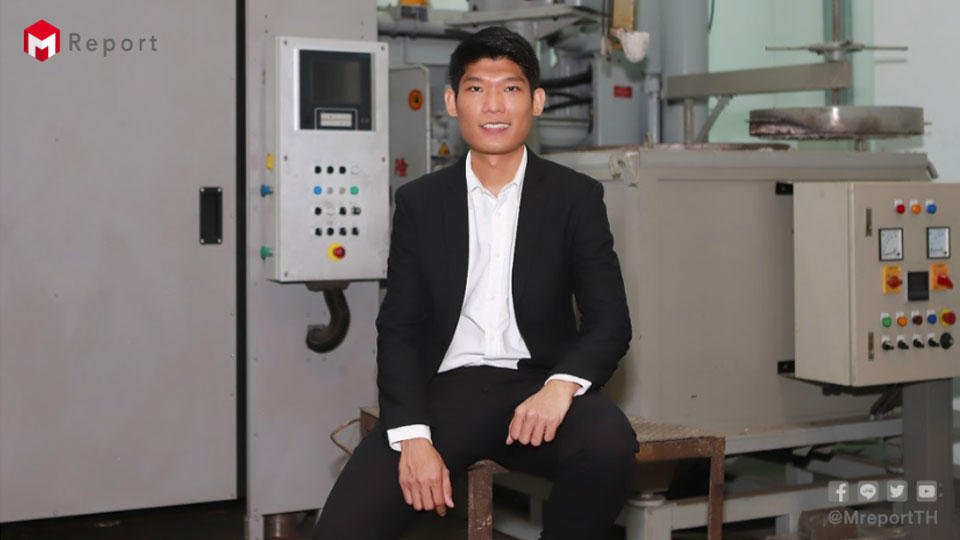
‘Aluminum’ as advanced material of EV era
With the rise of electric vehicles, aluminum serves as an advanced material that enables the automotive sector to move forward while lowering carbon dioxide emissions.
"Advanced materials" refers to advanced or progressive materials, no matter what type of substance. The demand for these materials is increasing to keep up with the rapid growth of technology.
In an interview with M Report, Assistant Professor Dr. Promphong Pandee, a lecturer at the King Mongkut's University of Technology Thonburi (KMUTT) Faculty of Engineering's Department of Production Engineering, said the following:
‘Aluminum’ as advanced material of EV era
Asst. Prof. Dr. Promphong began by mentioning how fascinating aluminum is, that it is an easy-to-form, lightweight metal that has a high strength-to-weight ratio and is three times less dense than steel. As a result, aluminum has long been utilized in large quantities in the manufacture of many different items, and demand just keeps rising.
With its exceptional quality of being "light metal," aluminum is used to reduce the weight of many products in the automotive, aerospace, construction, and other industries. The global electric car maker like Tesla is one example that uses aluminum in the production of EV parts.
Aluminum has several benefits beyond weight reduction, including the ability to be recycled and reused almost entirely. Because of this, a lot of aluminum-based items contain recycled components.
Smelting is the process used to recycle aluminum, and it uses a lot less energy than smelting ore. With the right methods, aluminum's quality may be maintained.
Additionally, the aluminum die casting procedure will produce aluminum workpieces with "near-net shapes," or workpieces whose shape is very similar to the final workpiece intended. It streamlines the procedures needed to complete the details. As a result, they can complete tasks rapidly and effectively enable the development of complicated shapes.
Many parties agree with the claim that "aluminum" is an "environmentally favorable material." Numerous products that strive for environmental friendliness throughout their life cycles use aluminum extensively.
These features make "aluminum" of interest to the Faculty of Engineering at King Mongkut's University of Technology Thonburi, which sees aluminum's potential to satisfy the needs of a world subject to growing environmental concerns, leading to the research of new grades of aluminum alloys.
Ecoline S Series Die Casting Machines - Bühler Group
at the King Mongkut's University of Technology Thonburi (KMUTT) Faculty of Engineering
“Al-Ni alloy” : research that got expanded upon after being published in prestigious journals
“Aluminum" has some drawbacks, though. It is less heat-resistant than steel because it has a lower melting point. Additionally, it is less durable at higher temperatures and has a lower fatigue strength than steel. However, due to the numerous benefits of aluminum, manufacturers now seek out aluminum that is stronger, more temperature resistant, and has superior casting qualities, such as improved flow of molten aluminum and resistance to heat cracking.
The most popular aluminum alloy used in casting right now is aluminum silicon (Al-Si alloy), which is easy to cast and has good corrosion resistance and weldability. Copper or magnesium are typically added to this kind of aluminum alloy to improve its properties. However, aluminum silicon also has the disadvantage of having a low level of heat resistance. This is what Asst. Prof. Dr. Promptong Pandee researched and developed it to become "Al-Ni alloy."
