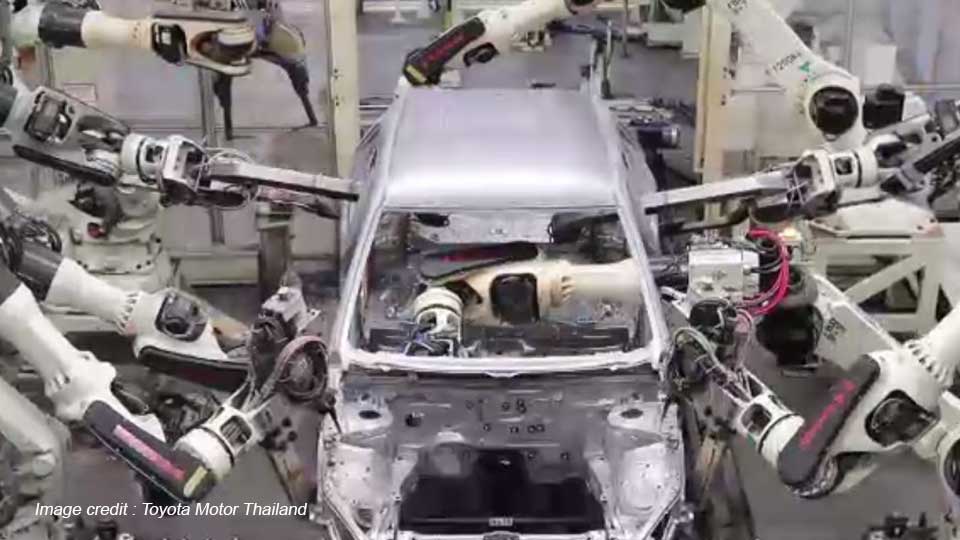
การเพิ่ม Productivity ในแบบฉบับของ ‘โตโยต้า โรงงานเกตเวย์’ (ตอน 1)
โตโยต้า มอเตอร์ ประเทศไทย (โรงงานเกตเวย์) หนึ่งในผู้ได้รับรางวัลคุณภาพแห่งชาติ ปี 2564 (Thailand Quality Award: TQA) เผยผลลัพธ์ความสำเร็จจากรางวัลอุตสาหกรรมดีเด่น ประเภทการเพิ่มผลผลิต ผ่านการบรรยายหัวข้อ “Think Productivity Act Productivity : จัดกระบวนทัพ ยกระดับผลิตภาพองค์กรยั่งยืน” ในงานสัมมนา “Thailand Quality Award 2021 Winner Conference :The Excellence of the Future Readiness” จัดโดยสถาบันเพิ่มผลผลิตแห่งชาติ สถาบันเครือข่ายของกระทรวงอุตสาหกรรม
คุณภัคพงษ์ ภักดีงาม รองผู้อำนวยการฝ่ายผลิต บริษัท โตโยต้า มอเตอร์ ประเทศไทย จำกัด (โรงงานเกตเวย์) เล่าให้เราฟังว่า Toyota Motor Thailand ในฐานะผู้ผลิตรถยนต์ที่มียอดขายและยอดการผลิตเป็นอันดับ 1 ของประเทศ ขับเคลื่อนโดย 3 โรงงานหลัก และ 1 ในนั้นคือโรงงานเกตเวย์
โรงงานเกตเวย์ ก่อตั้งขึ้นเมื่อปี พ.ศ. 2539 ที่นิคมอุตสาหกรรมเกตเวย์ จ.ฉะเชิงเทรา บนเนื้อที่กว่า 625 ไร่ ผลิตและประกอบรถยนต์ประเภทนั่งส่วนบุคคล ทั้งหมด 5 รุ่น คือ Camry, CHR, Corolla Altis, Vios และ Yaris บนพื้นฐานระบบการผลิตแบบโตโยต้า และพนักงานที่มีความชำนาญ มีความพิถีพิถันในทุกกระบวนการและปฏฺิบัติงานตรงตามมาตรฐานที่กำหนด เพียบพร้อมด้วยเทคโนโลยีที่ทันสมัย ใช้เวลาในการประกอบรถด้วยความเร็วในการผลิต (Takt Time (T/T)) เพียง 58 วินาที
โรงงานเกตเวย์ประกอบไปด้วย 4 กระบวนการหลักที่สำคัญ คือ 1. โรงปั๊มชิ้นส่วนตัวถัง 2. โรงเชื่อมชิ้นส่วนตัวถัง 3. โรงพ่นสี และ 4. โรงประกอบ
Advertisement | |
![]() |
นอกจากนี้ ยังมีอีก 2 กระบวนการย่อย นั่นคือ การเชื่อมประกอบช่วงล่าง การฉีดชิ้นส่วนพลาสติก ซึ่งทุกกระบวนการนั้นจะถูกตรวจสอบคุณภาพอย่างพิถีพิถัน โดยหน่วยงานตรวจสอบคุณภาพ หลังจากขั้นตอนการออกแบบ และกระบวนการเลือกสรรผู้ผลิตชิ้นส่วนที่ได้มาตรฐานระดับโลกแล้ว จึงเข้าสู่กระบวนการผลิตภายในโรงงาน โดยแบ่งได้ 6 แผนก ดังนี้
1. แผนกปั๊มชิ้นส่วนและตัวถัง (Press Shop) - ปั๊มขึ้นรูปโดยใช้เครื่องจักรที่ได้มาตรฐานและประหยัดพลังงาน รวมถึงเทคโนโลยีที่ช่วยลดมลภาวะทางเสียง
