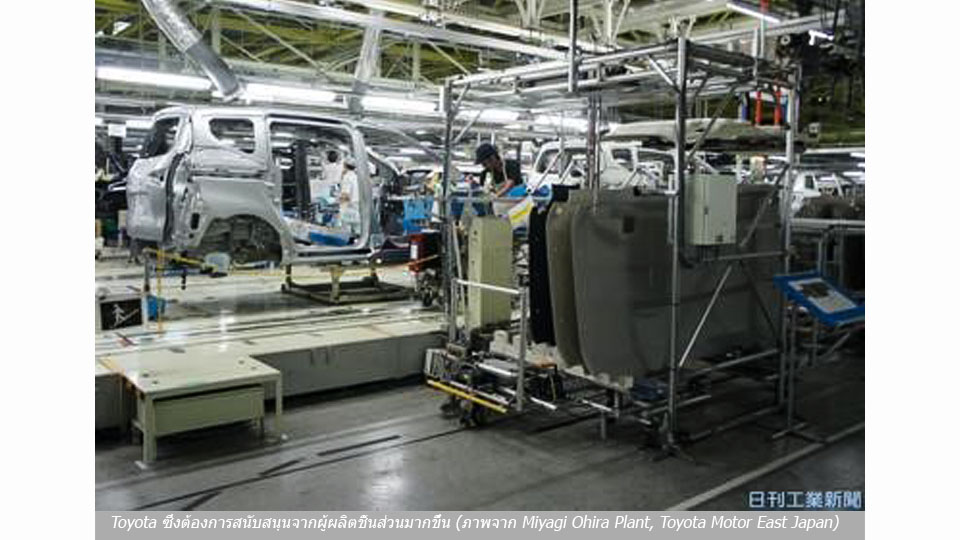
Japan’s industrial sector confronts population decline
The year 2011 was the year of the 6th great crisis of Japan when there were appreciation of the Japanese yen, earthquakes, and tsunami in Tohoku. With responsibility, Mr. Akio Toyoda, Chairman of Toyota had mentioned “No matter how hard the situation is, we have to maintain Japan’s industrial competitiveness.” He had announced to remain the production capacity of Toyota and its subsidiaries in Japan at 3 million units. And at that time, Chairman Toyoda admitted that it was such a surprised and unreasonable action.
Seven years later after Toyota’s success in maintaining its production capacity in Japan at 3 million units per year, the situation of the supplier’s side was dramatically declined. Despite the yen depreciation, the concept of “CASE” which had become an innovation within the automobile industry had caused Toyota to carry more cost burden of parts. In addition, the problem of the population decline had led to labour shortage.
It can be said that the pyramid of Japan’s automobile industry is shaking. Not only the automobile manufacturers who have been affected by such situations, but the suppliers also have the reaction toward the situations. A large parts manufacturer, a subsidiary of Toyota, have looked forward to 2025 when the baby boomers will then be age 75 and older. This will affect the employment as a whole. In preparation for reduction of thousands of people in the future, there is a plan of automatic system implementation and providing training for human resources with investment of strategic planning.
Toyoda Iron Works, a manufacturer of press dies, has initiated a measure since 2014 to maintain its production capacity in Japan at 2.5 million units through the efficient improvement of production line by joining all lines within in a plant as well as utilizing IoT.
Dealing with labour shortage will become a significant problem for each suppliers. For instance, Yokoyama, whose main products are automotive seats, has applied its metal work technology with cocktail shaker production and has shifted its focus to restaurant equipment and appliances. In addition, it will use acquired distribution channels in May for more distributions of “good quality consumable products” such as towels.
In addition, there is a possibility of change in demand direction. For instance, DYNAX, whose products are clutch disc plates for automatic transmission, has accelerated its product development to serve the wheel hub motor product for the EV in the future with FOMM as its joint-investor. Mr. Koji Akita, Chairman of DYNAX said that “Although the demand of clutch disc plates has risen, it is not possible not to develop products to serve the EV.”
It is expected that the dramatic increase of the production capacity in Japan is against all odds. There will be more trading activities between automobile manufacturers and automotive part manufacturers if Toyota wants to maintain its present production rate. And the most important thing is it has to receive supports from the suppliers.