ระบบจะแสดงผลข้อมูลในสายการผลิตออกมาให้เห็นบนแกนแนวตั้ง 4 ระดับ ดังนี้
- Level A : Collect การเก็บบันทึกข้อมูล
- Level B : Visualize การแสดงผลข้อมูลออกมาเป็นรูปภาพ
- Level C : Analyze การวิเคราะห์ข้อมูล
- Level D : Optimize การนำข้อมูลมาใช้อย่างเหมาะสม
Management Level
Management Level คือระดับบริหารจัดการ ระบบจะแสดงผลข้อมูลเชิงลึกหรือรายละเอียดให้เห็นบนแกนแนวนอน 4 ระดับ ดังนี้
- Level 1 : Worker ผู้ปฏิบัติงาน
- Level 2 : Workplace สายการผลิต
- Level 3 : Factory โรงงาน
- Level 4 : Supply chain ซัพพลายเชนทั้งระบบ
ข้อดีของ SMKL
- ช่วยให้เริ่มต้นพัฒนากระบวนการผลิตได้อย่างเหมาะสม ตรงจุด และเป็นไปตามความต้องการ
- วิธีการแบบแยกส่วน ช่วยให้พัฒนากระบวนการผลิตได้ทีละขั้น
- สามารถคำนวณและวัด ROI ในแต่ละขั้นตอน เพื่อช่วยในการตัดสินใจลงทุน
- เพิ่มประสิทธิภาพการพัฒนากระบวนการผลิตให้สามารถเกิดขึ้นได้ในทุกระดับ ตั้งแต่ผู้ปฏิบัติงาน สายการผลิต โรงงาน ไปจนถึงซัพพลายเชนทั้งระบบ เพื่อนำไปสู่การพัฒนาอย่างมีนัยยะสำคัญ
กรณีศึกษา การใช้ SMKL พัฒนากระบวนการผลิต
กรณีที่ 1: การปรับปรุงประสิทธิภาพการผลิต
เพิ่มประสิทธิภาพการผลิต ลดความผันแปรของประสิทธิภาพของพนักงานผ่านการดำเนินการที่ “มองเห็น” ได้
สายการประกอบมีผลผลิตต่ำ ควบคุมค่าใช้จ่ายไม่ได้ เนื่องจากพนักงานแต่ละคนทำงานต่างกัน ส่งผลให้มีข้อผิดพลาดระหว่างการทำงานที่ต่างกันไปในแต่ละคน และไม่สามารถระบุได้ว่าพนักงานคนไหนทำงานผิดพลาด และผิดพลาดมากน้อยแค่ไหน จึงนำหลัก SMKL มาใช้ โดยการให้ให้พนักงานสวม Wearable Device ที่สามารถจับภาพระหว่างการทำงานในสายการประกอบเพื่อรวบรวมและวิเคราะห์ปัญหาระหว่างการทำงาน ซึ่งประสบความสำเร็จในการลดข้อผิดพลาดจาก Human Error และลดต้นทุนการผลิตลง ซึ่งส่วนต่างที่ได้จากการลดค่าใช้จ่ายทำให้บริษัทตัดสินใจนำรูปแบบการทำงานเช่นนี้ไปใช้กับทั้งโรงงานต่อไป
ผลลัพธ์
- ประสิทธิภาพการผลิตโดยรวมเพิ่มขึ้น 30%
- ลดเวลาที่ใช้ในการฝึกพนักงาน 65%
- สลับการผลิตระหว่างรุ่นได้เร็วขึ้น 18%
- เวลาในการประกอบชิ้นงานโดยเฉลี่ยลดลง 12%
กรณีที่ 2: ลดต้นทุน
ทำความเข้าใจการใช้พลังงาน และลดต้นทุนด้วยมาตรการประหยัดพลังงาน
โรงงานแห่งหนึ่งมีข้อกังวลด้านค่าใช้จ่ายในการดำเนินงานเนื่องจากมีการใช้พลังงนในการผลิตสูง อย่างไรก็ตามโรงงานแห่งนี้ไม่สามารถระบุได้ว่าการใช้พลังงานเกิดขึ้นในส่วนใดของโรงงานและสายการผลิต จึงทำการวัดพลังงานที่ใช้ในแต่ละจุดแล้วแสดงผลเป็นกราฟออกมาผ่านแดชบอร์ด จึงสามารถระบุได้ว่ามีการใช้พลังงานมากในจุดใด จากนั้นจึงทำการปรับปรุงจุดนี้ให้ใช้พลังงานน้อยลง จนท้ายสุดค่าใช้จ่ายที่ประหยัดได้ก็คุ้มค่าการลงทุน
ผลลัพธ์
- ประหยัดค่าไฟได้ 800,000 เยนต่อปี
- ใช้เงินลงทุน 2,000,000 เยน และคืนทุนได้ภายใน 30 เดือน
ปรึกษาเพื่อรับคำแนะนำการพัฒนากระบวนการผลิต ฟรี ได้ที่ บริษัท มิตซูบิชิ อีเล็คทริค แฟคทอรี่ ออโตเมชั่น (ประเทศไทย) จำกัด
Webinar: Factory transformation คลิก
Webinar: e-F@ctory Smart Solution for the next normal คลิก