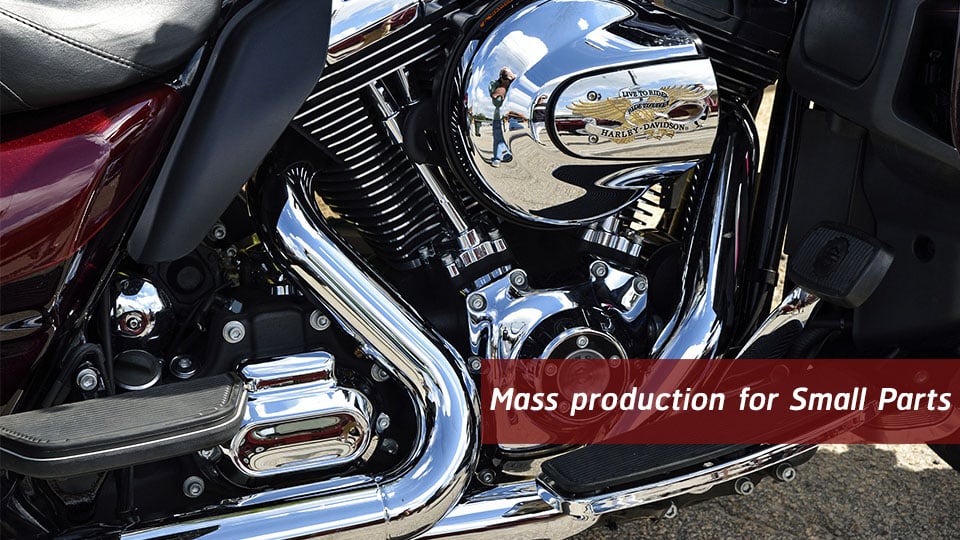
Revolutionary Mass Production for Small Parts
Those who are in mass production for small parts may have known modular production equipment as some plants have been using it, especially for the parts production of cars, motorcycles and compressors. Its economical design that takes only half of the space conventional machinery needs and that can easily be modified are the distinctive advantages.
The modular production equipment has been revolutionized with the installation of built-in robot arms to transport materials in each step or module to the next one. This results in an all-in-one-equipment automatic production.
From “Raw Materials” to “Final Product” with One Equipment
The transfer device and multiple axes robot in a module of DLFn modular production equipment from Fuji Corporation serves as the built-in robot that helps transfer the materials and work pieces swiftly and effectively. This results in an autonomous production, from loading the materials into the equipment to passing on the work pieces of each step to the next one until getting the complete product. These robot arms take only 5.8 seconds to transfer the work pieces and need only 450mm width of space for each module. If the whole production consists of 10 steps, from module 1 to module 10, then it will take totally 4.5 meters in length.
Having known this, the parts manufacturers should consider to adopt this technology in order to be ready for the growth of parts industry that looks very promising. Beside the fact that Thailand has a high probability of hitting the goal of 2 million units in vehicle production, there is a fervency among big-bike manufacturers, marching in to make an investment responding to the growth of big-bike market in Thailand and to make it here a manufacturing base for export.
Big-Bike Manufacturers Concurrently Invest in Thailand
Currently, the big-bike production volume in Thailand is at about 15% of the whole world’s or equivalent to over 1 billion U.S. dollars. Triumph was the first big-bike manufacturer that made Thailand become a significant manufacturing base for export. In 2016, over 40,000 units of big-bike were produced, or 80% of the worldwide sales volume. Meanwhile, Honda moved its manufacturing base for motorcycles under 700cc from Japan to Thailand, producing 16 models of motorcycles for export around the globe. Lately, Ducati has increased its production capacity in Thailand, setting the production goal of 20,000 units per year. In addition, Ducati is planning to produce the new flagship of big-bike “Panigale V4” or “superbike” at Rayong plant to export to Asia market.
As for such well-known U.S. brand as Harley-Davidson, it has already established a manufacturing plant in Rayong province, which is the third facility outside the U.S. It is expected to start the production in late 2018. The Harley-Davidson’s establishment in Thailand not only makes the company stronger and more competitive in the Thai market, but will also be the manufacturing base for export to Asean region and the big market like China.
How the Machinery Operates