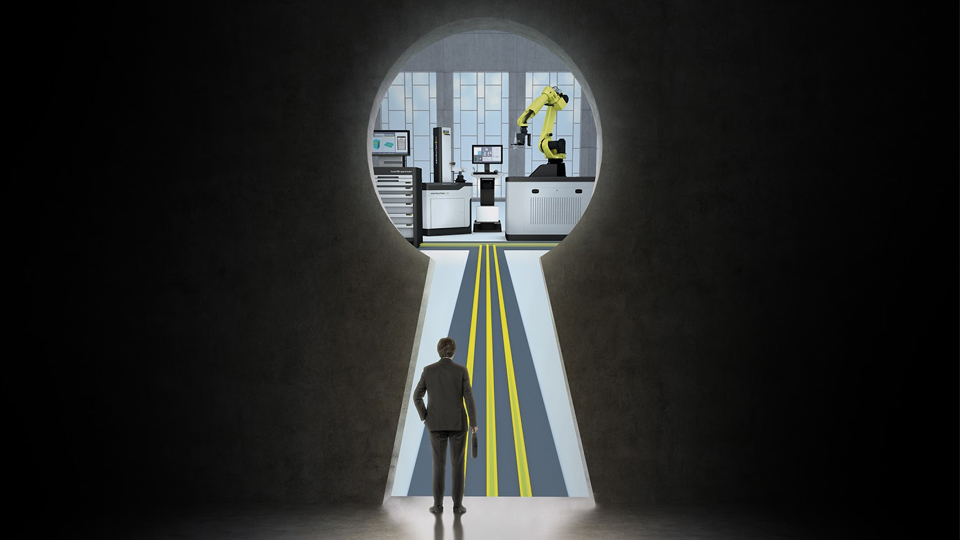
3 Steps to Digitization and Automation in Tool Provision
Thanks to a variety of solution concepts, ZOLLER Solutions can be used to meet any requirements, ranging from small companies to large production enterprises, significantly increasing economic efficiency and productivity in manufacturing processes.
Step 1: The New »zidCode« Communication Platform
The new communication platform »zidCode« can be integrated quickly and easily into a production system without major retrofits to tooling machines, high investment costs or long processes to enter tool data, forming the basis for digital communication between the tooling machine, presetting and measuring machine and ZOLLER Smart Cabinets storage systems. To use »zidCode«, all tool holders in use must be equipped with a unique 2D code. This ensures the system is ready for use. The operator only needs to scan in this code, and the tool data are available immediately in »zidCode« and can be transferred to the machine controller right away.
Tool identification
The basis of all digital and automated production is a unique marking on the tool holder used to identify complete tools. ZOLLER offers the »idLabel« for this purpose. This label is either provided directly by ZOLLER or can be generated locally in the company using the »idPrinter«. Thanks to its resin coating and rugged adhesive force, the »idLabel« is especially well suited for industrial applications – at a very low cost in comparison to other tool identification systems. The system is also flexible: Tool holders can easily be marked with new numbers or number ranges if necessary.
Complete data availability
Complete tools can be added and inventoried in the new »zidCode« communication platform. Once the code on the tool holder is scanned in, the associated tool data are automatically accessed by the z.One database and are available, for instance, to the tooling machine. There, data are first converted to a format appropriate for the controller, then read in. If other tool data needs to be added, such as the magazine space number, this can be done on the display.
»zidCode« can also be used to track the history of any tool. Saved information on the tool's remaining service life makes it easy to decide whether to continue using it. The additional module “Optimized Setup Sheet” can be used to generate tool exchange lists directly on the machine. The “Tool Break” software module reports current tool requirements – for example after a tool breaks – to the machine directly via the »zidCode« in the tool provision. The requested tool appears directly on the display of the ZOLLER presetting and measuring machine, or is available as a storage order to ZOLLER Smart Cabinets. This makes »zidCode« the optimal platform for communication between presetting and measuring machines and ZOLLER Smart Cabinets.
Data transfer via Bluetooth
In addition to simple, safe and convenient data transfer over the network, tool data can also be transmitted via Bluetooth memory chip technology. In this case, measured values are written by the presetting and measuring machine onto a memory chip integrated into the tool cart. Once this tool cart – the »idTransporter« – reaches the machine with the tools, after the tool is identified data are transmitted to the machine controller in an appropriate format and are available for production – everywhere and anytime.
Step 2: Standard Task Transmission to the »cora« Robotic System
Once tool data have been digitized, they can also be used to automate standard processes. The entire production process is on display, from picking the order to inventory and finding single components in the Smart Cabinet cabinet and storage systems, and automatic provision to transporting them to the machine using the robot »coraArm« and the self-driving tool cart »coraTransporter«. The operator can observe all of the production steps at all times via a Smartwatch, using it to approve orders and processes, for instance – from anywhere.
Step 3: Fully Automatic Tool Provision with »roboBox«
The third step is described by the fully automatic assembly of many different tool systems. Assembly and measuring procedures are also saved based on the digitized tool data. These data are used in the
»roboBox«. The modular automation system mounts all current tool systems in a minimum among of space, allowing it to shorten order lead times. Standard assembly processes include screw fitting, heat shrinking and pressing tools.
In addition, an upstream cleaning process ensures precise preparation of the tools, and subsequent measurement of tool geometry data and balance quality ensures the tool data necessary for production are provided. The flexible lock system can be used to adapt the »roboBox« optimally to any production environment.
Automatic Tool Assembly
Automation can also start directly at the ZOLLER presetting and measuring machine. Therefor, ZOLLER offers many new developments and machines.
»torquematic« is used to automate tool provision of tools with collet chucks. The newly developed presetting and measuring machine is equipped with a high-precision spindle with dual drive technology. It can be used to clamp and release collet chuck threaded couplings with torques of over 100 Nm in a fully automatic process, while calculating tool geometry data down to the µm. The »adaptYourHolder« quick change system can be used to align the clamping unit to the specific collet connection of the collet chuck system in seconds.
ZOLLER also offers »screwmatic« as a solution for automatic assembly of tools with horizontally arranged clamping and adjusting screws, such as those used on cylinder shaft tools with Weldon areas or with hydraulic tool chucks. With three CNC-controlled linear axes and a torque-controlled screw axis, any screw-fitting position can be approached precisely to the µm, allowing the screwing process to be carried out exactly.
New Software Solutions
The ZOLLER »pilot« measuring machine software is now available with its new design and new functions. The interface of the new version was specifically kept similar to the previous version, to simplify operation for users. However, there are some changes that make operation even faster and more convenient.
The design of the user interface is now uniform across the entire ZOLLER product range. Handling is self-explanatory and in line with modern operating concepts. Large click and touch areas allow the user to operate the system more quickly. In addition, operators can customize the interface: Widgets, for example, and the color scheme can be adapted to individual operator needs.
Tool management in ZOLLER TMS Tool Management Solutions is now web-based, and can be accessed and operated flexibly from any device, such as a PC, tablet, or smartphone and without requiring an initial installation – just like any other common web application. It is no longer necessary to install the program on a computer. This ensures availability everywhere and on every device. Likewise, updates no longer need to be installed, but are instead automatically uploaded when the program is accessed. This makes use and operations much more convenient for the operator.
The »fingerprint« software function in the main menu of the ZOLLER presetting and measuring machine offers automatic operating data recording for all operating parameters, allowing for a quick, comprehensive system check. The »pilot« measuring machinesoftware checks the functional condition of all system components at defined intervals. This allows system deviations to be detected and corrected early on, before a component failure. In addition, the module includes data recording that can be used for statistical purposes and to help optimize procedures, planning and machine load.