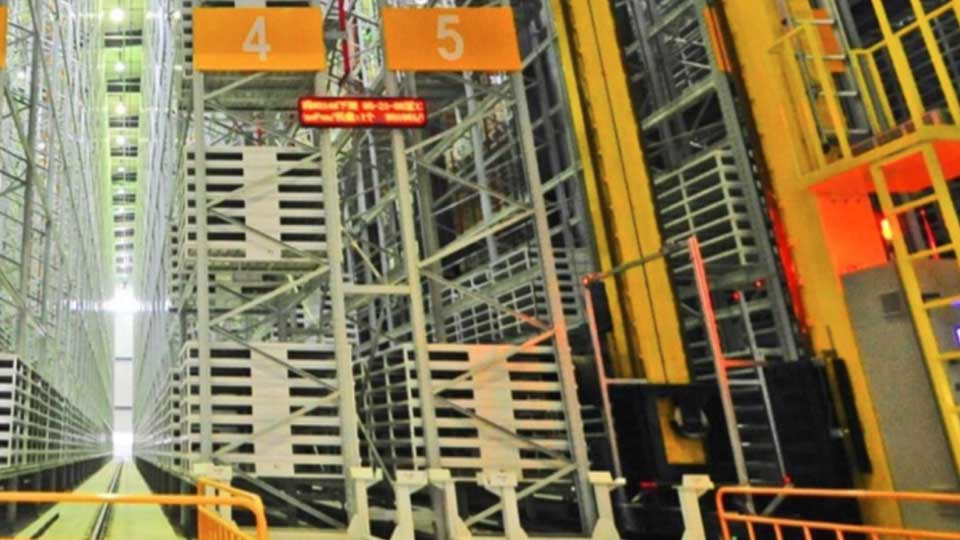
Automated Warehouse Technology: Spiking Trend and Solution to E-Commerce, Food & Beverage
Automated warehouse is the hottest technology of the year for a smart logistics system that has created a turning point for many businesses, especially e-commerce, food and beverage, those of which have invested in building an automated warehouse. It also is a strategy to drive business growth, helps reduce costs and increase management efficiency to improve their competitiveness, including expanding product lines and service coverage.
Nippon Kikai Engineering (NKE), the automation company behind the success of automated machines, has revealed a significant increase in the interest of the industry for smart logistics and warehouse automation, which reflected through investments in various projects from new businesses to improving efficiency of existing businesses.
NKE has partnered with Somboon Siasun Tech (SST) to integrate the networks, knowledge and expertise in order to fulfill the success of adapting and choosing smart logistics solutions for the Thai industry.
What Is Smart Logistics?
Smart logistics is the management of logistics covering the systems of transport, picking and sorting, and storage and packing. The ultimate goal is to achieve the highest efficiency at the lowest cost by using the integration of technologies into each part appropriately and compatibly to increase the time, labor and space management along with safety.
- Increase Efficiency
- Increase Accuracy
- Increase Safety
- Reduce Labor Cost
- Minimize Storage Space
Main technologies have occupied in the smart logistics system composed of racking system, material handling system, conveyor system, warehouse management system (WMS), intelligent algorithm, and total automation solution.
Creating a smart logistics system for each business does not begin with specific technology choices. Instead, we have to set out with the goals and needs of each business, including all the details in the nature of use, limitations and obstacles, and the important thing is the predetermined budget. All of the above, then, leads to the design of a smart logistics system that is truly suitable for the particular business.
However, businesses that are not in the logistics will usually underestimate the importance of logistics. Budgets and resources of a business are often spent on manufacturing processes, product quality development, productivity improvement, and manufacturing costs reduction. Logistics investments are usually made only when problems arise or after other parts of business have been improved. The main problem in logistics is the lack of storage space.
Automated Warehouse Solves the Lack of Storage Space
In the past when technology was not yet advanced, the problem of lacking storage space could only be solved by investing in additional land and buildings. If the business was not ready to invest, renting a storage space could buy them some time. As technology progressed, automated warehouse solutions have become the core of a smart logistics system. There are a variety of solutions to choose from or combine to meet the needs of each business:
#1 Automated Storage/Retrieval System (AS/RS)
AS/RS: Automated Storage/Retrieval System. This technology is often collectively referred to as "automated warehouse," which is often used in materials handling. It is supposed to automatically bring materials to and from the storage rack, in which the position of the AS/RS crane is clearly predetermined for retrieving materials from the storage rack to the pickup station and then to the deposit station. The AS/RS system is suitable for applications that need placing and retrieving a wide range of materials such as a highly dense storage rack.
