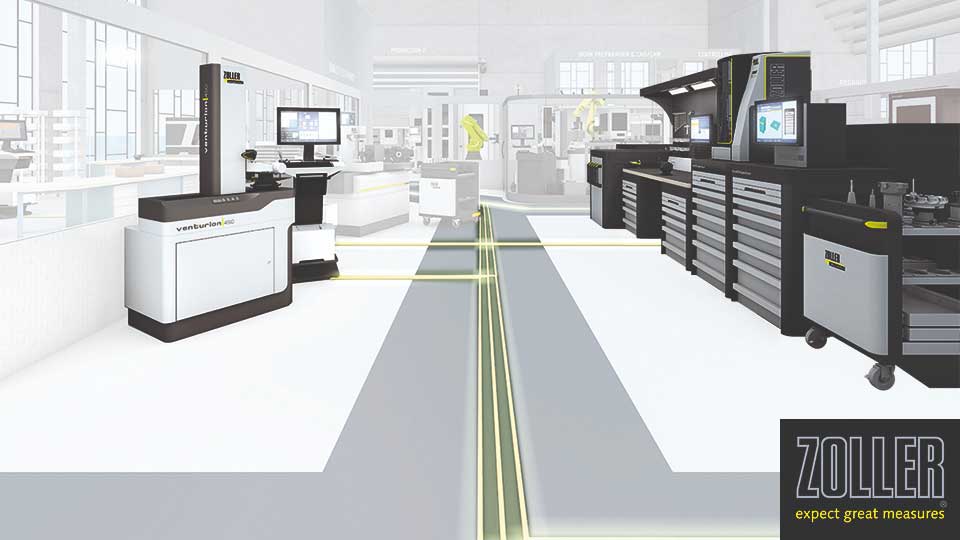
More cost-effectiveness in machining production thanks to communicating, networked systems
A communicative and connectable software is a requirement for the way into the smart factory of the future and offers enormous savings potential in the manufacturing process. ZOLLER recognized this early and today offers measuring machines, storage systems and automation solutions that work with exactly such software: the in-house developed measuring machine software “»pilot«” and the “TMS Tool Management tool” management software.
The measuring machine software »pilot« ensures simple, fast and reliable tool measurement, communication with various production elements and simple operation of the measuring machines. The TMS Tool Management Solutions extend »pilot« by the possibility to manage tools over the complete life cycle and thus to keep tool inventories and costs as low as possible.
The first step is data import
In the manufacturing process, the variable "tool" distinguishes between two variants of data - the target data required for tool setting and the actual data. ZOLLER offers a wide range of options for importing tool target data into the tool database - the simplest of which is data import from the cloud. Parameterized data as well as 2D and 3D graphics, characteristics and technology data can be imported quickly and easily from the cloud into the ZOLLER tool database. Thanks to DIN 4000 standardization, the import from tool portals of tool manufacturers (e.g. Kennametal, GTDE, CIMsource) is even faster. The imported characteristics save the laborious manual input of data and guarantee a process-safe assembly.
Consistent data flow as the basis for functioning processes
The data required for the manufacturing process must be available everywhere and always correctly. A continuous data flow is therefore essential for functioning communication and smooth processes. Both software solutions, both »pilot« and the ZOLLER-TMS, work on the basis of the central "z.One" tool database. Thus, all ZOLLER products, presetting and measuring machines such as tool cabinets, access a database. ZOLLER offers numerous connection options to external systems, such as ERP, CAM and production control systems, in order to guarantee the continuous flow of data across ZOLLER Solutions.
No separate tool data storage in the CAM system
The basis for programming a realistic milling strategy and for the subsequent virtual simulation is the clearly defined tool assembly using individual components via parts lists in the tool management software. ZOLLER offers interfaces to almost all CAM systems, thus eliminating the need for separate tool data storage in the CAM system. Even if more than one CAM system is in use, these systems can be connected in parallel - without any additional effort.
