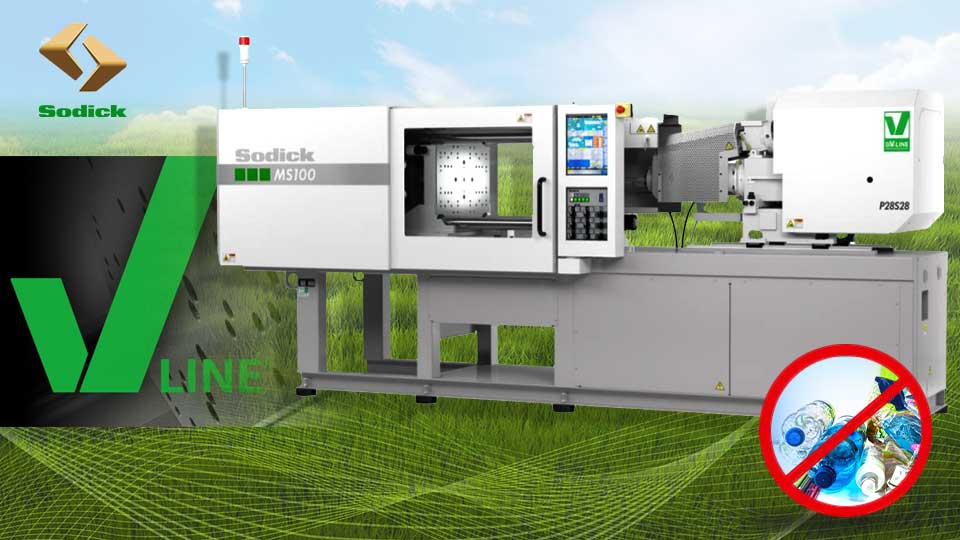
Sodick Technology’s V-LINE® Integrated with INFILT-V for Higher Precision of Biodegradable Plastic Injection
The V-LINE® technology integrated with INFILT-V enables an excellent biodegradable plastic injection molding of producing thin, highly complex workpieces and those requiring high precision, which helps reduce the amount of plastic waste.
"Plastics" is a very popular polymer material in the industry since it is lightweight, inexpensive, easily processed, can be used in a variety of applications, and can last up to several hundred years. Nowadays, up to 400 million tons of plastic are produced annually worldwide, making plastic waste one of the top environmental concerns. In addition, the amount of plastic tends to increase twice every 10 years, resulting in continuous efforts to find plastic substitutes. Biodegradable plastic is one of the options that are currently at the center of attention.
Biodegradable Plastic
Biodegradable plastic is plastic that can decompose in the natural environment, relying on microorganisms in water or soil to decompose the material, which is typically made from recyclable biomaterials, into carbon dioxide, water and other biomass.
However, biodegradable plastic is a material that is harder to work with in the injection molding process than conventional plastics. Its high viscosity when being melted complicates the process of forming thin or very complex workpieces and those that require precision.
V-LINE® Plasticization and Injection System: Technology from Sodick
Due to the above-mentioned limitations, Sodick offers a V-LINE® system for injection molding machines to increase accuracy. Basically, the injection molding involves the three processes of "plasticization" for melting the pallets, "weighing" for measuring the required volume, and "injection" for feeding the plastic. With the V-LINE® system, the processes of plasticization and injection are separated but are handled along the same axis by the inline screw system. The screw and injection cylinder are arranged coaxially.
A feature of the inline method is the check ring that moves backward and forward to shut off the plastic flow. Addition, the ring allows the plastic to flow freely during plasticization but shuts off the backflow of plastic during injection.
In the process of plasticization, plastic pellets are melted through a screw rotation and the heat from the heater. The screw will rotate in the same direction and position to maintain the process of thermal history so that the plastic resins are in a constant melting state. The liquid plastic is then fed into the plunger controlled by the linear servo valve drive system for accurate and precise injection. The screw stops at the desired location once the required amount of liquid plastic is reached and then moves in to close the flow.
In the process of injection, the screw that closes the liquid plastic flow prevents it from flowing back during injection molding, making the liquid plastic injected into the mold with the exact amount required. This is different from conventional inline injection molding machines, in which the nozzle and screw are in the same plane, causing the liquid plastic to flow back and resulting in inconsistent quality of workpieces.
In the V-LINE® system, the screw is used to melt the plastic pellets only. Without functioning in the injection of plastic into the mold, it keeps the temperature of liquid plastic stable, enabling the precise control of injection molding and reducing the shear forces, the wear and tear of various components as well as the excess heat while delivering plastics.
INFILT-V: Inert Gas Infiltrate Molding System
Sodick recently revealed the development of V-LINE® technology integrated with the INFILT-V system, which is an inert gas infiltration technology. The inert gas will act as a plasticizer, which is an additive that reduces the viscosity of liquid plastic and enables both thin and thick plastic injection molding easily. It is the first time in the industry that inert gas injection technology has been used in such injection molding for biodegradable plastics.
The components of INFILT-V and V-LINE® Systems
According to the test using bioplastics, polybutylene succinate (PBS), as a raw material and carbon dioxide as an inert gas, it showed that the INFILT-V system was able to produce excellent plastic cups with a height of 105 mm and a thickness of 0.4 mm. It also showed that the plastic could flow 18.7% longer with 48.3% lower injection pressure.
Comparison between plastic cups made from conventional injection molding machine (left) and from one with INFILT-V system (right)
The INFILT-V is used in conjunction with the V-LINE® system for injection molding machines to make plastic injection more effective. The inert gas is injected through the plunger, which allows the measurement of liquid plastic content and so the plastic injection is more accurate.
The V-LINE® system offers a new approach to the machine's plastic injection molding process, while the INFILT-V system solves the problem of liquid plastic viscosity. When these two innovative technologies from Sodick are integrated, surely, they are the solution of a green world where the needs for production of biodegradable plastic workpieces will grow steadily.