2. แผนกเชื่อมชิ้นส่วนและตัวถัง (Welding Shop) - หลังการตรวจสอบคุณภาพอย่างเข้มงวด แผ่นเหล็กจะถูกส่งต่อมายังแผนกเชื่อมชิ้นส่วน เชื่อมย่อยด้วยพนักงานที่มีความชำนาญ ทั้งยังมีการเชื่อมด้วยหุ่นยนต์ เพื่อความแม่นยำและสมบูรณ์แบบในทุกรายละเอียด ภายใต้การดูแลของพนักงานที่มีความเชี่ยวชาญสูง
3. แผนกพ่นสีตัวถัง (Paint Shop) - หลังจากเชื่อมประกอบตัวถังเสร็จ จึงส่งต่อมายังกระบวนการพ่นสี ชุบสีกันสนิมด้วยการเหนี่ยวนำประจุไฟฟ้า เพื่อให้สีกันสนิมเคลือบได้ทุกส่วน และทำการพ่นสีด้วยระบบการพ่นสีอัตโนมัติ ซึ่งใช้น้ำเป็นตัวทำละลาย เพื่อคุณภาพของสีที่สม่ำเสมอในทุกอณูและลดผลกระทบต่อสิ่งแวดล้อม
4. แผนกเชื่อมประกอบช่วงล่าง (Part Shop) - เชื่อมประกอบชิ้นส่วนช่วงล่างของรถยนต์
5. แผนกฉีดขึ้นรูปพลาสติก (Resin Shop) - ชิ้นส่วนพลาสติกจะถูกฉีดขึ้นรูปด้วยเครื่องจักรที่ทันสมัยที่สุดและนำไปขึ้นสี ก่อนจะถูกจัดส่งไปยังแผนกประกอบชิ้นส่วน
6. แผนกประกอบชิ้นส่วน (Assembly Shop) - ประกอบและติดตั้งชิ้นส่วนต่าง ๆ สำหรับรถยนต์ให้เสร็จสมบูรณ์
คุณภัคพงษ์ ภักดีงาม รองผู้อำนวยการฝ่ายผลิต โตโยต้า มอเตอร์ ประเทศไทย (โรงงานเกตเวย์)
ที่มาของการสร้าง “โรงงานเกตเวย์ 2”
จากยอดผลิตรถยนต์ที่เพิ่มสูงในปี 2556 ‘โรงงานเกตเวย์ 2’ จึงถูกสร้างขึ้นบนคอนเซ็ปต์ Simple & Slim ด้วยการออกแบบระบบที่เรียบง่าย ไม่ซับซ้อน ใช้พื้นที่น้อย แต่ได้ประสิทธิภาพสูงสุด เพียบพร้อมด้วยเทคโนโลยีการผลิตที่โดดเด่น ทั้งโรงงานเชื่อมประกอบตัวถัง ด้วยการออกแบบสายพานที่ไม่ต้องขุดลงพื้น จึงง่ายต่อการปรับเปลี่ยนจำนวนการผลิต และร่นระยะเวลาในการเตรียมงาน มีโรงงานพ่นสี ที่ใช้กระบวนการอบสีที่ประหยัดพลังงานและเป็นมิตรต่อสิ่งแวดล้อม พร้อมฝีมือของพนักงานผู้มีความชำนาญและมีประสบการณ์มาอย่างยาวนาน
ซึ่งการผนวกพลังของทั้ง 2 โรงงาน ทำให้โรงงานเกตเวย์มีศักยภาพการผลิตที่แข็งแกร่ง สอดรับกับความต้องการทั้งในและต่างประเทศ และเป็นโรงงานพี่เลี้ยง หนึ่งเดียวในเอเชียแปซิฟิก ทำหน้าที่ฝึกอบรมพนักงานจากประเทศต่าง ๆ ให้ได้มาตรฐานเช่นเดียวกับโรงงานโตโยต้าอื่น ๆ ทั่วโลก
นอกจากนี้ โตโยต้ายังให้ความสำคัญกับคุณภาพของคนเป็นอย่างยิ่งด้วยแนวคิด Happiness workplace หรือการสร้างความสุขในการทำงานให้กับพนักงานทุกคน ไม่ว่าจะเป็นการสร้างสภาพแวดล้อมที่น่าทำงาน ให้สวัสดิการที่ดีแก่พนักงานทุกคน ฝึกอบรมเพิ่มความรู้ความสามารถสม่ำเสมอ และใช้ทีมเวิร์คในการช่วยกันแก้ไขปัญหา แลกเปลี่ยนความรู้ และยินดีในความสำเร็จร่วมกัน ด้วยความเชื่อว่า ‘ความสุขย่อมสร้างงานที่มีคุณภาพเสมอ’
