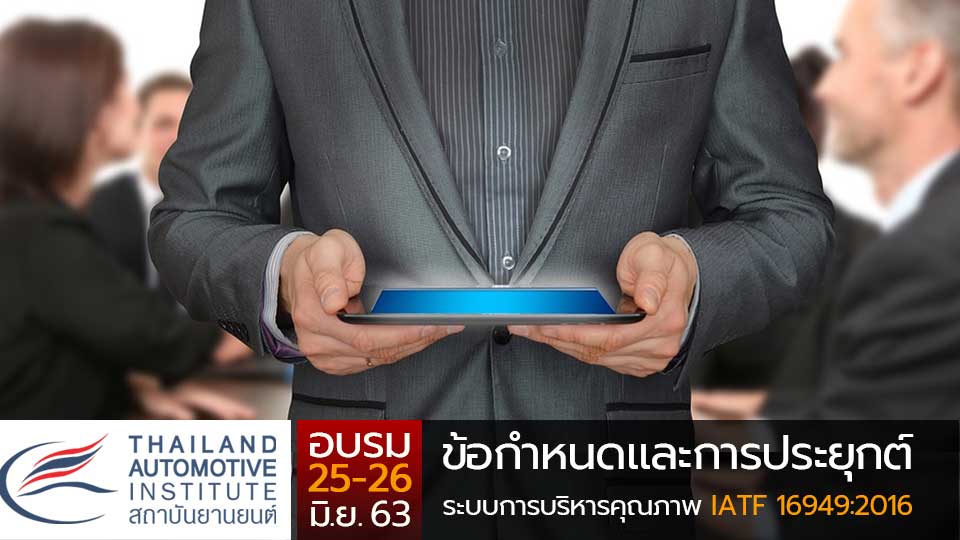
สถาบันยานยนต์ เปิดอบรม “ข้อกำหนดและการประยุกต์ระบบการบริหารคุณภาพ IATF 16949:2016” 25-26 มิ.ย.นี้
สถาบันยานยนต์ จัดฝึกอบรม “ข้อกำหนดและการประยุกต์ระบบการบริหารคุณภาพ IATF 16949:2016 (IATF 16949:2016 Quality Management System Requirement and Practice)” เนื่องจากระบบการบริหารงานคุณภาพ ISO 9001 ได้มีการปรับปรุงมาตรฐานทั้งในส่วนของหลักการพื้นฐาน และ โครงสร้างมาตรฐาน รวมถึง ข้อกำหนดไปจากเดิมมาก ดังนั้น เพื่อให้มั่นใจว่าองค์กรที่ประยุกต์ใช้ระบบบริหารคุณภาพจะสามารถปรับตัวให้อยู่รอดได้ในสภาพแวดล้อมภายนอกที่มีการเปลี่ยนแปลงอย่างรวดเร็วทวีคูณ และ มีความซับซ้อนมากขึ้น ให้สามารถประสบความสำเร็จที่ยั่งยืน ผู้บริหารของทุกองค์กรที่ต้องจัดทำระบบบริหารคุณภาพ จึงต้องทำความเข้าใจถึงการเปลี่ยนแปลงของมาตรฐานฉบับใหม่นี้ เพื่อสามารถที่จะวางแนวทางการปรับเปลี่ยนการบริหารภายในองค์กรให้สอดคล้องกับข้อกำหนดฉบับใหม่ และเกิดประโยชน์กับองค์กรอย่างแท้จริง ผู้ประกอบการและผู้สนใจสามารถเข้าร่วมได้ในวันพฤหัสบดีและวันศุกร์ที่ 25 - 26 มิถุนายน 2563 นี้ ณ ห้องอบรม สถาบันยานยนต์ กรุงเทพฯ
สำหรับสถานประกอบการที่ผลิตชิ้นส่วนยานยนต์ โดยส่วนใหญ่มีระบบบริหารคุณภาพ 2 ระบบคือ ISO 9001 และ ISO/TS 16949 ดังนั้น จะต้องปรับปรุง เปลี่ยนแปลง เอกสารที่มีอยู่ให้เกิดการผสมผสาน ที่สามารถประยุกต์ได้ทั้งสองระบบ เพื่อให้การบริหารองค์กร และการผลิต เป็นไปอย่างมีประสิทธิผล
หัวข้อการฝึกอบรม
- บทนำ/ประเด็นที่มีการเปลี่ยนแปลงจาก ISO 9001: 2008 เป็น ISO 9001: 2015
- ISO/TS 16949 ฉบับใหม่ประกาศใช้ 1 ตุลาคม 2016 แล้ว และเปลี่ยนชื่อเป็น IATF 16949 สิ่งที่องค์กรต้องดำเนินการ ตามกรอบระยะเวลาที่ IATF กำหนด
- ประวัติความเป็นมาของการจัดทำมาตรฐาน ISO/TS 16949
- การอธิบายหลักการของ Process Approach
- การกำหนด customer-oriented processes, support processes และ management processes
การอธิบายข้อกำหนดหลักที่สำคัญ และการประยุกต์ใช้ โดยยึดข้อกำหนด ISO 9001:2015 เชื่อมโยงกับข้อกำหนด IATF 16949:2016
1 บริบทขององค์กร (Context of Organization)ความเข้าใจในบริบทองค์กร (Understanding the organization and its context)
2 ความต้องการและความคาดหวังของผู้มีส่วนเกี่ยวข้อง (Understanding the need and expectations
3 กำหนดขอบเขตระบบการบริหารระบบคุณภาพ (Determine the scope of the QMS)
