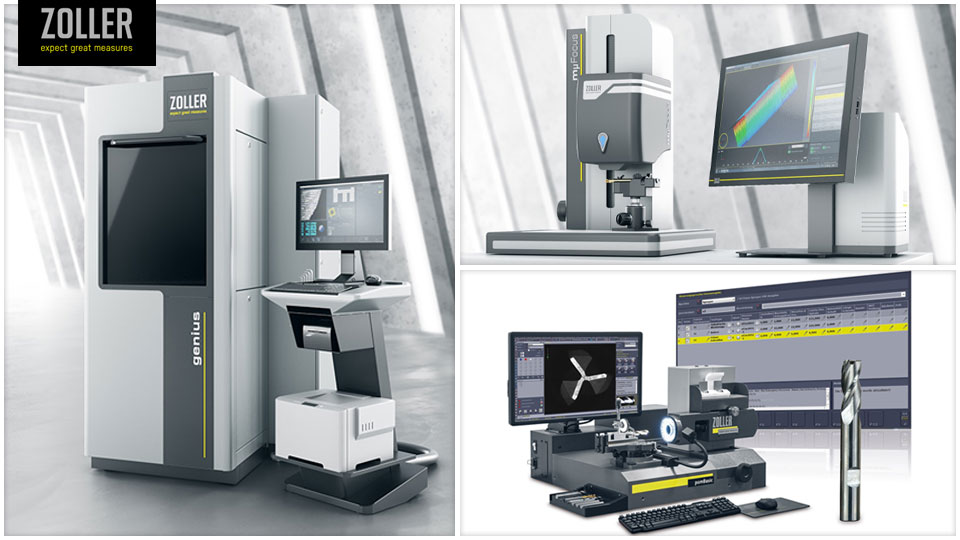
Delivering 100 % accurate high-precision tools with the universal measuring machine »genius« from ZOLLER.
The enemy of good is better
In the world of tool manufacturers and grinders, being the better and always ahead of the game means delivering 100 % accurate tools every day and manufacturing them in our own production facilities with maximum efficiency. The best-selling model that contributes to the production of these high-precision tools is the universal measuring machine »genius«.
Precise tool measurement is common practice in machining production. Measuring accuracies in the micrometer range are standard - because exact components can only be manufactured with tools whose tool geometry data have been precisely determined. With the measuring and inspection devices from ZOLLER, the expert for more economic production, tool manufacturers can determine, record and verify the tool geometry data directly after grinding.
100 % control during tool production
The new measuring technology series »genius« from ZOLLER in new design
ZOLLER offers the right measuring specialist for every type of tool: »genius« for the high-precision measurement of tools of all kinds, »threadCheck« for measuring threading tools, »titan« for determining and measuring the cutting edge preparation, the compact »pomBasic« for the universal inspection of shank tools, »mµFocus« for determining the surface roughness and measuring the cutting edge preparation and »hobCheck« for the fully automatic measurement of hob cutters.
With the unique »pilot« operating software, the ZOLLER »genius« and »titan« inspection and measuring machines measure the tools produced fully automatically in incident and transmitted light, determine all relevant parameters and log them - no matter how complex the tool is designed. At the same time, the new version »pilot 4.0« facilitates the execution of the measuring programs due to its self-explanatory handling and its orientation towards modern operating concepts.
Check off, get started: parameters to be measured are quickly and easily selected in the self-explanatory software interface and »genius« takes over the measurement - fully automatically
The CAD/CAM data of the grinding process are the basis for the measuring procedure. After the construction of the tool and the simulation of the grinding process, these data are sent both to the grinding machine and in parallel to the control of the inspection and measuring machine. At the push of a button, the control generates an automatic measuring sequence - either as a complete measurement or for measuring selected parameters.
The inspection and measuring machines »threadCheck« or »hobCheck« have an additional swivel axis of the optics carrier. With this unique solution from ZOLLER, even tools with a pitch such as taps or hobs can be measured holistically and without distortion.
Automatic inspection with robot support is ideal for particularly high tool throughput. For this purpose, the automation system »roboset 2« can be connected to the inspection and measuring machines »genius«, »threadCheck« and »titan«.
Close to tool production
After the actual tool data has been determined on one of the ZOLLER inspection and measuring machines, it can be transferred back to grinding machines of numerous manufacturers via the »pilot« software. In the control system of the grinding machine, the deviations between target and actual values are displayed directly. The direct data transmission ensures once again reliable processes in the grinding process and saves the operator time and money.
Process-oriented measurement
Proven worldwide, sold over 500 times: the compact inspection device »pomBasic«
The compact, universal »pomBasic« inspection device is the ideal solution for a quick tool check in between. With more than 500 units sold, »pomBasic« can be found in many grinding shops worldwide. It can be positioned directly next to the grinding machine and determines the tool parameters after each work step.
The ground tool is removed from the grinding machine, inserted into the »pomBasic« inspection device and started up, then the inspection starts. Equipped with camera systems and the »pomSoft« user software, also an in-house development from ZOLLER, the edges are automatically detected. This makes the measurement results operator-independent and reproducible. The operator is guided safely through the assisted measuring sequences and the required parameters such as distances, radii or angles are determined.
NEW: The inspection device »mµFocus«
The new inspection device »mµFocus« for optical measurement of cutting edge preparation and surface roughness
The new inspection device »mµFocus« is the ideal solution for all those who want to take a close look at their tools and inserts both in production and in the measuring room. This device is available in two equipment versions for the pure measurement of the cutting edge preparation and for the additional optical measurement of the surface roughness. Besides ergonomic control elements like the easy to move optics, the new, clearly structured and easy to use software and the sophisticated construction for maximum precision, the »mµFocus« is perfect for very smooth and therefore metallic surfaces and at the same time enables a wide range of applications for the most different measuring tasks.
News: ZOLLER inspection device breaks the 500 mark
The »pomBasic« inspection device, the compact solution for a universal inspection of cutting tools, has proven itself worldwide in recent years. Since the product launch in 2014, sales figures have risen continuously, so that the company was able to record over 500 units sold at the end of 2019. »pomBasic« is used worldwide in production, incoming and outgoing goods, primarily for random sample measurements in individual and series production, i.e. for the rapid inspection of a wide range of cutting tools. All face and circumferential geometries are recorded in quick alternation. The automatic edge detection for high accuracy, wizard-guided measuring sequences and test reports at the push of a button make measurement extremely simple. »pomBasic« or »pomBasicMicro« for micro tools are the right choice when basic geometries on the tool have to be determined or compared for running-in.
About E. ZOLLER GmbH & Co. KG
With enthusiasm for inspection and measuring technology, E. ZOLLER GmbH & Co. KG. based in Pleidelsheim near Stuttgart, have been developing innovative solutions for greater efficiency in manufacturing processes for almost 75 years. More than 38,000 presetting and measuring machines with worldwide unrivalled software solutions have been installed to date.
ZOLLER offers everything for efficient and process-reliable cutting tool handling in the manufacturing process. With ZOLLER solutions, tools are digitally and physically recorded, measured, managed, stored, and inspected throughout the entire tool life cycle. An international network of subsidiaries and agents ensures the highest level of service quality with personal customer care.
For more Information, Please contact
ZOLLER (Thailand) Co., Ltd.
111/48-49 Moo 6, T.Don Hua Roh, A. Muang, Chonburi 20000
Tel: 033-002-016
Email: [email protected]
www.zoller-in.com