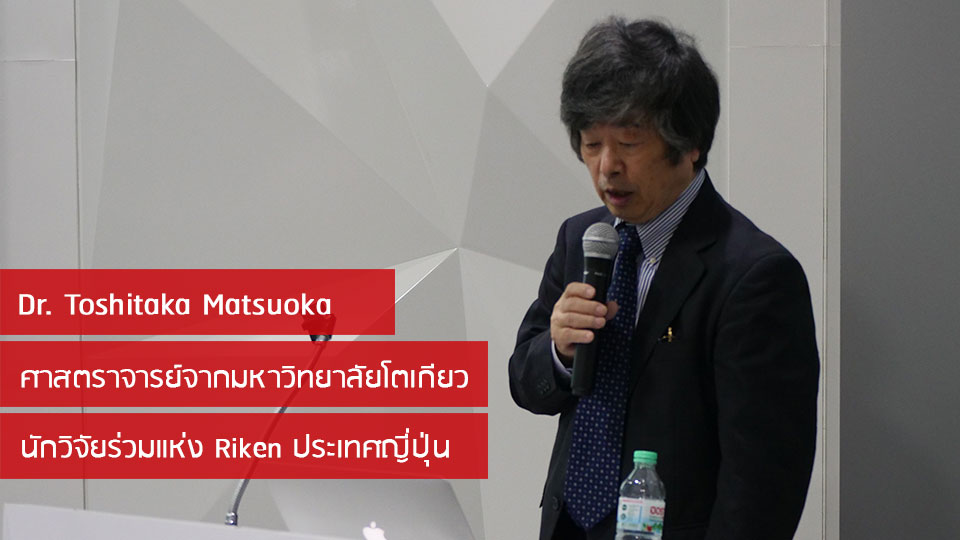
Three Technological Trends for Parts Manufacturing
On November 19, 2018, “The Latest Technical Trend Seminar,” which was co-hosted by Factory Max, NS Tool, and Sodick, was honored to have a distinguished speaker Dr. Toshitaka Matsuoka, a professor from the Faculty of Engineering at Tokyo University and a collaborative researcher at Riken, the largest research institute in Japan and one of the leading experts in manufacturing technology. At the seminar, Dr. Matsuoka commented on the trend of milling technology for parts manufacturing industry in the information technology era; there are three interesting points as follows.
1. Machines on the Database
In the information age, effective production is dependent on data collection. To raise the quality of production, each manufacturer needs to have its own treasure trove of data or cloud infrastructure for internal use.
The data directly affect production as it is a contributing factor related to the machine and automation that can determine how effectively work can be done. That is to say, good information can lead to more effective function of the machine. For example, if the machine can autonomously choose the right tools, production will be faster and meet demands better.
The database should not be limited to just the information from the manual on which and how materials to set up, but should store other information in details, such as the length of the tool, the type of materials, the spindle speed, the coolant and even the type of process. Such details will enable the machine to choose appropriate approach and right tools. These smart features can promote reliable production system and can work effectively in real settings.
In the future, in addition to using the information, all machines will be more connected. This is called "Mieruka (or visibility)" in Japanese in order to be able to monitor the process at every step at any location. Work processes are integrated, so the machines can work autonomously. Even the quality control detector will be a part of the system in order to check whether the workpiece being done is complete for the next step and make corrections itself, if any.
Such connective quality has urged a number of machine manufacturers to see that a controlling panel for each machine is unnecessary as they can develop controlling function embedded in smartphones or tablets which are easy to attain, convenient to control, and can remotely control the machines.
In the beginning, machine users can install additional equipment so that the machines that they have can be connected to other machines. However, in the future, those who need more work precision may need to consider acquiring a new machine as it may serve the purpose better in this information technology era.
2. End Mill Technology
Nowadays, an end mill is a really important part of the production, especially as of lately since the smartphone and the aircraft industries have grown rapidly, there have been changes in the materials used in production, such as the use of stainless steel in smartphone parts, as well as the continuous emergence of new materials such as Inconel (nickel alloy), CFRP (carbon fiber reinforced polymer). The development of end mill, therefore, is becoming a trend in which many manufacturers do a research on in order to better meet the variety of milling needs in the market.
In the past, the milling cutters for grooving work were usually of two sharp edges, but in the future, the development of the end mill will focus on two main points as follows.
- Development for high feed work
- Changing the shape of the end mill to suit the 5-axis machine
Both of these are developed to maximize the work efficiency. For traditional milling with the end mill, the center point of the end mill does not have a shear force, in other words, the Vc equals to 0.
Dr. Matsuoka proposed a change in the milling method from milling at the right angle to milling around the edges instead. An increase in the number of cogwheels can reduce the size of scrap, enabling the machine to work faster and minimizing the problem that may occur to the machine.
From the experiment, it was found that the milling at the outer edge in the oblique angle with a high Vc can reduce the wear of the end mill, which can prolong the end mill’s service life.
At present, manufacturers are actively developing the end mill to provide a more suitable value for the work. Dr. Matsuoka has developed an end mill with the ability to cut at high speed yet with precision and better surface appearance. By comparing the work between the end mill with 2 cogs and one with 4 cogs, it was found that the 4-cogged end mill was able to cut the same job with only half the time of the 2-cogged model. Additionally, the chance that the end mill will be worn out is way much lower than Dr. Matsuoka had anticipated.
In addition, the milling of materials with high ductility such as aluminum, copper and others can be easily operated. However, there is still a problem in the work surface. Using a sharp edge that is exceptionally sharp and controlling the cutting with precision will be able to cut more refined work piece.
Dr. Matsuoka also suggested that in stainless steel milling, using a high cutting speed at 200 meters per minute (Vc 200) will give the best results. The results from low Vc milling are almost no difference in both workpiece and tool wear. However, this high-speed milling can speed up the work.
3. 5-axis Machine Is the Future
Currently, the machines that are widely used are 3-axis machines. However, Dr. Matsuoka said that in the future, 5-axis machines will become the main trend, completely replacing 3-axis machines eventually.
The important factor that will make the 5-axis machine replace the 3-axis machine is the "end mill’s length". The 5-axis machine uses an end mill that is shorter than that of the 3-axis machine, allowing the machine to hold the tool firmly at higher speed and reducing the bending of the tools. In addition, the structure of the machine can adjust the angle of the workpiece freely, making it possible to use a shorter end mill to cut the piece more deeply and thoroughly.
Another important thing is the 5-axis machine is suitable for workpieces that need to be milled from many angles. Unlike the 5-axis machine, the 3-axis machine requires the user to remove the work piece and rotate it in different angle before continuing the milling.
For this reason, the cutting tools manufacturers have accelerated the development of the end mill that is shorter in length and has more sharper edges but no cutter in the center in order to be able to work on the product more quickly. Such 5-axis end mill machines in the future will be very different from the present ones to support the milling of the workpiece in different tilt angles
Dr. Matsuoka added that even though the self-developed CAM is used in the experiment for maximum results and programming for 5-axis machines is more difficult than 3-axis machines, many manufacturers now focus more on 5-axis machines. They developed software to make this difficult task easier. Therefore, there is no need to worry about the progress in the development of technology of each department involved.