#2 Automated Guided Vehicle (AGV)
AGV: Automated Guided Vehicle. An automated guided vehicle is controlled by computer. It could be in a trolley, a forklift, or in some other forms. Often, it is referred to as "a robot system used in an automated warehouse." The movement of the AGV is controlled by a combination of software and navigation sensors to safely move materials or products on a predetermined path with precise speed, preventing any collisions through automatic obstacle detection. As for its navigation system, there are a variety of technologies such as magnetic stripe induction motion using magnetic pins embedded in the floor, underfloor wiring, laser detection, automatic navigation mapping, etc. The AGV is most often used in transporting raw materials to support the production line or picking up products in a warehouse.
#3 Automatic Palletizing
Automatic Palletizing: Automated palletizing and handling equipment is a machine or robot specifically designed for loading and unloading pallets before and after transportation. It is able to automatically lift, rotate, and place loads to the predetermined location. Automated palletizer is often used in distribution centers and factories that use pallets for product placement, such as wholesale and retail businesses of consumer goods, agriculture packaging, food and beverage, automotives, etc.
#4 Automatic Picking & Sorting:
Automatic Picking & Sorting. There are many technologies, for example,
- Belt Sorter or Conveyor Based Sorter is a sorting machine using connected conveyors to change the conveying direction to different bases, carrying goods or materials to the next step. This method can transport a wide variety of products and materials, including products in various packaging types. It can hold a lot of weight and can be used in conjunction with other technologies such as vision sensors, tracking systems, automated guided vehicles, loading systems.
- Pick to Light is a system where the “pick tag” devices are used to track the shelf of the product. When the lights flash the position of the items, the operator will pick them up in the quantity ordered by the inventory management system and then press the button to confirm the picking, and the lights will go out. This solution is suitable for picking up products that have been unpacked from big cartons. With this solution, the operator does not waste time searching products and so can pick them up quickly and accurately without the need of printed work orders.
#5 Warehouse Management System (WMS) & Warehouse Control System (WCS)
WMS and WCS is a warehouse management system software that coordinates, manages and controls inventory management orders. WMS maintains a record of each SKU's inventory, its quantity, its in-out movements, storage location, and sends inventory order data to WCS to control the order execution such as storing, picking, packing, counting.
#6 The Advantages of Automated Warehouse
As we can see, there are various technologies used in automated warehouses; each has its own advantages. When comparing a general warehouse with an automated warehouse, the main difference lies in the storage area. The AS/RS system, especially, focuses on the use of aerial or vertical space, which can reduce the use of horizontal space by approximately 60%. Next is labor saving. An automated warehouse requires less staff by up to 70%, which leads to warehouse energy saving. With automated machines, the warehouse can operate 24/7 as well.
In addition, an automated warehouse can meet the needs of precision with WMS, which supports accurate and precise storage and disbursement tasks. It also facilitates a FIFO or other management concept because the system knows which product or pallet comes first, which can reduce human errors.
And finally, safety. The automatic operation of machines can reduce the risk of accidents to employees, for example, using a crane to run along a track instead of a forklift can reduce the risks for employees as well as damages to products and shelves.
Trends and Concepts - Choose Warehouse Technology in Smart Logistics
The automated warehouse is currently used in medium and large businesses. It is most used in the e-commerce industry, followed by the food and drink, the retail and wholesale, where there are a wide variety of products, the modern trade group, and convenience store franchises.
Lately, when the e-commerce business exponentially grows, an automated warehouse has become needed for speedy and accurate delivery, which is crucial on the competitive market, especially to those with a wide variety of products and lots of orders. By bringing in mini-load AGVs to the warehouse in place of employees, they will be able to reduce the walking time to find products.
Generally speaking, those in the food and beverage industry can use AS/RS with height since most products are not too heavy and they need to be in and out quickly as they can expire. The AS/RS can also replace human labor in storing and disbursing products very well. In cases that there are a wide variety of products, an automatic picking system can make picking items from different pallets easier and faster. For the refrigerated and frozen food businesses, an automated warehouse is often used to save space and reduce the costs of building refrigerated storage to store products.
To determine the basic suitability, a business may decide from the current functions and applications in the warehouse, the area of warehouse, and goods and materials in the warehouse. This will make the most of the investments. Consulting an expert to work together to find the right solution for business is also a good alternative in choosing technology