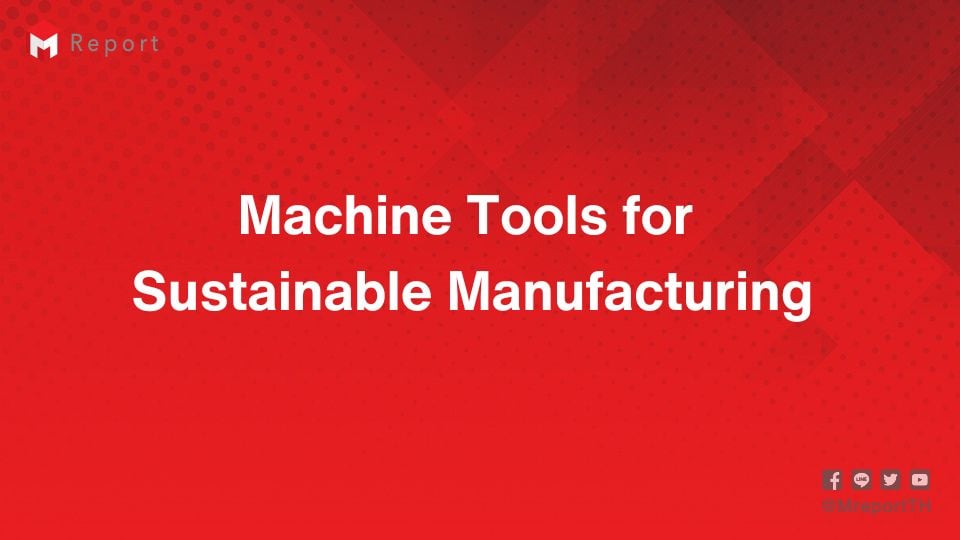
Innovation of the Future: Machine Tools for Sustainable Manufacturing
As the global population declines and labor shortages in factories become increasingly apparent, sustainable manufacturing is poised to become a major social issue. There is great expectation that the machinery and machine tools industry will play a key role in addressing this challenge.
To contribute to sustainable manufacturing, it is essential to anticipate the challenges faced by both users and society. This involves working backward from an ideal future state to propose valuable solutions—without being constrained by existing business boundaries or current technologies. Additionally, balancing the expansion of existing business with the exploration and introduction of new value requires organizational reform, such as redefining the company’s vision and actively leveraging external human resources.
Changing Business Environment
One of the most significant changes in the machinery industry is the labor shortage in the manufacturing sector, which is the primary user of machine tools. Although the global population has traditionally grown, it is now expected to peak and then decline. According to the United Nations World Population Prospects 2024, the global population is projected to peak in the 21st century. Furthermore, in 63 countries and regions—which collectively account for 28% of the world’s population, including Japan, China, Germany, and Russia—the population is expected to peak before 2024. In Japan, for example, the total population is projected to decline by 5% by 2034 and by 16% by 2050 compared to 2024, as estimated by the National Institute of Population and Social Security Research.
Employment Projections
Due to the declining population, labor shortages are expected to worsen. Data from the Japan Institute for Labor Policy and Training indicates that the number of employees in the manufacturing sector will decrease as follows:
- Under a scenario where per capita growth and labor participation remain unchanged, the number of employed individuals is expected to drop by 7% in 2030 and 21% in 2050 compared to 2022.
- Even in a scenario where labor participation increases gradually (through enhanced labor policies and other measures), the number of employees is projected to remain steady until 2030, but then decline by 7% by 2040 relative to 2022.
If productivity does not increase sufficiently to compensate for the reduced workforce, companies may struggle to secure the necessary labor, leading to an excessive workload for each employee. This could result in the downsizing or even closure of production facilities.
Social Impact and the Importance of Innovation
The loss of manufacturing sustainability carries broad social implications. Manufacturing not only contributes to societal wealth by producing high-quality, low-cost products, but also serves as a critical social function. It offers factory workers a sense of fulfillment and pride through innovative methods to boost productivity, while also providing employment opportunities that benefit local communities.
In the future, achieving sustainable manufacturing will become a key social issue, and there will be increasing expectations for machine tools as vital drivers of productivity in the manufacturing industry.
Looking Ahead: Anticipating Change and Delivering Value
Given these business environment shifts, what should the machinery and machine tools industry do? Beyond continuing bottom-up efforts to address everyday challenges and demands from machine tool users, it is crucial to:
- Envision an ideal future where sustainable manufacturing thrives even amid labor shortages.
- Employ a “backcasting” approach—working backward from the envisioned future to determine the value needed to achieve it.
- Present value to machine tool users and society in a way that anticipates evolving trends.
For example, one value proposition based on backcasting is to enhance the ease of use of machine tools. To mitigate labor shortages amid declining populations, it is necessary to design an environment in which groups that have not traditionally participated in the workforce—such as women and the elderly—can work effectively. Traditional machine tools are often designed for experienced operators and may not be user-friendly for these groups. In response, industries like robotics offer examples: Universal Robots in Denmark has developed robotic arms that can be controlled easily via a touchscreen tablet with simple arrow key commands. In the future, with the advent of generative AI technology, it might even be possible for users to command robots and machine tools using everyday language. Moreover, labor-saving measures are now being considered not only for the machine tools themselves but also for transportation devices that handle processed workpieces.
Organizational Reform and the Use of External Resources
To successfully deliver value through backcasting, companies must reform their organizational structures to achieve ambidextrous management—simultaneously deepening existing businesses and exploring new opportunities. Traditionally, the machine tools industry has grown by closely responding to customer demands, buoyed by a thriving manufacturing sector and abundant factory labor. However, as economies mature and labor shortages intensify due to declining populations, simply meeting current customer needs will no longer guarantee stable operations. Companies must continuously seek new value and pursue emerging business opportunities.
One way to challenge the status quo is to redefine the company’s vision—clarifying what the organization should become in the future. Historically, many machine tool companies have focused on quality and technology as their unique selling points. While continuing to improve these areas is important, companies must also articulate a vision that encompasses contributions to sustainable manufacturing and societal well-being, thereby broadening the scope of the value they offer. It is also essential to create opportunities for dialogue among employees at all levels (through executive retreats, town hall meetings, etc.) to ensure the new vision is fully embraced.
Given that in-house expertise in advanced technologies such as software and AI is often limited, leveraging external human resources becomes even more critical. Companies should actively recruit external talent and managers with the necessary skills rather than relying solely on developing internal resources. With growing societal demands for enhanced corporate governance, one option is to incorporate external directors into management through reforms such as adopting a committee-based system. Through these organizational reforms, the machine tools industry can better address the challenges of a declining population and contribute significantly to sustainable manufacturing and overall societal sustainability.
Article by
Nomura Research Institute, Global Manufacturing Consulting Department, Principal, Takanari Saito
Saito Takashige specializes in management reform in the mobility and manufacturing sectors, business strategy and business plan formulation, building new business models in the value chain sector, and implementation support including DX.