"Aluminum-nickel alloy (Al-Ni alloy) is a new kind of aluminum alloy created by mixing nickel with aluminum and has a high degree of structural stability. It is more heat-resistant than aluminum-silicon alloy."
When nickel is alloyed at a ratio of 6% of the total weight, an aluminum-nickel alloy with a eutectic temperature of 640 °C is achieved. However, because of nickel's poor fusion with aluminum, the matrix substrate of the aluminum-nickel alloy isn't very robust. Additional secondary alloying elements must be added in order to improve the mechanical properties even more.
The strength and tensile strength of aluminum-nickel alloys are tested using a variety of nickel ratios, and it has been established that this alloy is a promising one with good high temperature resistance.
The research of Asst. Prof. Dr. Phromphong Pandee and his team was published in Materials Science and Engineering Journal A, issue 709 in 2018, and Acta Materialia, issue 164 in 2019, and was further developed by Tesla, a manufacturer of electric vehicles, which was awarded a patent (WO2020/028730A1) in 2020.
‘Aluminum automotive parts’ are booming
Today's manufacture of automobile structural parts from die-cast aluminum is increasing rapidly, according to Bühler, a Swiss business with a global reputation as a creator of best-in-class process solutions along the whole value chain for healthy food and clean mobility. This is consistent with the requirement to lessen vehicle weight in order to consume less energy, hence reducing the release of carbon dioxide and other greenhouse gasses into the atmosphere.
To lighten the weight of the car, not only is the body construction of the car composed of aluminum, but it also integrates several sections into one. The battery housing is one of several components being developed in this fashion that will see a large rise in demand in the future.
In addition to reducing vehicle weight, these innovative manufacturing technologies also improve performance stability, strength, and safety to fulfill the demands of contemporary cars.
Future trends will result in a reduction in the number of vehicle parts. Vehicles with internal combustion engines typically contain over 2,000 moving parts, but electric vehicles only have 18 to 20 moving parts, which are produced using high-pressure die casting (HPDC) technology.
Die-castng components in vehicles
According to Bühler, the European market will have the highest demand for HPDC-produced auto parts by 2025, with 4.8 million units annually and average annual growth of 4%. China will come in second with 1.9 million units annually and average annual growth of 7%, and North America will come in third with 1.7 million units annually and average annual growth of 18%.
What is high-pressure die casting (HPDC)?
High-pressure die casting is a manufacturing method that involves injecting molten metal into a mold and then using high pressure to seal the mold until the metal hardens. High pressure casting reduces air bubbles in the workpiece by allowing the molten metal to enter the mold significantly more quickly than in traditional metal casting. Additionally, when injecting liquid metal into the mold, the volume must be sufficient to allow the workpiece to shrink to the appropriate size.
The HPDC method makes it possible to make thin parts. Therefore, it is employed to manufacture not only consumer goods, but also the structural components for cars and airplanes.
According to Mr. Wanchai Chutimavutikul, DC Appliction Specialist (SEA), Bühler (Thailand) Co., Ltd, 70-80% of aluminum parts are currently manufactured with HPDC method. Many manufacturers in Thailand use injection molding equipment for this method. However, some manufacturers may choose to use pre-owned equipment rather than make the costly investment in new machinery.
One of the drawbacks of using pre-owned equipment is that it produces a large number of defective workpieces. But since recycling aluminum is easy and low cost, manufacturers have chosen to downplay the significance of the large number of defective workpieces and recycle those to bring aluminum back in use.
However, global adaptation to climate change is currently accelerating, giving rise to a variety of measures to reduce greenhouse gas and carbon dioxide emissions. The recycling of this scrap is becoming a pain point for the foundry business that may be targeted. If the manufacturer decides to invest in efficient machinery, scrap will be at minimum or practically eliminated. The environmental issues of this industry will be lessened. It also improves the overall efficacy of production.
NG parts are recycled
Aluminum personnel development for future growth
Since "aluminum" plays such a significant role in the expanding electric vehicle age, people with knowledge of aluminum in numerous industries are undoubtedly in demand on the job market. So, King Mongkut's University of Technology Thonburi's Faculty of Engineering offers courses for students at various levels who desire to pursue studies in this particular field. It also offers short training courses, advisory services, “industry clinic” or testing and inspecting services for mechanical qualities of materials, for the public to prepare for the growth of personnel in the aluminum market.
Additionally, Assistant Professor Dr. Promphong suggests that those who seek to investigate and create novel materials or manufacturing methods can get subsidies from the government as well as consultation for the faculty of engineering.
The development of aluminum, the material of the future, is yet possible. Future aluminum development will mostly concentrate on enhancing aluminum's characteristics by combining new elements.