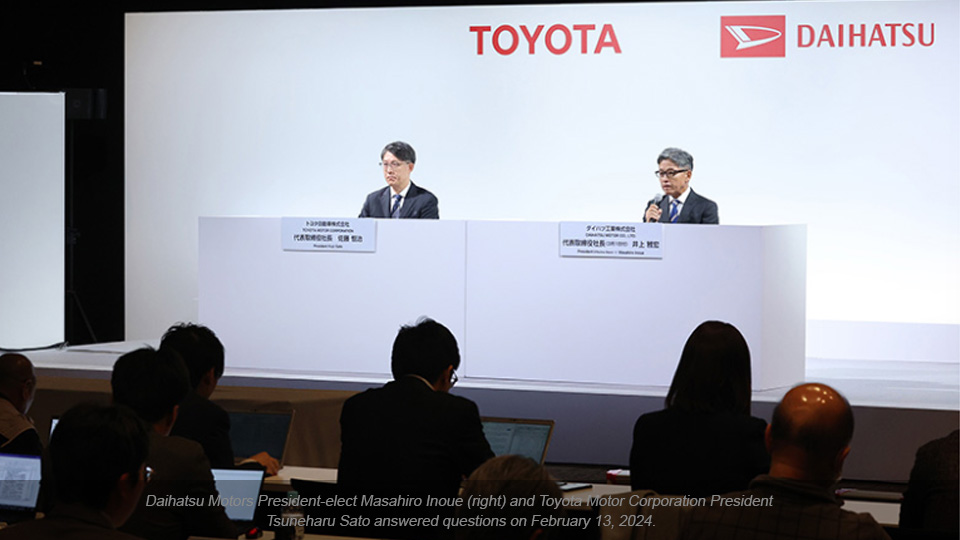
Japan’s Manufacturing Scene Is Fluctuating – Quality Is A Management Problem
Japan’s manufacturing sites are shaking. Quality fraud issues that have been exposed in recent years at Japanese companies such as Daihatsu Motor and Toyota Industries are losing trust in Japanese brands and shaking the foundations of Japan’s manufacturing powerhouse. In many cases, fraud at manufacturing sites is summed up as a lack of morals on the part of individuals, but where does the true nature of the problem lie? The nature of “management” is being questioned
“Industrial morality” necessary for top management
No matter how skilled you are, you will not be able to produce high-quality industrial products without “industrial morality.” Kotaro Honda is known as the “God of Iron” for developing the world’s first KS steel and served as the sixth president of Tohoku University. He said this at the opening ceremony of a company he was involved with. Honda called for “industrial morality,” among managers, saying, “If you guide the workplace with an eye toward industrial morality, the top and bottom will work as one, concentrically, and you will be able to manufacture high-quality products, at low prices.” A link between management and the field. He preached that superior products are achievable only when both aspects work in harmony.
What is currently happening at manufacturing sites in Japan? The tangible and intangible pressures on the field are increasing year by year. The “standardized mass production” that brought prosperity during the Showa era is now a thing of the past. With the diversification of customer needs, “mass customization” which applies mass production systems while making full use of the Internet of Things (IoT), is taking hold for products produced in a wide variety of products in small quantities. In addition, there are high targets that must be achieved under the slogan of shortening lead time, reducing costs, chronic labor shortages, and improving productivity. For the field side, the series of problems was an unfortunate event in which multiple conditions conducive to fraud occurred, and as a result, the responsibility of inaction on the part of management that led to fraud is grave. It is no exaggeration to say that quality fraud is a “Management problem.”
Daihatsu’s press conference was held in Tokyo on the 13th. Masahiro Inoue, who took the stage as the company’s next president, surmised the cause of the fraud, saying, “As the quality and quantity of our business expanded, we were unable to fully address the issues that were bothering us and we allowed the company to carry out business operations with unsolved issues. According to the recurrence prevention report and other documents, this is said to be the result of neglecting the burden on the workplace and overexerting themselves. Tsuneharu Sato, president of Toyota Motor Corporation, who was also present, said, “Corporate management is like running a marathon. Right now, we need to rebuild our structure, even if it means slowing down a little.” Although he was prepared for temporary delays in development and decreased productivity, he expressed his intention to prioritize reviewing management.
Quality fraud is a management problem. What should companies do? One is the review of “management quality.” The concept of management quality is unfamiliar in Japan, but its origins date back to the United States in the 1980s. The United States, whose international competitiveness has declined due to the offensives of Japan and Germany, thoroughly researches both countries and comes to the following conclusion. “Pursuing quality from the customer’s perspective, not quality from the company’s perspective.” In 1987, the “Malcolm Baldrige National Quality Award” (MB Award) was established, named-oriented management, which later led to the strengthening of the competitiveness of American Industry.
To spread management quality in Japan, we started activities with the Socio-Economic Productivity Headquarters (currently Japan Productivity Headquarters) as the leader. In 1993, a private study group centered on Toyota Motor Corporation and NEC began, and in 1996, the council was officially established.
Naoyuki Yanagimoto, who founded the Management Quality Council as a secretariat member at the time, said, “The aim was to instil in Japanese companies the quality improvement of “management” that can produce high-quality products and services, rather than the products and services themselves, “he recalls
The “Japan Management Quality Award.” Which can be called the #Japanese version of the MB Award.” Was established at the same time, and the awards have been held 28 times to date.” If customer value is not prioritized and management and the workplace work together, the efforts made at the manufacturing site will not lead to good management.” Yanagimoto, who currently serves as the council’s executive director, points out.
Nowadays, customer-oriented
It has been about 30 years since CS management started in Japan. Nowadays, customer-oriented management is taken for granted, and in addition to being forced to take various measures such as the environment, digital technology, and human rights, management aimed at shareholders, such as return on equity (ROE) management, is gaining momentum. This excessive pressure on management is distorting the form of manufacturing companies and creating distortions at manufacturing sites.
The spirit of industrial morality advocated by Kotaro Honda. Management and manufacturing sites must constantly communicate and integrate to produce quality products. Honda’s perspective expressed before the war has not faded to this day.
#Toyota #Daihatsu #Japan #QualityProblem #Mreport #ข่าวอุตสาหกรรม
Source: Nikkan Kogyo Shimbun