Collision-free manufacturing thanks to digitization
But practice shows that not all challenges have been solved yet. Programmed target data of the tools often do not correspond to the actual data - for example due to assembly errors. This is solved by the »toolrealityCheck« measuring program in the ZOLLER »pilot« measuring machine software. The actual tool contour is recorded on the rotating tool. Then it is checked whether the real tool contour corresponds to the tool used in the original simulation. This ensures that the tool corresponds to the actual machining situation and that collisions can be ruled out.
Correct tool assembly guaranteed
If the setup sheet is available after programming, the real tool can be correctly assembled using assembly graphics including dimensions in the ZOLLER software. When searching for the individual components, the operator is supported by the graphical storage location management and 3D models of the ZOLLER storage cabinets in the TMS Tool Management Solutions software - click, recognize, a grip in the tool cabinet, no long search times.
Always enough in stock: Ordering tools as needed
In order to always have sufficient individual components and tools in stock, ZOLLER offers an optimal tool with the "Ordering" software module of the TMS Tool Management Solutions software. If the minimum stock level is not reached, an order proposal is generated, which is either sent directly or via the ERP system for ordering. Hit/flop lists in the " Storage Location Management " module also evaluate which tools were required very frequently during a certain period and which are rarely used. By substituting these rarely used tools, the storage space can be used optimally and costs for stockkeeping can be reduced.
Touch and Go - secure and fast data transmission
If tools are correctly mounted, measured and adjusted, they must not only arrive physically at the machine, but also digitally - in a fast and safe way. Two factors play an essential role here: clear tool identification and error-free data transmission to the machine tool.
For several years, ZOLLER has been offering the data transmission variant using RFID technology, in which the actual tool data is encoded in a chip and transmitted to the machine. In addition to the RFID chip, ZOLLER today offers a significantly more cost-effective variant: tool identification via a DataMatrix code. The complete tool is uniquely identified via a DataMatrix code attached to the tool holder, scanned on the machine and its actual data transferred directly from the tool database to the tool table of the machine control via the network. It is also possible to prepare the data for control via a postprocessor and transfer it to the machine control system at the click of a mouse.
Data transfer solutions are used today in many production plants and have proven themselves in practice. The investment in a process-safe data transfer pays off for companies of all sizes who want to remain competitive.
ZOLLER has developed a further option for companies with a small machine park that do not have a network connection and still want to bring their actual tool data to the machine in a process-reliable manner: the data transfer variant with the ZOLLER identification code »zidCode«. It requires no network connection, no software installation on the machine controller and is therefore extremely easy to implement. The tool data is transmitted via QR code. The tools are measured on the ZOLLER presetting and measuring machine and all data is printed out on a label encrypted in a QR code. This QR code is then only scanned with the reading device and the data is automatically transferred to the control of the CNC machine. Errors caused by manual data entry are thus excluded.
Communication with index multi-spindle automatic lathes
In terms of industry 4.0, the most advanced data transmission solution to the machine that ZOLLER has to offer in addition to the »flash« tool monitoring software is "digital communication" between machines such as index multi-spindle automatic lathes and ZOLLER presetting and measuring machines with the »pilot 3.0« software.
The current remaining tool life on the machine, its identification numbers and associated orders are called up on the presetting and measuring machine. The measuring device indicates for which tools the warning limit has been reached and which tools have to be changed soon. The operator sets up the relevant tools and receives all relevant information from the central ZOLLER tool database z.One, e.g. assembly sketch and stock information.
At the measuring machine, the optics carrier (CNC version) automatically moves to the target position. After measuring and setting the tool, the measured actual data is transferred digitally to the machine via the file server and printed on a label together with the order number, tool ID and target machine. The code is scanned at the machine and checked with the job number and the target machine to see whether it is the tool intended for the machine. If the result is positive, the position where the tool must be inserted is displayed. If the tool is not intended for this machine, it is rejected and cannot be used - 100% process reliability is guaranteed.
More Information please contact
ZOLLER (Thailand) Co., Ltd.,
Tel: +66 33 002 016
Email: [email protected]
www.zoller-in.com