“สำหรับจุดประสงค์ในการยื่นขอรางวัลอุตสาหกรรมดีเด่นด้านการเพิ่มผลผลิตนั้น โตโยต้าเรามีการพัฒนาและเปรียบเทียบในทุก ๆ ด้านมาอย่างต่อเนื่อง แต่สิ่งที่เรายังคิดว่าเรายังขาด คือการวัดผลเชิงรูปธรรมที่เป็นมาตรฐานสากลจากหน่วยงานภายนอก เพื่อที่จะได้รับคำชี้แนะมาปรับปรุงในส่วนต่าง ๆ จึงเป็นที่มาของการยื่นขอรางวัลอุตสากรรมดีเด่นในครั้งนี้ ซึ่งเราก็ทำได้สำเร็จนะครับ”
นิยามของการเพิ่มผลผลิตในมุมมองของโตโยต้า
คุณภัคพงษ์ เล่าต่อว่า จริง ๆ แล้ว บริบทการเพิ่มผลผลิตไม่ใช่เพียงแต่เป็นการเพิ่มจำนวนการผลิตให้มากยิ่งขึ้นเท่านั้น แต่ยังครอบคลุมไปถึงการใช้ทรัพยากรที่น้อยลง แต่ผลิตได้จำนวนเท่าเดิม หรือแม้แต่การผลิตให้เหมาะสมต่อความต้องการของลูกค้าหรือผู้บริโภค ตรงจุดนี้เองที่สอดคล้องกับนโยบายของโตโยต้าที่พยายามมุ่งเน้นความสำคัญของลูกค้า เราพยายามยืดหยุ่นปรับเปลี่ยนตัวเอง ตามความต้องการ ทั้งในเรื่องของจำนวน คุณภาพ และการทันต่อกระแสต่าง ๆ ในสังคม
โดยปรัชญาของคุณสุวิทย์ ไชยประสิทธิ์ รองกรรมการผู้จัดการใหญ่ ซึ่งเป็นหัวหอกของทางโตโยต้าเกตเวย์ ได้วางทิศทางที่ให้ความสำคัญกับความยืดหยุ่นในการทำงาน (Flexible) เพื่อรองรับกับการแข่งขัน บนพื้นฐานจริยธรรมที่ดีควบคู่กัน
ความสำคัญของ Most Flexible ต่อการผลิตรถยนต์
ในแง่ของการเปลี่ยนแปลงของ Takt time ที่ใช้เวลา 58 วินาทีต่อการผลิตรถยนต์ 1 คัน เรามีการปรับสมดุลอยู่ตลอดเวลา ทั้งโรงงานเกตเวย์ 1 และ 2 (ดูภาพประกอบด้านล่าง) เพื่อตอบสนองความต้องการของผู้บริโภคได้ดีที่สุด รวมถึงใช้เท่าที่จำเป็นต่อความต้องการ
ซึ่ง Model Line up สำหรับรถยนต์นั่งส่วนบุคคล (Passenger car) อยู่ที่ประมาณ 4 ปี แต่ยังมีในส่วนของ Year Model การปรับปรุงมาตรฐานรถในแต่ละรุ่น ทั้งรูปร่าง ขนาด สี รวมถึงทุกอย่าง เพื่อให้เหมาะสม กล่าวได้ว่า Gateway model paint เรามีโมเดลใหม่ที่รอขึ้นรูป ขึ้นสี ในทุก ๆ 6 เดือน
เพื่อรองรับความเปลี่ยนแปลงมากมายขนาดนี้ Key point ของเราจึงต้องเป็น “Strong Manufacturing” อย่างเดียวเท่านั้น จึงจะสามารถรองรับทั้งในส่วนของพื้นฐาน การผลิต และต้นทุน ทั้งหมดนี้รวมกันเพื่อต้องการให้เป็นอันดับหนึ่งในอุตสาหกรรมยานยนต์ของโลก การจะไปสู่จุดนั้นได้คนของเราจึงต้องมีจริยธรรมที่ดีเป็นตัวนำก่อน