- ข้อกำหนดเฉพาะลูกค้า (Customer Specific requirements) ต้องถูกประเมินและรวมอยู่ในขอบข่ายของระบบการจัดการ
- ต้องมีกระบวนการที่กำหนดเป็นลายลักษณ์อักษรสำหรับการจัดการผลิตภัณฑ์และกระบวนการที่เปลี่ยนเกี่ยวกับความปลอดภัย (Product Safety)
4 การบริหารระบบคุณภาพและกระบวนการ (Quality Management system and its process)
- การอนุมัติพิเศษสำหรับ Control Plan และ PFMEA การฝึกอบรมเฉพาะสำหรับคนที่เกี่ยวข้อง การสอบกลับได้
5 ภาวะผู้นำ (Leadership) ภาวะผู้นำ และความมุ่งมั่น (Leadership and commitment)
- ความรับผิดชอบขององค์กรต่อสังคมและสิ่งแวดล้อม (Corporate Responsibility) ต้องกำหนดนโยบายหลักปฏิบัติที่เหมาะสม (Code of conduct) สำหรับพนักงานและนโยบายการยกระดับจริยธรรม และนำไปปฏิบัติ เพื่อการดำเนินธุรกิจอย่างซื่อสัตย์ต่อสังคมและสิ่งแวดล้อม
6 นโยบายคุณภาพ (Quality Policy)
7 บทบาทองค์กร ความรับผิดชอบและอำนาจ (Organizational roles, responsibilities and authorities)
- มีการแต่งตั้งตัวแทนคุณภาพ นอกจากกำหนดอำนาจในการหยุดสายการผลิตแล้ว ยังเพิ่มการกำหนดอำนาจการหยุดการส่งมอบให้ลูกค้าด้วย
8 การวางแผนสำหรับระบบคุณภาพ (Planning for the quality management system) การดำเนินการกับความเสี่ยงและโอกาส (Actions to Address Risks and Opportunities)
- การวิเคราะห์ความเสี่ยง (Risk analysis) – ต้องทำการวิเคราะห์ความเสี่ยงอย่างต่อเนื่อง อย่างน้อยต้องควบคลุมถึง การเรียกคืนสินค้า (Recall) ชิ้นงานที่มีข้อบกพร่องเมื่อผู้บริโภคใช้งาน (Field repairs) ข้อร้องเรียน (Complaints) ชิ้นงานเสียที่ต้องทำลายทิ้ง (Scrap) ชิ้นงานที่ต้องซ่อมแซม (Rework) ทั้งที่มีแนวโน้มจะเกิดขึ้นและเกิดขึ้นแล้ว (Potential and Actual)
- ระบุ ประเมินความเสี่ยงทั้งภายในและภายนอกสำหรับกระบวนการผลิตและอุปกรณ์โครงสร้างพื้นฐานทั้งหมด
- กำหนดแผนสำรองตามความเสี่ยงและผลกระทบที่มีต่อลูกค้า เช่น การติดขัดจากการส่งมอบของ Supplier ภัยธรรมชาติ โครงสร้างพื้นฐาน
- ทดสอบประสิทธิผลของแผนสำรอง รวมถึงการจำรองสถานการณ์ (Simulation)
10 วัตถุประสงค์ เป้าหมาย และแผนงานด้านคุณภาพ (Quality Objectives and Planning to Achieve Them)
11 การวางแผนในการเปลี่ยนแปลง (Planning of Changes)
- ทบทวนและอัพเดทแผนดังกล่าว อย่างน้อยปีละครั้ง โดยใช้ทีมคละแผนก (Multidisciplinary Team) รวมถึงผู้บริหารระดับสูง
