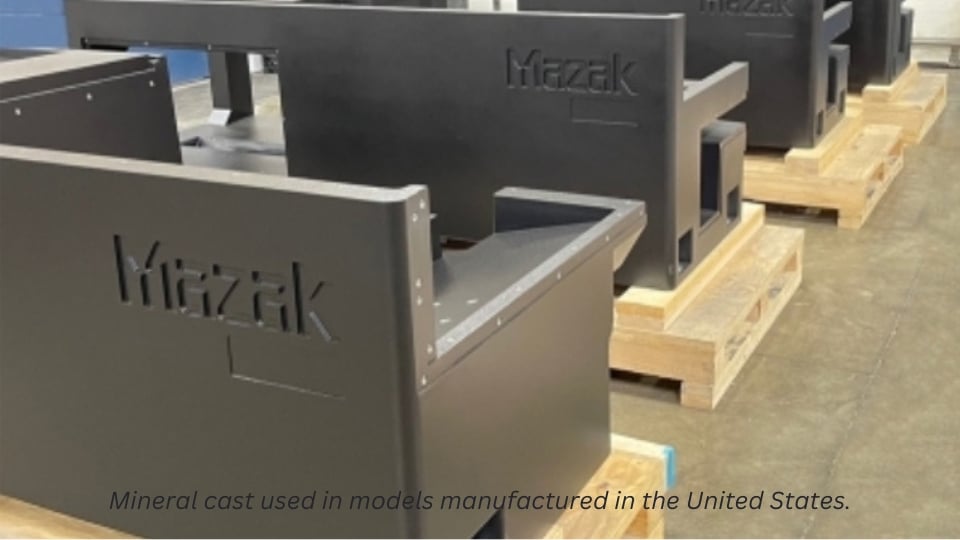
Mazak Commences In-House Production of "Mineral Cast"
Yamazaki Mazak initiates in-house production of 'Mineral Cast' to mitigate parts procurement risk by utilizing machine tool bases instead of castings, offering the advantage of significantly lower carbon dioxide (CO2) emissions during the manufacturing process.
Japan, Dec 25, 2024 - Yamazaki Mazak has initiated efforts to internally manufacture a composite material known as "Mineral Cast." This material, a combination of ore and epoxy resin, will be utilized in structures such as machine tool bases, replacing traditional castings. The company aims to complete technological development for mass production by fiscal year 2023 and commence mass production in fiscal year 2024, concurrently introducing new models featuring mineral cast.
The risk associated with producing cast parts has escalated due to a labor shortage in the foundry industry, prompting us to actively seek alternative solutions for replacement parts.
In Japan, it remains uncommon for a machine tool manufacturer to undertake in-house production of mineral cast. With industry leader Yamazaki Mazak spearheading this initiative and promoting widespread adoption, the integration of mineral cast within the machine tool industry is anticipated to accelerate.
Mineral cast boasts high vibration damping performance and excellent thermal stability, rendering it suitable for constructing machine tool structures. However, in Japan, the number of manufacturers is limited, and the procurement cost, including transportation expenses, exceeds that of castings, hindering widespread usage. Currently, the company incorporates mineral cast from external suppliers into some models.
Recognizing these challenges, the company sought technical collaboration with a mineral cast manufacturer in the United States. After several years of experimental research, it explored the feasibility of in-house production and expanded adoption.
Mineral cast offers the advantage of significantly lower carbon dioxide (CO2) emissions during the manufacturing process compared to casting. Moreover, it can reduce lead time. The company reports an 80% reduction in CO2 emissions and a 60% reduction in lead time. As the transition from castings to mineral casting progresses, we anticipate a reduction in CO2 emissions during machine tool production and shorter delivery times.