บทบาทผูับริหารระดับสูงของโตโยต้า เกตเวย์
นโยบายที่ให้ไว้ดังกล่าว จะนำมาสู่ผู้บริหารระดับสูงที่จะช่วยทำให้เกิดขึ้นจริง ทั้งในด้านของคนไทย คุณสมคิด ประดิษฐกำจรชัย และทางด้านคนญี่ปุ่น คุณเคโงะ นิเฮอิ ที่ประสานงานกัน ช่วยกัน โคชชิ่ง ก่อนจะลงมาในส่วนของผู้อำนวยการฝ่าย (GM) ในฐานะลีดเดอร์ ที่จะต้องถูกพัฒนาทั้งในแง่ของกระบวนการคิด การกำหนดนโยบาย กลยุทธ์ในการจัดการ และ change point ที่จะเกิดขึ้นในอนาคต รวมถึง Passion ในการทำงาน เพื่อบรรลุสู่เป้าหมาย ส่วนผู้จัดการในฐานะผู้อยู่หน้างาน ก็จะถูกพัฒนาในการนำกลยุทธ์มาลงมือปฏิบัติจริงอย่างเข้มแข็ง มองจุดเปลี่ยนให้ออก และแก้ไขปัญหาได้อย่างถูกต้องรวดเร็ว อย่างไรก็ตาม HRD เป็นเรื่องที่ซับซ้อนและกำหนดรูปแบบตายตัวได้ยาก การคาดหวังผลก็ยากตาม เพราะคนแต่ละคนมีประสบการณ์มาไม่เท่ากัน ดังนั้นจึงเป็นสิ่งที่จะต้องทำอย่างต่อเนื่องและทำให้มากที่สุดเท่าที่จะทำได้
ซึ่งก็ได้มีการกำหนดเป้าหมาย ความคาดหวังในแต่ละช่วงเวลา ในรูปแบบของ PDCA Cycle ควบคู่กันทั้ง GM และ MGR
จาก ‘บนลงล่าง’ และจาก ‘ล่างสู่บน’ กุญแจดอกสำคัญในการสื่อสารภายในของโตโยต้า
การสื่อสารในระดับองค์กรของโตโยต้า มีทั้งในรูปแบบจากบนลงล่าง (Top Down) และจากล่างขึ้นไปบน (Bottom-Up) ทั้งในระดับสายงานและระดับฝ่าย โดยแชร์ในส่วนของ Company Direction ว่าภาพรวมขององค์กรต้องการสิ่งใด มีการสื่อสารนโยบายรายปี Company-wide ในระดับ GM ขึ้นไป มีการนำสิ่งที่เกิดขึ้นในระดับล่างขึ้นไปบน เพื่อแก้ไขและปรับเปลี่ยนกลยุทธ์ให้เหมาะสม (Familiar talk) การสื่อสารสถานการณ์ของบริษัท แม้ในช่วงโควิดที่มีการล็อกดาวน์ทั่วโลก ทำให้เราขาดชิ้นส่วนนำเข้าจากต่างประเทศ จึงต้องปิดโรงงานเกตเวย์ เราก็มีการนำเทคโนโลยีดิจิทัลมาใช้งาน เพื่อให้สามารถดำเนินการได้อย่างต่อเนื่อง แม้เปิดโรงงานแล้วก็ได้มีการวางนโยบายเพื่อให้เราสามารถอยู่ร่วมกันภายใต้สถานการณ์โควิดให้ได้
- “โตโยต้า” ปิดโรงงานต่อ ถึง 30 เม.ย.นี้
- เลื่อนอีก! “โตโยต้า” ปิดโรงงานเกตเวย์ต่อ ถึง 23 พ.ค.นี้
- โตโยต้า เปิดก่อน 2 โรงงาน “สำโรง-บ้านโพธ์” ด้านเกตเวย์ กลับมาผลิต 25 พ.ค.นี้
นอกจากนี้ ยังมีการติดตามและทบทวนผลการดำเนินงาน (Daily management) วิเคราะห์หาสาเหตุของปัญหา เพื่อสรุปแนวทางการแก้ไขร่วมกันในแต่ละ KPI ทั้งในแบบ Daily, Weekly, Monthly, Quarterly และ Half year