- บันทึกการแก้ไขเปลี่ยนแปลงของแผนดังกล่าว และผู้มีอำนาจในการอนุมัติการเปลี่ยนแปลง
12 การสนับสนุน (Support) ทรัพยากร (Resources)
- ทั่วไป (General)
- บุคลากร (People)
- โครงสร้างพื้นฐาน (Infrastructure)
- มีวิธีการระบุและขจัดความเสี่ยงสำหรับการจัดทำแผนโรงงาน สิ่งอำนวยความสะดวก และเครื่องจักรอุปกรณ์
- มีวิธีการประเมินความเป็นไปได้ในการผลิต และ ประสิทธิผลของการผลิต และ นำผลการประเมินนั้นเป็นส่วนหนึ่ง ในการทบทวนของผู้บริหาร
- ต้องมีการจัดเก็บบันทึกกิจกรรม การบำรุงรักษาสำหรับ ซอฟแวร์ทั้งหมดที่ใช้ในการควบคุมผลิตภัณฑ์และกระบวนการ (รวมถึงซอฟแวร์ที่ติดตั้งอยู่ในเครื่องมือที่เป็นของลูกค้า และพนักงาน)
- การควบคุมสภาพแวดล้อมในการทำงาน (Environment for the operation of processes)
- เครื่องมือวัด และเฝ้าติดตาม (Monitoring and measuring resources)
- ความรู้ขององค์กร (Organization knowledge)
13 ความสามารถ (Competence)
14 ทัศนคติ Awareness
- ต้องสร้างความตระหนักให้กับพนักงานทุกคนถึง ผลกระทบต่อผลิตภัณฑ์ที่เกิดจากการทำงานของพนักงาน รวมถึง ข้อกำหนดเฉพาะของลูกค้า (CSRs) และความเสี่ยงที่เกี่ยวกับลูกค้าจากการได้รับผลิตภัณฑ์ที่ไม่เป็นไปตามข้อกำหนด
15 การสื่อสาร (Communication
16 ข้อมูลเอกสาร (Documented Information)
- กำหนดระยะเวลาการเก็บรักษาบันทึกที่กำหนดในคู่มือ PPAP (AIAG) เช่น บันทึกของ PPAP, Tooling และ APQP, PO และการเปลี่ยนแปลงจะต้องถูกจัดเก็บรักษาเป็นระยะเวลาตลอดอายุที่ชิ้นงานยังส่งออกเพื่อการผลิตและการบริการ บวก 1 ปี ปฏิทิน นอกจากจะกำหนดเป็นอย่างอื่นโดยลูกค้าหรือกฎหมาย
17 การปฏิบัติ (Operation) การวางแผน และการควบคุมตามแผนงาน (Operation Planning and Control)
- เพิ่มเติมข้อกำหนดที่จะต้องนำมาวางแผนการสร้างผลิตภัณฑ์ คือ ข้อกำหนดด้านโลจิสติกส์ ความเป็นไปได้ในการผลิต (Manufacturing feasibility) การวางแผนโครงการ
18 การพิจารณาความต้องการของตลาด และการสร้างความสัมพันธ์กับลูกค้าDetermination of requirements for products and services
- การสื่อสารกับลูกค้า – พนักงานที่รับผิดชอบในการสื่อสารกับลูกค้า เช่น เรื่องการรายงานกำลังการผลิต การรายงานการแก้ไขป้องกัน ปัญหาที่ร้องขอ ข้อมูลด้านโลจิสติกส์ และ Customer Portal จะต้องได้รับการอบรมเรื่องเหล่านั้น
19 การออกแบบและพัฒนาผลิตภัณฑ์และบริการ (Design and development of products and services)
