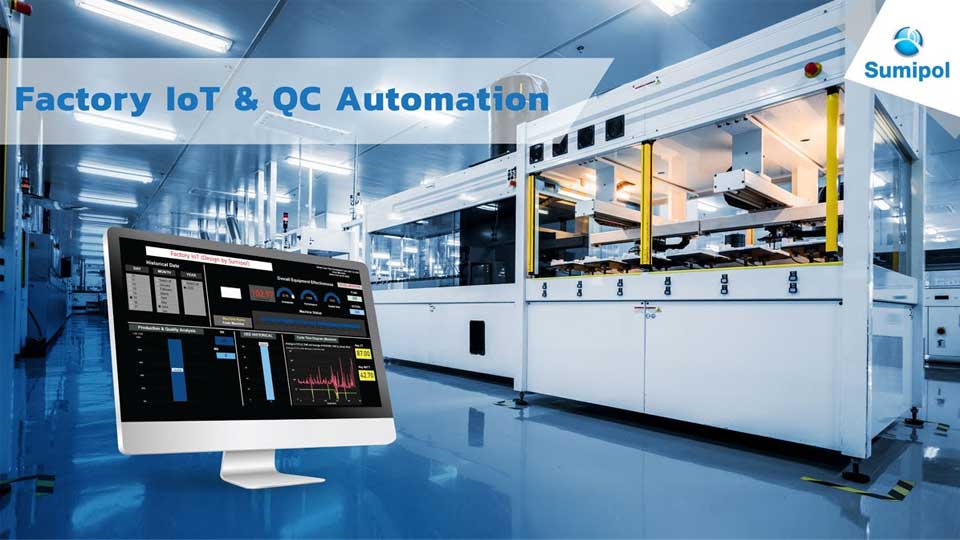
Factory IoT and QC Automation Improve Production Lines More Competitive
In a modern world where the environments have totally changed, digitalization has been playing an important role in all areas, including the manufacturing sector. It utilizes the Internet of Things (IoT) by integrating into the production processes and workflows, especially the ability to see the entire information precisely and instantly. This is the distinction that no tools can ever do before and so it changes the way of thinking in the modern world completely.
Factory IoT has become an important tool in a manufacturing plant, in which it strengthens the competitiveness of the business continually. It truly allows us to see the whole factory, including how each machine is working. It allows us to see problems and to correct them directly, or even to set a preventive plan. It can also analyze the information to improve the efficiency of the production lines in order to bring out high-quality products with the best costs and deliver to the customers within specified conditions and schedules.
In each manufacturing process and step, it has to be set the working parameters and all the requirements of the to-be-manufactured products. These settings and requirements really need a good quality control (QC). Like the factory IoT becomes a helping hand, there is a tool to increase the efficiency in quality control: QC Automation.
In this article, we will delve into “the two technologies at the heart of factories with competitiveness: factory IoT and QC automation,” which Sumipol Corporation Limited has piloted to encourage the manufacturers in Thailand to consider in order not to be outdated and forgotten factories.
l Factory IoT Improves the Efficiency of Production Lines to be Lean Manufacturing
Factory IoT is a system that connects all the devices in the production lines with an internet network. It collects data from those devices, e.g. material detectors, CNC machines, PLC devices, mechanical robot arms, and reports in graphics the status of the production lines or any errors, so the users can understand easily and take the information to further analyze.
To collect the data, it relies on the sensors installed on machines and automation systems or those additionally installed to enable the machines to know the status of production, including the distance between the tools and workpieces, temperature, working duration, and the quality of the workpieces.
The data collected from the sensors will be transmitted via the data logger, which can be either wired or wireless, and either store the data in a server or a cloud system, to the automatically detecting device so that it can alarm any error timely. The manufacturers can choose the logger to fit their business by considering its price and usage. They may also consider to rent it monthly or yearly.
Working Structure of Factory IoT
Last, but not least, is the display of the information in easily understandable forms like graphs, statistic tables, dashboards that can be customized to meet the specific needs of each production line. They help the managing executives and related staff to see the information overall and to make a decision more easily and quickly, optimizing the use of the machines. A good software should be able to collect data and display it as the client’s needs without any additional programming skills. It also should help in recording, notifying, and dispersing the information conveniently.
Sample of Display
The benefits of Factory IoT are the following:
- Connected factory enables efficient and eliminated blind-spot communication between machines.
- Production visibility to identify the status in real-time
- Improved productivity by identifying loss and problems that arise in the production process
- Improved quality by measuring and analysing data to protect defects.
- Predictive maintenance to minimize machine downtime
Evidently, the information collected will help in controlling the production process conveniently with easy tracking the status of each production step. It also helps minimizing losses, increasing productivity and leads to developing production lines to be a higher precision, more accurate and precise product manufacturing process that will lead to the next phase of production improvement to be lean manufacturing.
However, there are still many factors that prevent companies from taking full advantage of factory IoT. So they need to rely on a highly experienced expert to support their deployment of IoT that fit their current needs yet is flexible enough for other scenarios as well as the next phase of expansion. Factory entrepreneurs must have a thorough understanding of the operating nature of their business, the possibilities of various cases, as well as their systems of ordering, manufacturing and delivering products. That is because the data collected and analyzed by the factory IoT will affect the operating decision of each next department in the organization. The operating factors like personnel, funds, equipment and machines must also be favourable. In order to effectively use the IoT system, funds are required to upgrade equipment unless there are basic equipment that can be applied to the IoT technology. Since the IoT system is highly complicated, it is imperative to have a team of reliable experienced experts to maximize the IoT deployment.
l QC Automation: An Automatic Quality Controlling System
The quality control is indispensable for high-performance production lines. With this technological advancement, traditional quality control has been transformed into an automation with devices such as slide rails, conveyors, robotic arms, along with quality inspecting devices.
Designing a highly efficient QC automation system requires experts with lots of experience to design specifically to suit the workpieces and working area of each customer as well as to choose various measuring instruments and measuring devices that work well together.
The key benefits to QC automation is the reduction of errors arising from the traditional way of working with employees and the instant acquisition of information. This makes the quality control achieve high accuracy and less costs even when it comes to quality inspection of large quantities of workpieces.
Sample of QC automation system designs
The benefits of QC automation are the following:
- It shortens the inspection time, making it possible to inspect more workpieces.
- It reduces inspection errors compared to those made by humans.
- It can automatically store the inspection measurement information, reducing the step of taking notes of such information for further analysis.
- It can be customized to meet the needs of each customer.
For those who are planning to improve the production line to be more efficient, just getting advice from Sumipol Corporation and Sumiphon Group companies’ experts and system integrators.