กระบวนการวางแผนกลยุทธ์ด้านการเพิ่มผลผลิตของโตโยต้า
การวางแผนกลยุทธ์ด้านการเพิ่มผลผลิต เป็นส่วนสำคัญที่ทำให้เกิดผลสำเร็จในด้านธุรกิจขององค์กร ทั้งในระยะสั้นและระยะยาว เพื่อการปฏิบัติงานครอบคลุมทุกส่วนงานอย่างมีประสิทธิภาพ
โตโยต้า เริ่มต้นจากการรวบรวมข้อมูลจากปัจจัยภายในและภายนอก โดยปัจจัยภายนอก ได้แก่ ข้อมูลการสั่งซื้อและการคาดการณ์ การมองสถานการณ์การเมือง เศรษฐกิจและสังคม อาทิ โควิด รถยนต์ไฟฟ้า ค่าเงินบาท รัสเซียยูเครน รวมทั้งคู่แข่งที่มีอยู่เดิมและรายใหม่
ส่วนปัจจัยภายใน ได้แก่ Model Change Cycle แบ่งเป็น FMC: Full Model Change (Cycle: 4 years) YM: Year Model (Cycle: 2 years) MNC: Minor Change (Cycle: 2 years)
ในด้านของ Corporate policy การ ‘ทรานส์ฟอร์มธุรกิจ’ ที่โตโยต้าอาจไม่ได้เป็นเพียง Car maker ผลิตรถเพียงอย่างเดียวตลอดไป แต่ยังมองในแง่ของ MaaS (Mobility as a Service) ที่เป็นนโยบายจากบริษัทแม่ โดยอาจเป็นในด้านของรถเช่าและบริการต่าง ๆ ที่เพิ่มเติมเข้ามา
ซึ่งทั้ง 2 ปัจจัยจะถูกนำมาวิเคราะห์ วางแผนร่วมกัน เพื่อกำหนดเป็น Corporate Direction ปรับใช้งานผ่าน Hoshin Kanri หรือการบริหารนโยบายแบบญี่ปุ่น ลงมาเป็นแผนแบบ Monthly > Weekly > Daily และถูกรีวิวตามช่วงเวลาในแต่ละ KPI ที่ได้กล่าวไปข้างต้น
โตโยต้า กับ การวิเคราะห์จุดแข็ง - จุดอ่อน SWOT Analysis
ในการวิเคราะห์จุดแข็ง-จุดอ่อน โตโยต้าใช้หลัก SWOT Analysis (S: Strength, W: Weakness, O: Opportunity, T: Threat) พัฒนากลยุทธ์ในการลงมือปฏิบัติ ให้มีความยืดหยุ่น (Flexible Production) เพื่อให้สามารถรับมือต่อความเปลี่ยนแปลง เมื่อมีผู้เล่นหน้าใหม่เกิดขึ้นในตลาด
ในส่วนของเทรนด์รถยนต์รถยนต์ไฟฟ้า (Electric Vehicle: EV) ที่ทุกคนต่างทราบดีว่ามาแน่ ๆ โตโยต้าจึงได้พัฒนา Hybrid Battery Line เป็นแห่งแรกในเมืองไทย ให้มีความพร้อมมากที่สุด มีเพียง ‘เซลล์แบตเตอรี่’ เท่านั้นที่เรานำเข้ามา นอกเหนือจากนี้เป็นการประกอบภายในทุกส่วนในประเทศ เพื่อต่อยอดสู่ความรู้ทางด้านอีวีในอนาคต
Production Real time มีการวัดค่าการผลิตในทุก ๆ Process การทำงาน โชว์ในรูปแบบดิจิตอลที่ดูผ่านสมาร์ทโฟนได้ทันที
สำหรับ IT Improvement นั้น ด้วยการสื่อสารอย่างมีประสิทธิภาพ ระหว่างโตโยต้าและลูกค้า รวมถึงซัพพลายเออร์ และพนักงานของเรา ทำให้ในช่วงที่มีการ WFH เราก็ยังสามารถดำเนินการผลิตได้
