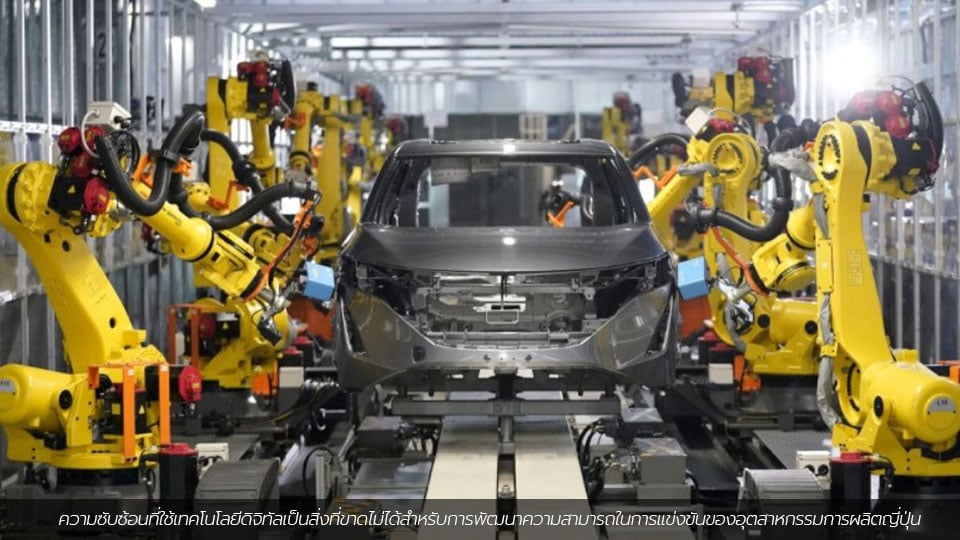
Japan White Paper 2023 warns of the necessity for digitalization
In the ever-changing world of manufacturing, Japan's 2023 White Paper on Monodzukuri emphasizes the vital role of digitalization in maintaining competitiveness.
Essential for Digitalization and Maintaining Competitiveness
The digital shift of the industry is forcing a change in the Japanese manufacturing industry. The advancement of digital technology has accelerated the horizontal division of labor. The competitive environment has changed with the emergence of new companies that utilize resources. Green Transformation (GX) - in order to realize this, the importance of sharing data beyond individual companies and group companies will increase. The Manufacturing White Paper 2023 warns that the promotion of digitization is required urgently to maintain the competitiveness of Japan's manufacturing industry.
Acceleration of Horizontal Division of Labor in the Manufacturing Industry: Knowledge, Know-how, Utilization of External Resources
The horizontal division of labor in the global manufacturing industry is accelerating. One of the backgrounds is the progress of digitalization and standardization of manufacturing processes such as production line design and on-site operations. Manufacturing that provides knowledge and know-how resisted on manufacturing to the outside via the cloud, with the advent of solution providers, barriers to entry into the manufacturing industry from other industries have decreased, and emerging companies are beginning to grow rapidly.
Vietnam's VinFast is one of the companies that has entered the finished vehicle business by utilizing these external resources. The company was established in 2017 by Vin Group, which operates a business centered on the real estate industry. Through the services provided by Germany's Siemens, etc., in their own factory, they introduced production lines and production technology comparable to those of major automobile manufacturers. VinFast, which does not have basic automotive technology, the factory was put into operation in 21 months. About half of the usual time. By 2025, the company plans to produce 500,000 units of electric vehicles (EV) annually.
In Japan, companies that develop services for the manufacturing industry are increasing their presence online, offering product procurement services, using artificial intelligence (AI). These include Misumi Group Headquarters, which develops and supports companies in shortening delivery times, and Arendt, which uses digital technology to convert expert know-how in plant design into explicit knowledge. It is expected to support the digital revolution (DX) of the manufacturing industry.
Up to now, Japan has established itself as a country that focuses on manufacturing through a vertically integrated business model that includes design development, manufacturing, and sales, and through the refinement of technology by field workers. However, in an environment where excellent technology can be procured from outside, is it possible to maintain competitiveness with intuition, tricks, and experience alone? The situation is unclear. There is a need for a flexible response that utilizes digital technology, such as concentrating management resources while assessing the company's strengths and utilizing external resources.
Another important issue facing the Japanese manufacturing industry, in order to maintain its competitiveness, is data linkage that transcends the boundaries of companies and groups.
In 2024, Europe will start a system to make it mandatory to disclose the carbon footprint (CFP) of carbon dioxide (CO2) emissions throughout the product life cycle for storage batteries sold in the region. If it is not possible to respond to CFP disclosure, it will be virtually impossible to sell products such as EVs and equipment with storage batteries.
According to the FY2023 Monodzukuri White Paper, only 4.4% of Japanese manufacturing companies have already taken steps to link data across companies to visualize CO2 emissions. In the Japanese manufacturing industry, business relationships are fixed between affiliated companies and group companies, and there was no need for data linkage beyond companies and groups.
Industry building a collaborative platform
Europe is leading the way in data linkage beyond the scope of individual companies. In April, Catena-X, a data linkage platform for the automobile industry developed primarily by German companies, was launched.
Over 100 companies constituting the supply chain, including BMW, Bosch, BASF, SAP, and Siemens, are actively participating. While it's an open platform, participating companies maintain data sovereignty. Additionally, the platform is encouraging companies beyond Europe, such as those in Southeast Asia, to join, with the aim of establishing new business models through data linkage.
In Japan, the Ministry of Economy, Trade, and Industry has initiated the 'Uranus Ecosystem' project to create essential infrastructure for data collaboration across companies and industries. The project is committed to promoting the utilization and sharing of data in diverse fields, including physical distribution, people flow, financial flow, and supporting the disclosure of Carbon Footprint (CFP) in storage batteries. It also ensures interoperability with overseas data linkage platforms like Catena-X, raising awareness both in Japan and overseas to prevent the emergence of isolated market phenomena. Our goal is to commence services by FY2022.
In the midst of a complex business environment fraught with uncertainties, including GX and economic security concerns, there's a risk of supply chain exclusion if data linkage is delayed. To optimize the supply network through data linkage, each participant in the supply chain must embrace digitalization.
#Monodzukuri #Japan #Manufacturing #Digitalization #Mreport #ข่าวอุตสาหกรรม
Source: Nikkan Kogyo Shimbun