- เป้าหมายของการสอดคล้องข้อกำหนดผลิตภัณฑ์ ครอบคลุมถึงความสามารถในการบริการซ่อมแซม สุขภาพ ความปลอดภัย สิ่งแวดล้อม
- ข้อกำหนดที่เกี่ยวกับซอฟแวร์ที่ฝังตัวอยู่ในอุปกรณ์อิเลคทรอนิกส์
20 การควบคุมการได้มาจากภายนอกของผลิตภัณฑ์และบริการ (Control of External Provision of Goods and Services)
- กำหนดกระบวนการคัดเลือก Supplier โดยการประเมิน QMS ของ Supplier, การประเมินความเสี่ยงของ Supplier Risk และใช้ทีมงานคละแผนกในการคัดเลือก
- กำหนดเกณฑ์ต่างๆ ที่ใช้เป็นพื้นฐานในการคัดเลือก Supplier เช่น ประวัติคุณภาพ, ความมั่นคงด้านการเงิน, ความสามารถในการออกแบบ, กำลังการผลิต, การวางแผนธุรกิจให้มีความต่อเนื่อง
- กำหนดให้องค์กรส่งต่อข้อกำหนดกฎหมายที่เกี่ยวข้อง และคุณลักษณะพิเศษสำหรับผลิตภัณฑ์และกระบวนการ ให้ Supplier เพื่อนำไปกระจายลงสู่ Supply chain ณ จุดผลิต
21 การผลิตสินค้า และการจัดให้มีการบริการ (Production of Goods and Provision of Services)
- กำหนดและดำเนินการทวนสอบหลังมีการหยุดการผลิต ตามที่วางแผนไว้ (Planned shutdown) หรือหยุดโดยที่ได้วางแผน (Un Planned shutdown)
- Total Productive Maintenance (TPM)
- การวางแผนการผลิต (Production scheduling) ต้องพิจารณาข้อมูลต่างๆที่เกี่ยวข้อง เช่น กำลังการผลิต ภาระการผลิตที่ใช้ร่วมกัน, Lead time, ระดับของสินค้าคงคลัง
22 การส่งมอบผลิตภัณฑ์ และบริการ (Release of products and services)
- พนักงานในสายการผลิตต้องได้รับการฝึกอบรมเรื่องการควบคุมชิ้นงานที่ต้องสงสัยและไม่ได้ตามข้อกำหนด
- การซ่อมแซมชิ้นงานที่เกี่ยวกับความปลอดภัยและข้อกำหนดกฎหมายจะต้องได้รับการอนุมัติจากลูกค้าก่อน
23 การควบคุมสิ่งที่ไม่เป็นไปตามข้อกำหนด (Control of nonconforming)
- ใช้ FMEA ในการประเมินความเสี่ยงสำหรับกระบวนการซ่อมแซม (Rework process) ชิ้นงานก่อนตัดสินใจดำเนินการซ่อมแซม
- กำหนดกระบวนการจัดการชิ้นงานที่ไม่สอดคล้องตามข้อกำหนดที่ไม่ได้นำไปซ่อมแซม สำหรับชิ้นงานที่ไม่เป็นไปตามข้อกำหนดด้านความปลอดภัย และกฎหมายจะต้องทำลายทิ้งจนไม่สามารถใช้งานได้แล้ว ก่อนนำไปทิ้งขยะ
24 การประเมินผลการดำเนินงาน (Performance evaluation)การเฝ้าติดตาม การวัด การวิเคราะห์ และการประเมิน (Monitoring, Measurement, Analysis and Evaluation)
- กรณีที่กระบวนการผลิตไม่สอดคล้องตารมเกณฑ์การยอมรับที่กำหนด ต้องมีแผนการแก้ไข และ กระบวนการยกระดับปัญหา (Escalation Process)