หลักในการเพิ่มผลผลิต (Productivity) ของโตโยต้า
เพื่อรองรับกับการเปลี่ยนแปลงของผู้บริโภคให้ได้มากที่สุดในทุก ๆ ด้าน ทั้งคุณภาพ, ปริมาณที่เพียพอ และระยะเวลาการส่งมอบที่ทันต่อความต้องการภายใต้ราคาที่สมเหตุสมผลกับสถานการณ์เศรษฐกิจปัจจุบัน โตโยต้าจึงมีการตั้งหน่วยงานมอนิเตอร์โซเชียลมีเดียทุกช่องทาง เพื่อรับข้อร้องเรียนของลูกค้าได้รวดเร็วขึ้น ในส่วนยอดขายในประเทศที่เพิ่มขึ้นและเปลี่ยนแปลงอยู่เสมอ เรามีการพัฒนาระบบให้ยืดหยุ่นสามารถเพิ่มหรือลด รวมถึงปรับเปลี่ยนในเวลาอันสั้นด้วยต้นทุนที่ต่ำได้ พร้อมการันตีการส่งมอบรถให้กับฝ่ายขายได้ภายใน 8 ชั่วโมง (100%) และ 4 ชั่วโมง (99.5)
โดยยึดหลักองค์ประกอบ 3 ด้านสำคัญ คือ
INPUT - ใช้วัตถุดิบทุกด้านอย่างคุ้มค่าที่สุด เพื่อให้ต้นทุนอยู่ในระดับที่แข่งขันได้
OUTPUT - ผลิตรถคุณภาพและตรงกับความต้องการของผู้บริโภคทั้งรุ่น, สี และเวลาส่งมอบ
LOSS - ลดการทำงานที่สูญเปล่าและของเสียจากการผลิต รักษาฐานลูกค้าไว้
Flexible all 4M to support changes by Toyota
ทั้งนี้ โตโยต้าได้วางกลยุทธ์ด้านการเพิ่มผลผลิต ที่ใช้ความยืดหยุ่นในการผลิตให้สามารถรองรับกับการเปลี่ยนแปลง โดยมองทั้งในเรื่องของ Market Situation ควบคู่ไปกับ Production Plan
ซึ่งแบ่งออกเป็น 3 ระยะ คือ ระยะสั้น (Short Term) คาดการณ์ 3 เดือนล่วงหน้า, ระยะกลาง (Mid Term) มองแบบปีต่อปี และ ระยะยาว (Long Term) คาดการณ์ 3 ปีล่วงหน้า
ทั้งนี้ ตัวชี้วัดสมรรถนะของโรงงานเกตเวย์ จะถูกแบ่งตามนโยบายที่กำหนดไว้ในด้านต่าง ๆ รวมทั้งหมด 6 ด้าน (Main KPI : 6 Mission) ประกอบด้วย Safety, Quality, Production, Cost, HRD และ Environment
Customer First ตอบโจทย์ความพึงพอใจของลูกค้า
ความรู้เกี่ยวกับลูกค้าและตลาดเป็นสิ่งสำคัญ เพื่อการเพิ่มผลผลิต โตโยต้าได้ใช้กระบวนการปรับปรุงข้อร้องเรียนของลูกค้า ผ่านระบบ ISO9001 ตั้งแต่ผู้แทนจำหน่ายจนถึงผู้ผลิตชิ้นส่วน ในส่วนของโรงงานเกตเวย์ ยังได้นำข้อมูลที่เกี่ยวข้องใน Social Media มาปรับปรุงเพื่อให้ทันกับความต้องการของลูกค้าอยู่เสมอ โดยตรวจสอบ Process การผลิตของเราเอง ว่ามีความเกี่ยวข้องหรือไม่ ก่อนแก้ไขและแชร์ข้อมูลสู่โรงงานอื่น ๆ เพื่อไม่ให้เกิดปัญหาเดียวกันกับรถรุ่นอื่นในโรงงานอื่น ๆ ด้วย
นอกจากนี้ โตโยต้ายังได้สื่อสารข้อมูลความต้องการของลูกค้า ให้พนักงานทั่วทั้งองค์กร รับทราบและตระหนักถึงปัญหาของลูกค้า ผ่านกิจกรรม TOYOTA RESTART DAY ในวันที่ 24 กุมภาพันธ์ของทุกปี ซึ่งโตโยต้าทั่วโลกได้ดำเนินต่อเนื่องมาตั้งแต่ปี 2010 เพื่อเป็นการย้ำเตือนมิให้ลืมความร้ายแรงจากผลกระทบของผลิตภัณฑ์และบริการที่ไม่ได้คุณภาพ โดยถอดบทเรียนเป็น Case Study จากปัญหาคุณภาพที่เคยเกิดขึ้นในอดีต ทั้งจากกลุ่มงานการผลิต, กลุ่มงานการตลาด และกลุ่มงานบริหาร
เพื่อรักษาความพึงพอใจของลูกค้า เราสร้างความสัมพันธ์ต่อลูกค้าที่ดี ด้วยการสื่อสารแบบทันท่วงทีผ่านแอพ T-Connect บนสมาร์ทโฟน และนำปัญหาลูกค้ามาเรียนรู้และปรับปรุงผ่านศูนย์การเรียนรู้ Quality Learning Center ทั่วทั้งองค์กร (2012) และบริษัทคู่ค้า (2018)
ซึ่งมีการลงพื้นที่จริงเพื่อดูปัญหาของลูกค้า และสำรวจรถรุ่นใหม่ผ่าน Initial Market Survey (IMS) สำรวจข้อร้องเรียนใน Internet แล้วนำเสนอการปรับปรุงแก้ไขอย่างทันเหตุการณ์ ต่อผู้บริหารระดับสูงในการประชุมเช้าประจำวัน (Asakai) และ กระบวนการผลิตจริง (Genba) อย่างสม่ำเสมอ แม้ในสถานการณ์โควิดที่ยากลำบาก ภายใต้ปรัชญา
“ลูกค้าคือหัวใจสำคัญของเรา (Customer First)”
- การเพิ่ม Productivity ในแบบฉบับของ ‘โตโยต้า โรงงานเกตเวย์’ (ตอน 2)
- ‘ชิ้นส่วนจากพืช’ ความท้าทายใหม่ของซัพพลายเออร์โตโยต้า
- ทุบทุกสถิติ TOYOTA ทำกำไรสูงสุดเป็นประวัติการณ์
#Toyota #โตโยต้า #โตโยต้าเกตเวย์ #รางวัลคุณภาพแห่งชาติ #TQA2021 #ThailandQualityAward #Mreport #ข่าวอุตสาหกรรม #onlinecontent
บทความยอดนิยม 10 อันดับ
- 10 ตัวอย่างที่นำ 5G มาใช้งานได้อย่างน่าสนใจและประสบผลสำเร็จ
- เทคโนโลยีแห่ง G สู่ 5G เครือข่ายไร้สาย
- แบตเตอรี่ลิเธียมไอออนคืออะไร ตลาดจะก้าวไปในทางไหนในปี 2030?
- เทคโนโลยีสำหรับโลจิสติกส์ ทางเลือกสู่ทางรอด ปรับก่อนโดนเบียด
- นิยามใหม่ SME ใช้ “รายได้” เป็นตัวกำหนด
- ธุรกิจที่ได้รับผลกระทบจาก COVID-19 ปี 2564
- กลยุทธ์การ PR และ Communication ในยุคดิจิทัล
- ปัญหาตู้คอนเทนเนอร์ขาดแคลน เจาะลึกตู้สินค้าหายไปไหน?
- เทรนด์การทำงานในอนาคต หลังไทยติดโควิด นานเกือบสองปี!
- FTA ไทย มีกี่ประเทศ พอหรือไม่ ทำไมต้องคิดเรื่อง CPTPP
อัปเดตข่าวทุกวันที่นี่ www.mreport.co.th
Line / Facebook / Twitter / YouTube @MreportTH