- กำหนดการใช้เครื่องมือสถิติใน DFMEA และ PFMEA
- การติดตามความพึงพอใจของลูกค้า รวมถึงข้อมูล Warranty, Recall และต้องทบทวนข้อมูลสมรรถนะที่ลูกค้าจัดทำให้ผ่านทางเว็บออนไลน์ (Online customer portal) และใบประเมินผลสมรรถนะจากลุกค้า (Scorecards)
25 การตรวจติดตามภายใน (Internal Audit)
- กำหนดความสามารถของ Internal audit เช่นความรู้ Core tools, process approach, เข้าใจผลกระทบต่อลูกค้าจากปัญหาของชิ้นงานและกระบวนการ, เข้าใจการควบคุมผลิตภัณฑ์และกระบวนการ
26 การตรวจสอบการบริหารจัดการ (Management review)
- Management review ต้องทำอย่างน้อยปีละ 1 ครั้ง คามถี่ของการทบทวนต้องเพิ่มขึ้นตามการเปลี่ยนแปลงของภายในและภายนอกที่ส่งผลต่อ QMS และ ประเด็นที่เกี่ยวกับสมรรถนะขององค์กร
- Review inputs เพิ่มเรื่อง การวางแผนอำนวยความสะดวกและอุปกรณ์เพื่อให้มั่นใจว่ามีความเป็นไปได้ในการผลิต แผนการจัดทำ PM , ผลการดำเนินงาน Warranty, Customer, Scorecards, Potential failures จากการวิเคราะห์ FMEA
27 การปรับปรุง (Improvement)การปรับปรุง (Improvement)
- ต้องมีกระบวนการในการพิจารณาการใช้เทคนิคป้องกันความผิดพลาด, รายละเอียดการนำไปใช้และความถี่ในการทดสอบจะต้องระบุไว้ใน PFMEA และ Control plan
28 ความไม่สอดคล้อง และการแก้ไข (Nonconformity and Corrective Action)
- ต้องจัดเก็บบันทึกการทดสอบอุปกรณ์ป้องกันความผิดพลาดในกรณีที่มีความล้มเหลว และชิ้นงานมาสเตอร์ที่ใช้ทดสอบนั้นต้องได้รับการชี้บ่ง และ สอบเทียบ
- ต้องมีแผนแก้ไขในกรณีที่อุปกรณ์ป้องกันความผิดพลาดทำงานล้มเหลว
29 การปรับปรุงอย่างต่อเนื่อง (Continual improvement)
คุณสมบัติผู้เข้ารับการอบรม
- ผู้แทนฝ่ายบริหาร ผู้บริหาร หัวหน้างาน พนักงานที่ดำเนินงานในระบบบริหารคุณภาพและผู้สนใจทั่วไป
ระยะเวลาการอบรม : จำนวน 2 วัน
Download ตารางอบรมประจำปี 2563 คลิกที่นี่
Download ใบสมัครเข้าอบรม คลิกที่นี่
มีค่าใช้จ่ายในการอบรม 4,000 บาท/คน (รวมภาษีมูลค่าเพิ่มแล้ว)
กรุณาส่งใบสมัครภายในวันที่ 18 มิถุนายน 2563
***วันและเวลาการอบรมอาจมีการเปลี่ยนแปลงตามความเหมาะสม***
กรุณาส่งใบสมัครเข้าร่วมโครงการและใบสมัครมายัง สถาบันยานยนต์ โดยผ่านช่องทาง 2 ช่องทางดังนี้
1. Fax : 0-2712-2415
2. E-mail : [email protected] , [email protected] , [email protected] , [email protected]
สอบถามเพิ่มเติมได้ที่
Tel: 0-2712-2414 ต่อ 6701-3